OLYMPIC
Lake Crescent Lodge
Historic Structures Report
|
|
III. DESCRIPTION OF EXISTING SITE AND BUILDING FEATURES
SITE
The grounds of Lake Crescent Lodge have several
remnant landscape materials and structures that survive in form,
material, and intent from the original layout of the grounds. The
overall spatial organization of the site remains intact. The grounds
slope approximately six percent from Highway 101 down to the lakefront,
some 400 feet north. Primary vehicular access to the site is off Highway
101 with major parking at the end of a short access road that ends
directly behind lakefront cottages numbers 676 through 680. Additional
parking is provided behind cabins 668-674 for overnight guests. The site
is provided with relatively new water and sewage utility services. Much
of the electrical service equipment on site is outdated and needs
replacement.
Many of the original plant materials remain on the
site, though many are decayed or in poor condition because of neglect.
While some new plant materials have been incorporated over the years,
the original structure of planting areas and massing has been
maintained.
As a whole, the complex displays relationships and
fundamental patterns of land use, circulation systems, building clusters
and use that have remained consistent through time without significant
spatial alteration. The original site design provided a variety of
experiences for the visitor. In a very small area the guest had a range
of spatial experiences from very public spacesthe entry path and
front lawnto semi-private areas in front of the
individual cabins, to very private areas on the porches of the cabins
and the cabins themselves. This pattern and gradation of spaces is still
evident and contributes much to the experiential quality of the site
today. In addition, most landscape and structural elements considered
primary to the character of the complex are intact, including the entry
and parking areas, path, building clusters and vegetation. Finally, it is evident that
the lodge and surrounding components provide a special link to the past.
There is a continuity and ambience that creates a quality and sense of
place and sets the complex apart from similar resort developments.
|
Figure 13. View of Lake Crescent Lodge from the shoreline.
Photograph by Marty Stupich, NPS, 1983.
|
|
Figure 14. Front entry facade (east elevation) Lake Crescent
Lodge. Photograph by Marty Stupich, NPS, 1983.
|
LAKE CRESCENT LODGE
Structural System
The foundation of the lodge consists of 6 x 6
wood posts atop one-foot square pre-cast concrete pads. Many of the
posts have wood shims possibly indicating earlier re-leveling attempts.
One post, now laying prone on the ground, should be repositioned under a
beam splice near the stone fireplace. Some of the posts under the later
addition of the lodge are raised from the concrete pads. In general, the
posts appear to be in good condition with little or no evidence of
insect rot or decay. Crawl space headroom from one foot to two feet is
found throughout the original building and later additions. Less crawl
space is found under the existing dining room and kitchen, although
access panels through the floors service mechanical spaces.
Spot elevations taken on the first floor indicate
considerable settlement. Using the stone fireplace hearth as a control
point, the following settlements of the main lobby were observed:
NE corner - 4 inches
SE corner - 5 inches
SW corner - 6 inches
NW corner - 4 inches
With the same control point, the following settlement
of the dining room area was observed:
NE corner - 3 inches
SE corner - 0.2 inch
SW corner - 3 inches
NW corner - 0.1 inch
In the tavern area, using the brick fireplace hearth
as a control point (3 inches lower than the stone fireplace hearth), the
following settlements occurred:
NE corner - 1 inch
SE corner - 4 inches
SW corner - 0 inches
It should be remembered that all three of these
portions tested for settlement were built at different times. A certain
amount of settlement under these conditions is not unusual and would be
acceptable.
The National Park Service commissioned preliminary
drawings and specifications for corrective foundation work at the lodge
by Systems Architects Engineers, Incorporated (SAE) of Seattle (drawing
file no. 149-80020, Olympic National Park). The work was never
executed due to funding shortages. Some of the work proposed by Systems
Architects Engineers will need to be reviewed in the context of current
conditions at the lodge before being incorporated into the
rehabilitation proposal now under consideration; however, it appears
that the requirements for stabilizing the original and 1950s addition
foundations will have changed very little in the intervening years. This report
concurs with a recommendation of the Denver Service Center that a
perimeter concrete stem wall with spread footings be substituted for the
strip footing with eight-inch diameter concrete columns recommended by
SAE. Continuing this stern wall around the portions of the lodge to be
retained will provide an enclosed crawl space capable of being
insulated, while also providing for lateral shear transfer from walls to
footings.
Wall framing in the historic Singer's Tavern
portion of the lodge is 2 x 6 wood frame construction 24 inches on
center. Wall construction of the remaining portions of the lodge is 2 x
4s construction at 24 inches on center.
The roof structure of the original lodge
portion is made up of 2 x 6 rough sawn lumber at 24 inches on center.
The roof has a two foot overhang with a 1 x 6 open soffit. Two by six
columns have been added in the attic to brace the rafters. A structural
evaluation of the roof was part of the Systems Architects Engineers'
preliminary report, which recommended adding structural members to
reduce rafter spans both in the original lodge portion and the later
dining room addition.
Aside from the noticeable foundation settlement, the
first floor appears to be in good condition. Gaps found around
the windows and the porch off the main lobby can be attributed to
foundation settlement. The stone fireplace has severely cracked,
starting at the right corner of the opening. This is probably due to
loads imposed at the beam pockets from the perimeter beams below, and to
the expansion of the steel lintel of the opening.
The condition of the additions housing the
kitchen, support areas and the dining room is marginal. Problems with
the roofing systems over these areas were addressed in the Systems
Architects Engineers' report mentioned earlier. The floor systems in
these areas are wood frame with concrete topping. They have deteriorated
considerably due to settlement and poor maintenance over the years.
No structural problems of immediate concern were
found on the second floor of the lodge. As with the first floor,
windows and doors are racked from foundation settlement. It should be
noted that the attic floor joists (second floor ceiling joists) are
lapped over the hallway walls below, with the joists lapping over
alternate walls. Therefore, both hallway walls are bearing walls. Room
partitions are non-bearing.
As in the first and second floors, windows in the
attic story are racked due to foundation settlement.
|
Figure 15. Southwest corner Lake Crescent Lodge. Photograph
by Marty Stupich, NPS, 1983.
|
|
Figure 16. South facade Lake Crescenet Lodge. Photograph by
Marty Stupich, NPS, 1983.
|
Building Exterior
The exterior skin of the building is painted cedar
shingles over 1 x 8 shiplap sheathing. A cedar shingle roof with metal
flashing is laid over a 1 x 6 roof deck eight inches on center. Wood
gutters are found on the original lodge portion with metal gutters on
other portions of the building. The entire roof system is in poor
condition and in need of major repair and replacement. The perimeter
wood foundation skirting shows signs of deterioration, particularly
where it is in contact with the soil, and will require major repair
and/or replacement.
Some minor exterior problems at the facility are
listed below; they were noted during recent inspections on site. The
list should not be considered comprehensive, but more a sampling of
general maintenance and repair concerns.
Veranda and porch decking nails are popping
and need to be reset and properly treated for paint.
Gutter downspouts are either clogged or
disconnected in many areas. Drainage water is not carried far enough
away from the building. Downspouts are two inches in diameter, which is
undersized for the surface to be drained.
Exit stairs on the south side of the complex
are unacceptable structurally and do not meet code requirements. Their
uninterrupted run is excessive, and the intermediate supports
inadequate.
The roof portions of added building sections
are poorly detailed and the cause of several maintenance problems.
The entire facility is uninsulated, including
surface exposed water and waste piping, making year-round use of the
present facility impractical.
Several routes of entry are currently open to
bats and other pests in all building portions.
|
Figure 17. Southeast corner Lake Crescent Lodge. Photograph
by Marty Stupich, NPS, 1983.
|
|
Figure 18. Dining Room Lake Crescent Lodge. Photograph by
Marty Stupich, NPS, 1983.
|
Mechanical Systems
The mechanical systems are functioning adequately,
although it appears frequent maintenance is required. The plumbing
system has a number of exposed and makeshift alterations and repairs. A
new water system installed in 1976 provides ample pressure and should
continue to satisfy the projected increased requirements of the lodge. A
new sewer system was also installed in 1976 and will service projected
increased capacities.
An automatic fire sprinkling system was installed in
the lodge in 1975. This four-inch system has been properly
installed and well maintained. However, there are some deficiencies in
the system: the crawl space is not sprinkled, and the distance from the
attic peak to sprinklers exceeds current code requirements.
Heating in the upper floor guest rooms and bath is
provided by 1500W electric baseboard heaters. The remainder of the
building is heated by tube panel ray heaters, gas floor space heaters,
and a LP gas suspended heater located in the main lobby of the lodge.
The three fireplaces in the facility provide some heat. There is
currently no central heating system. As noted above, the building is
completely uninsulated.
Other mechanical deficiencies in the building include
inadequate restroom facilities, no restroom ventilation, no discharge
pipe on the water heater's temperature and pressure relief valves,
improper propane-fired appliance venting with respect to clearances and
terminations, and fire sprinkler heads.
Replacement of most major mechanical systems on the
main floor of the lodge will be required as part of the proposed lodge
renovation.
|
Figure 19. Interior enclosed porch Lake Crescent Lodge looking
west. Photograph courtesy of Ellis Studio and Post Card Company,
Arlington, Washington, late 1920s.
|
|
Figure 20. Interior enclosed porch Lake Crescent Lodge looking
east. Photograph by Marty Stupich, 1983.
|
Electrical Systems
The lodge is fed by two overhead service lines from a
pole mounted single phase transformer rated at 7200-120/240 volt, with
primary fusing, and with metering on an intermediate pole midway between
the transformer pole and the building.
One service feed goes to a 400 amp fused switch
mounted on the outside of the southeast corner of the kitchen area, with
separate feeds to switches and breaker panels on the same wall to feed
loads in the building.
The second feed goes to another 400 amp fused switch
on the inside of the food storage room. An alarm and exit lights breaker
panel is fed from the line side of the switch, and from the load side
separate feeds go to circuit breaker panels on the interior wall, for
upstairs heaters and kitchen equipment.
Lighting in the main lobby is by incandescent lights
in suspended fixtures controlled by rotary switches beside the desk and
protected by a four-unit fuse panel on the stair landing. This
panel also provides protection for the second floor lighting, which
consists of a single incandescent fixture in the center of each room
with pull chain control. Each room also has a triplex receptacle at
floor level. Lighting in the attic is by incandescent lamps on porcelain
lampholders fed by knob and tube wiring on the roof. Supplemental
lighting in the lobby is provided by wall-mounted incandescent
fixtures fed from a knob and tube cable behind a wooden parapet. The
cable is spliced in various locations around the room and placed in
four-inch boxes for the connecting service. There are some recessed
receptacles in the lobby walls which feed additional wall and counter
lights. Dining room lighting is by six recessed flourescent fixtures
with control dimmer switches. Two of these fixtures were not
operating.
Electric resistance heaters are installed in each
bedroom, toilet, and bathroom upstairs, with individual thermostat
control, fed from a Square D load center on the stairs to the attic with
wiring distribution in conduit in the attic and conduit drops in the
exterior walls to each heater.
There is a secondary feed that goes from the fused
switch overhead to the meter pole to feed the cabins. Three-wire service
on spool insulators is hooked between cabins with a tap to a
two-fuse box on each cabin.
A smoke detector fire alarm system installed in the
building was supplied by Amex Security Corporation, Long Beach,
California. It consists of a control unit #ML24DS, battery,
and battery charger in the food storage room and detectors located in
the upstairs hallway, apartment, kitchen, corridor and office. The zoned
alarm panel is in the lobby beside the reception desk; a Faraday
fire bell #3440 is located in the upstairs hallway, lounge, and lobby.
Manual pull stations are located at all building exits.
Exit lights are installed at all exterior doors. They
are fed from a breaker in the same panel as the fire alarm system, which
is in the food storage room.
Load readings were taken on both incoming services;
the highest reading on one leg of the service to the kitchen area was
100 amps.
A completely new electrical system will be required
to accommodate projected improvements at the lodge, to replace obsolete
equipment, and to meet building code requirements. Current loading of
the system will have to be increased if an electric heating system is
chosen to service a year-round resort facility.
|
Figure 21. Interior Lake Crescent Lodge during the Singer era.
Courtesy of Kellogg Collection.
|
|
Figure 22. Interior Lake Crescent Lodge during the Singer era.
From University of Washington Pacific Northwest Collection
Post Card File.
|
Room By Room Description and Floor Plans
VERANDA #101
DIMENSIONS
EW 12'2' NS 48'3" ceiling 11'9"
FLOOR
Painted 5 3/4" x 7/8" random length hardwood EW
direction except NE corner where 45 degree joint turns boards NS until
they intersect wall
CEILING
Painted 3" 'V' groove boards across length of porch
then turned 45 degrees in NE corner
WALLS
W wall wood shingles (exterior siding) except
northern most portion that is wall of glass enclosed porch
Other "walls" 5 1/2" square post (1 each corner and 3
Intermediate across length) with 1 3/4" x 9 5/8" boards 20" from floor
running between posts except at open step portion
LIGHTING
Ceiling mounted incandescent fixture
ENCLOSED PORCH #102
DIMENSIONS
EW 55'0" NS 11'6" ceiling 11'9"
FLOOR
3 1/4" wide hardwood boards running in NS direction
with slope down, in N direction
CEILING
Painted 3"3 1/2" wide 'V' groove boards running
EW direction
WALLS
S wall (exterior N wall lodge building) painted,
machine sawn shingles
N wall is glass (see Illustration page for
configuration); 3 middle window bays have single paned sliding windows
in lower portion; all other windows single paned and fixed;
W wall was mirror image of E minus the doors; when
the sprinkling system was installed in 1975, the W wall was modified to
receive fire door by removing the three southern most windows; the door
is in the center of this opening surrounded by a wood framed shingle
wall
MOLDINGS
Base N, S, E walls type A; W wall type B
Ceiling type A
LIGHTING
Ceiling mounted incandescent fixtures
FEATURES
The porch was enclosed after the lodge had been in
operation for several years. This carefully executed modification gave
guests a sitting space with a most pleasing view of the Lake protected
from the area's often brisk winds.
LOBBY #103
DIMENSIONS
EW 54'9" NS 35'0" ceiling 13'10" (largest room in
building)
FLOOR
1/4" fir running EW direction
CEILING
Board and Batt 1" x 12" boards with 1/4" x 1
5/8" batts running EW direction
WALLS
2" x 6" frame construction with 1" x 12" boards
and 1/4" x 1 5/8" vertical batts
MOLDINGS
Base type C
Ceiling - batt material
Plate rail 7" wide; 9'4" from floor is found
throughout except at fireplace (photograph p. )
FEATURES
Two cloth tapestries in 3/4" x 3 1/2" wood frames are
found on the W wall between the door to the lounge and N wall (12'11 1/2" x
6'10 1/2"; 1'11 3/4" from floor) and in the stairwell to the second
floor on the S wall (9'6 1/2" x 4'8"; 7'8" from floor). Tapestries
appear to be original to building.
A stone fireplace 10'0" wide with 5'0" opening is
found on E wall. It has a tile and concrete hearth at floor level,
mantle and two tier chimney that is exposed the full height of the room.
One of four counters in the space appears to be historic. It is
located near the E entry to the building and is detailed compatibly with
other original building elements. The other counters are of a 1950s
vintage, probably installed after the facility was purchased by the Park
Service.
A telephone booth circa 1950s is found on the E wall.
HEATING
A propane heater hangs in the SE corner. Its
dimensions are 2'0" wide, 2'6" deep and 2'9" high and is 7'5" from the
floor
LIGHTING
Lighting is supplied by 7 18" diameter half globe
pendant fixtures (globe down) on 3 chains each; an eighth fixture has
been replaced by a flourescent fixture in the SW corner, smaller
multi-faceted, (resembling leaded glass) bracket-type sources are
located around the room 6'0" from floor height; wiring to these fixtures
is original complete with rotating type control switches
COMMENTS
A few minor alterations have occurred in the lobby over the years
nothing that is irreversible or of major significance. A general
settling of the foundation has cause noticeable sag in the floors and
racking of some of the doors and windows. Some exposed wire mold has
been added to the space over the years as well as an exposed fire
sprinkling system.
According to historic photographs (Fig. 21) much of
the original craftsmans style furnishings used in the lodge in its early
days are still found on site.
STAIRS #104
Lower flight 4'1 1/4" wide (wall to edge of tread) x
7'6 3/8" long (run) x 6'4 3/8" high (rise); landing 4'7 1/2" EW x 3'6
1/2" NS; upper flight 4'3" wide x 10'3" long (run) x 8'0 5/8" high
(rise); all with rubber treads
Baluster 1 3/8" square posts one per step topped with
simply detailed handrail
8" square newel post with minimum detail at ground
level, finial missing; plain 9 1/2" corner post extends to ceiling at
landing
STORAGE #105
DIMENSIONS
EW 9'4" NS 3'3 1/2" level ceiling under landing then
sloping under first stair flight to 1'6"
FLOOR
Same as lobby
CEILING
Plaster on plywood
WALLS
1/2" GYP, painted
LIGHTING
Single porcelain holder, bare bulb, pull cord on wall
DINING ROOM #106
DIMENSIONS
NS 31'8" EW 39'4" ceiling 8'8"
FLOOR
9" x 9" asphalt tile; off-white color
CEILING
2' x 4' accoustical tile in 'T' bar grid running
NS
WALLS
Vertical 4' x 8' blond wood panelling
MOLDINGS
Base - type C
Ceiling 3/4" x 6" boards positioned so 4 1/2"
projects below accoustical ceiling
FEATURES
The east window wall provides a pleasing view of the lodge grounds.
HEATING
2 propane wall heaters located on N and S walls
1'9" x 6" (projecting into room) 5'0" high with flues
running up surface of wall and penetrating ceiling
LIGHTING
2' x 4' flourescent flush mounted
COMMENTS
Windows in the E and S walls originally had
multi-paned transom windows (see photo page). These windows were
covered when the drop ceiling was installed.
SPRINKLER ENTRY CLOSET #107
DIMENSIONS
NS 3'0" EW 4'0" ceiling 7'9" sloping in E direction
FLOOR
Unpainted plywood
CEILING
Exposed 2"x4"s under roofing material
WALLS
N and S exposed batt insulation; W door; E exterior
shingles of building
LIGHTING
Single porcelain holder, bare bulb, pull chain
COMMENTS
This room is the entrance point for the main 4"
fire sprinkler service pipe.
STORAGE #108
DIMENSIONS
EW 6'10" NS 8'7" ceiling 7'11"
FLOOR
Unpainted plywood
CEILING/WALLS
Unpainted plywood
E and S floor to ceiling shelves
MOLDINGS
Base type D
Ceiling and corner type A
LIGHTING
Single porcelain holder, bare bulb, pull chain
COMMENTS
This room contains the main electrical service
panels and is also used for kitchen storage.
WALK-IN COOLER #109
DIMENSIONS
EW 5'9" NS 10'5" ceiling 6'8"
FLOOR
Painted concrete
CEILING
Painted plywood with 1/4" x 1 5/8" batts over butt joints
WALLS
Painted plywood (no treatment at butt joint)
MOLDINGS
Base/ceiling/corner type A
LIGHTING
Single porcelain holder, bare bulb switched on
outside near door
COMMENTS
Floor to ceiling wood shelves are found on the E, W
and N walls. The refrigeration unit is located
near the ceiling on the south wall. Piping and
wiring to refrigeration unit is exposed.
KITCHEN # 110
DIMENSIONS
EW 18'11" NS 24'4" ceiling S portion 7'9", N portion 9'4"
FLOOR
Painted concrete
CEILING/WALLS
Painted plywood (no. treatment at butt joints)
MOLDINGS
Base type E
Corner and ceiling type A
LIGHTING
Suspended flourescent fixtures
COMMENTS
The concrete floor has settled and is cracking
places. Exposed sprinkler pipes, both flex and conduit wiring is found
throughout. The amount kitchen equipment in place provides little room
work or circulation.
SERVICE ENTRANCE #111
DIMENSIONS
EW 6'8" NS 3'11" ceiling 9'4"
FLOOR
Painted concrete
CEILING/WALLS
Painted plywood (no treatment at butt joints)
MOLDINGS
Base type E
Ceiling and corner type A
EMPLOYEE'S LOUNGE #112
DIMENSIONS
'L' shape EW 11'11" NS 13'7" with 5'10" x 7'5" projection ceiling 7'9"
FLOOR
Painted concrete
CEILING/WALLS
Painted plywood (no treatment at butt joints)
MOLDINGS
Base types F and G
Ceiling and corner type A
HEATING
Cylindrical propane heater W wall
LIGHTING
Two single porcelain holders, base bulb, pull chains
COMMENTS
The concrete floor is badly deteriorated. Pipes,
conduit and flex wiring is exposed on walls and ceilings. A large
reach-in refrigerator unit is located in the SE corner and
partially blocks the door there.
STORAGE #113
DIMENSIONS
EW 7'1" NS 7'7" ceiling 7'9"
FLOOR
Painted concrete
CEILING/WALLS
Painted plywood (no special treatment at butt joints)
MOLDINGS
Base none
Ceiling and corner type A
LIGHTING
Single porcelain holder, bare bulb
COMMENTS
North and west walls have floor to ceiling wood shelves.
CORRIDOR #114
DIMENSIONS
EW 7'5" NS 13'8" ceiling 7'9"
FLOOR
Painted concrete
CEILING/WALLS
Painted plywood (no special treatment at butt joints)
MOLDINGS
Base type G
Ceiling and corner type A
LIGHTING
Incandescent pendant single bulb
COMMENTS
Exposed wiring is found throughout. The S door
has been removed because of placement of ice maker.
STAIRS #115
DIMENSIONS
EW 3'10" NS 10'3" ceiling rises to second floor
FLOOR
Tread and risers painted wood (see floor plan for configuration)
CEILING/WALLS
Painted plywood (no special treatment at butt joints)
MOLDINGS
Base type E, N wall
Ceiling and corner - type A
Handrails 1 1/2" diameter 2" from wall 2'7" from floor
LIGHTING
None
COMMENTS
Exposed pipe and wires are found throughout.
LIQUOR STORAGE #116
DIMENSIONS
2 spaces North EW 3'10" NS 2'8" ceiling
7'9" South EW 3'10" NS 7'2" ceiling exposed
to stair structure
FLOOR
North painted concrete
South 3 3/8" wood boards EW direction
CEILING
North painted plywood
South unpainted plywood, exposed ceiling
MOLDINGS
North ceiling type A on E side only
LIGHTING
Single porcelain holder, bare bulb, pull chain
each space
COMMENTS
The N room has floor to ceiling wood shelves on the E
wall measuring 1'7" deep. S room has floor to ceiling wood shelves 9"
deep on E and W walls.
RESTROOMS, MENS/WOMENS #117 AND 119
DIMENSIONS
Men EW 6'7" NS 6'10" ceiling 7'10"
Women EW 6'7" NS 7'4" ceiling 7'10"
FLOOR
12" x 12" vinyl tile
CEILING/WALLS
Painted plywood (no treatment at butt joints)
MOLDINGS
Base type F
Ceiling and corner type A
LIGHTING
Single porcelain holder, bare bulb
COMMENTS
Rooms are subdivided into two compartments with
plywood and wood frame screens that begin 6" above the floor and stops
6" below the ceiling.
CORRIDOR #118 & #120
DIMENSIONS
EW 11'8" NS 5'7" ceiling 7'9"
FLOOR
Painted concrete with rubber runner over
CEILING/WALLS
Painted plywood (no treatment at butt joint)
MOLDINGS
Base type G, NE corner; all other type H
Ceiling and corner type A
LIGHTING
Incandescent pendant single bulb
OFFICE #121
DIMENSIONS
EW 11'8" NS 15'5" ceiling 7'9"
FLOOR
Carpet over concrete
CEILING/WALLS
Stained plywood (no treatment at butt joint)
MOLDINGS
Base type G
Ceiling and corner type A
HEATING
Propane heater NE corner resting on floor, 1'11"
wide, 10'0" deep and 2'1" high flue rises vertically 3'0" and turns
horizontally to each
LIGHTING
2-4'0" flourescent fixtures surface mounted on
ceiling
COMMENTS
Exposed pipes and wires are found throughout.
LOUNGE #122
DIMENSIONS
EW 19'4" NS 21'4" ceiling 7'9"
FLOOR
Painted concrete
CEILING
4' x 8' sheets knotty pine; 1/4" x 1 9/16" batts EW
direction
WALLS
4' x 8' sheets knotty pine; 1/4" x 1 9/16" batts
vertical direction
MOLDINGS
Base type G
Ceiling and corner batt material
FEATURES
Centered on the W wall is a "common" brick
fireplace with a flush face, no hearth and 1" x 4" mantle 4'11" from the
floor.
South wall has a bar and back bar, EW 8'2" by NS
7'2 1/2" with a mirror on the wall above the back
bar.
LIGHTING
Wall mounted pendant type, with one or two fixtures
per bracket. All fixtures are controlled by a pull chain on each.
COMMENTS
Pipes and wiring are exposed throughout.
WATER HEATER ROOM #123
DIMENSIONS
EW 4'6" NS 8'4" ceiling 8'2"
FLOOR
2" x 10" boards NS direction with 1/8" crack between
CEILING/WALLS
1/4" grey asbestos panels
COMMENTS
This room contains three propane water heaters.
|
FIRST FLOOR (click on image for a PDF version)
|
CORRIDOR #201
DIMENSIONS
EW 54'11" NS 4'1" ceiling 8'8"
FLOOR
Carpet over plywood (historic hardwood floor was
removed when plywood installed)
CEILING
1' x 12" boards with 1/4" x 1 5/8" batts EW
direction
WALLS
1' x 12" boards with 1/4" x 1 5/8" vertical batts
MOLDINGS
Base type I
Ceiling and corner batt material
LIGHTING
2 pendant globes with individual pull chains
COMMENTS
This room has three risers at the E end leading to an
emergency stairway constructed in 1975. The landing at the door is 2'11"
long. The risers are wood and are 6 3/4" to 7 1/4" high and rise a total
of 1'9".
Sprinkler pipes are exposed throughout.
CORRIDOR #202
DIMENSIONS
EW 2'8 1/2" NS 11'6" ceiling 8'8"
FLOOR
Carpet over 3 5/16" wide hardwood EW direction
CEILING
1" x 12" boards with 1/4" x 1 5/8" batts EW
direction
WALLS
1" x 12" boards with 1/4" x 1 5/8" vertical batts
MOLDINGS
Base type I
Ceiling and corner batt material
LIGHTING
None
COMMENTS
Sprinkler pipes exposed throughout.
WOMENS TOILET #203, MENS TOILET # 204
DIMENSIONS
Womens EW 3'1" NS 4'6" ceiling 8'1"
Mens EW 2'11" NS 4'6" ceiling 8'1"
FLOOR
12" x 12" vinyl tile over wood floor raised 6 1/2" at
door (raised edge is flush with corridor)
CEILING
Painted plywood
WALLS
3 1/4" vertical 'V' groove board all walls except E
wall womens, W wall mens that are masonite; all are painted
MOLDINGS
Base/ceiling/corner type A
Base (mens) type F
HEATING
2'0" electric baseboard each room, womens W wall N
end; mens E wall N end
LIGHTING
Incandescent metal lamp holder, single bulb
COMMENT
Each room contains one water closet against the S
wall centered (EW) in room.
CORRIDOR #205
DIMENSIONS
EW 2'8" NS 4'11" ceiling 8'8"
FLOOR
Rubber runner over 3 5/16" wide hardwood EW
direction
CEILING
1" x 12" boards with 1/4" x 1 5/8" batts EW
direction
WALLS
1" x 12" boards with 1/4" x 1 5/8" vertical batts
MOLDINGS
Base type I
Ceiling and corner batt material
LIGHTING
None
MENS BATH #206, WOMENS BATH #207
DIMENSIONS
Mens EW 4'9" NS 6'4" ceiling 8'1"
Womens EW 4'4" NS 6'4"
FLOOR
12" x 12" vinyl tile over floor raised 6 1/2" edge is
flush at corridor
CEILING
Painted plywood
WALLS
3 1/4" vertical 'V' groove board except S walls that
are masonite; all painted
MOLDINGS
Base all type A
Ceiling and corner type A
HEATING
2'0" electric baseboard each room, mens S wall W end,
womens E wall S end
LIGHTING
Residential type glass box with 4 incandescent bulbs
inside
COMMENTS
Both bathrooms have 5'6 1/2" long. 2'6" wide, 1'10
1/2 high claw foot bathtubs against the common wall.
CORRIDOR #208
DIMENSIONS
EW 7'5" NS 3'6" ceiling 8'8"
FLOOR
3 5/16" wide hardwood EW direction with access panel
2'1" x 1'7" in middle of space
CEILING
1" x 12" boards with 1/4" x 1 5/8" batts EW
direction
WALLS
1" x 12" boards with 1/4" x 1 5/8" vertical batts
MOLDINGS
Base type I
Ceiling and corner batt material
LIGHTING
None
COMMENTS
SE corner of room has vertical riser for attic
sprinkling system.
STAIRS #209
DIMENSIONS
Lower flight 3'8" wide (wall to wall) 5'0" long
(run) 4'8" high (rise) 7 treads at 8 1/2' (+3/4" nosing) 8 risers at
7"
Landing EW 4'6" NS 3'9"
Upper flight 4'2" wide (wall to wall) 5'0"
long (run) 4'8" high (rise) 7 treads at 8 1/2" (+3/4 nosing) 8 risers at
7"
CEILING
Open to attic
WALLS
Board and batten (same as second floor corridors)
MOLDINGS
None
No handrails
LIGHTING
None
COMMENTS
This stairway leads to the third floor attic
and is closed to the public.
GUEST ROOMS #252 THROUGH 260
DIMENSIONS
Room widths (EW) vary from 8'8" (#257) to 11'2"
(#252); length (NS) is 14'10" N rooms, 15'1" S
rooms; ceiling heights 8'8"
FLOOR
3 5/16" wide hardwood EW direction
CEILING
1" x 12" boards with 1/4" x 1 5/8" batts EW direction
WALLS
1" x 12" boards with 1/4" x 1 5/8" vertical batts
MOLDINGS
Base type I
Ceiling and corner batt material
FEATURES
All rooms have one window (type ), except corner
rooms (#252, 259, 269) that have one on each side wall.
Some rooms are connected to neighboring rooms via a
common pass door.
Each room has a lavatory. 1'7 1/2" wide by 1'4 1/2"
deep projecting from wall.
HEATING
6'0" electric baseboard heaters under windows
LIGHTING
Incandescent ceiling pendants with pull chains
COMMENTS
Room #253 has a 4' x 10' cut plywood ceiling running
in EW direction and a 1'1" EW by 3'2" NS plywood panel in the floor at
the door. The flooring in this room was removed and reinstalled to
correct water damage. A 5'0" by 1'8" deep closet was added in the SW
corner.
MANAGER'S APARTMENT KITCHEN #261
DIMENSIONS
EW 8'10" NS 10'3" ceiling 8'0"
FLOOR
12" x 12" decorative vinyl tile
CEILING
Painted plywood, NS direction (no batts at butt
joints)
WALLS
Painted plywood, vertical direction (no batts at butt
joints)
MOLDINGS
Base - type J
Ceiling and corner - type A
LIGHTING
Single flourescent fixture
COMMENTS
The west wall has a 2'5" cased opening connecting
with the utility room. A 2'0" by 5'2" closet is found in the NE
corner.
MANAGER'S APARTMENT UTILITY ROOM #262
Same as kitchen (#261) except 2'0" by 4'9 1/4" closet
located in NW corner and lighting in ceiling is a single incandescent
bulb in a porcelain holder.
MANAGER'S APARTMENT WORKROOM #263
DIMENSIONS
EW 8'8" NS 14'7" ceiling 8'0"
FLOOR
Linoleum
CEILING
Painted plywood, NS direction (no batts at butt joints)
WALLS
Painted plywood, vertical direction (no batts at butt
joints)
MOLDINGS
Base type J
Ceiling and corner type A
LIGHTING
Ceiling mounted flourescent and incandescent
fixture
MANAGER'S APARTMENT CORRIDOR #264
DIMENSIONS
EW 17'7" NS 3'11" ceiling 8'0
FLOOR
Carpet over plywood
CEILING
Painted plywood, EW direction (no batts at butt
joints)
WALLS
Painted plywood, vertical direction (no batts at butt
joints)
MOLDINGS
Base type J
Ceiling and corner type A
LIGHTING
Ceiling mounted incandescent lamp holder
COMMENTS
An access panel to the attic is located in the W end
of the corridor. The panel is 1'0" off the W and S walls. Its dimensions
are 1'10 3/4" EW by 2'1" NS.
MANAGER'S APARTMENT BATH #265
DIMENSIONS
EW 11'3" NS 6'8" ceiling 8'0"
FLOOR
Carpet over plywood
CEILING
Painted plywood, NS direction (no batts at butt
joints)
WALLS
Painted plywood, vertical direction (no batts at butt
joints)
MOLDINGS
Base type J
W Ceiling and corner type A
HEATING
Electric baseboard
LIGHTING
Ceiling mounted incandescent lamp holder
COMMENTS
A divider between the shower stall and toilet, built
with 2'x6's and plywood projects from the E wall.
MANAGER'S APARTMENT BEDROOM #266
DIMENSIONS
EW 15'4" NS 13'4" ceiling 8'0"
FLOOR
Carpet
CEILING
Painted plywood, NS direction (no batts at butt
joints)
WALLS
Painted plywood, vertical direction (no batts at butt joints)
MOLDINGS
Base type J (without quarter round)
Ceiling and corner type A
HEATING
8" cylindrical propane heater centered on E wall
LIGHTING
Ceiling mounted incandescent lamp holder
COMMENTS
A 2'0" x 6'10 3/4" free standing closet is
located in the SE corner.
MANAGER'S APARTMENT LIVING/DINING ROOM #267
DIMENSIONS
EW 15'8" NS 20'4" extension SE corner EW 4'0" by
NS 6'3 1/2" ceiling 8'0"
FLOOR
Carpet over plywood
CEILING
Painted plywood with 1/4" x 1 1/2" batts NS direction
WALLS
Painted plywood with 1/4" x 1 1/2" batts vertical direction
MOLDINGS
Base type J (without quarter round)
Ceiling and corner batt material
HEATING
1'9" wide by 5'0" high propane heater partially
recessed (2" exposed) in E wall, N end
LIGHTING
Ceiling mounted incandescent lamp holder
|
SECOND FLOOR (click on image for a PDF version)
|
ATTIC #301
DIMENSIONS
EW 54'9" NS 35'0" ceiling to rafters
FLOOR
3 5/8" x 1/4" soft wood running in EW direction
CEILING
Open to rafters
WALLS
Open to framing
LIGHTING
Ceiling mounted incandescent fixtures
COMMENTS
Addition columns have been added to reduce the rafter
span of the roof framing. Windows are racked due to foundation
settlement.
|
ATTIC (click on image for a PDF version)
|
Elevations
|
EAST ELEVATION (click on image for a PDF version)
|
|
NORTH ELEVATION (click on image for a PDF version)
|
|
SOUTH ELEVATION (click on image for a PDF version)
|
|
WEST ELEVATION (click on image for a PDF version)
|
Doors
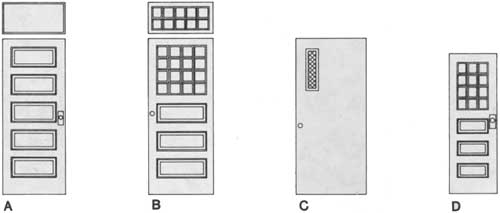
Feature Door Schedule
Door No. | Type |
Size | Description |
Lite Size | Trim Type |
Remarks |
101 | G | 2-2'6"x6'6"x1 3/4" | Wood | Clear Glass 6 1/8"x11 1/8" |
|
|
102 | G | 2-2'6"x6'5"±x1 3/4" | Wood | Clear Glass 6 1/8"x11 1/8" |
| No Transom Floor Slopes |
103 | G | 2-2'6"x6'6"x1 3/4" | Wood | Clear Glass 6 1/8"x11 1/8" |
| No Pane Hardware |
104 | E | 3'0"x6'8"x1 3/4" | Wood S.C. |
|
|
|
105 | P | 2'8"x6'8"x1 3/8" | Wood Panel | Textured Glass |
| w/Transom |
106 | R | 2'9"x5'8"x3/4" | 3/4" Plywood |
|
|
|
107 | H | 2-2'6"x6'6"x1 3/8" | Wood | Clear Glass 6 3/8"x5 1/8" |
|
|
108 | L | 3'0"x6'7"x1 3/8" | Wood | Clear Glass 5 7/8"x5 5/8" |
|
|
109 | F | 3'0"x6'8"x1 3/4" | Wood S.C. | Clear Glass |
|
|
110 | E | 2'8"x6'8"x1 3/4" | Wood H.C. |
|
|
|
111 | N | 2-3'0"x6'7"x1 3/8" | Wood S.C. | Clear Glass |
| Double Acting |
112 | A | 2'6"x6'4"x1 3/8" | Wood Panel |
|
| No Transom |
113 | F | 2'8"x6'6"x1 3/4" | Wood S.C. | Clear Glass |
|
|
114 | A | 2'6"x6'4"x1 3/8" | Wood Panel |
|
| No Transom |
115 | *J | 2'6"x6'6"x1 3/8" | Wood Panel |
|
|
|
116 | *J | 2'8"x6'6"x1 3/8" | Wood Panel |
|
|
|
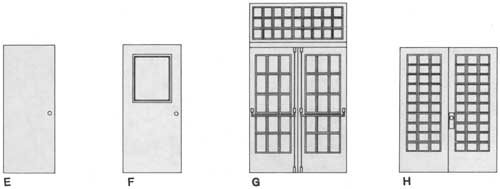 |
117 | Q | 2'6"x6'2"x1 3/8" | Wood Panel | Clear Glass |
|
|
118 | *J | 2'8"x6'6"x1 3/8" | Wood Panel |
|
|
|
119 | J | 3'0"x6'8"x1 3/8" | Wood Panel |
|
|
|
120 | J | 2'4"x6'5"x1 3/8" | Wood Panel |
|
|
|
121 | J | 2'6"x6'6"x1 3/8" | Wood Panel |
|
|
|
122 | J | 2'6"x6'6"x1 3/8" | Wood Panel |
|
|
|
123 | K | 2'8"x6'8"x1 3/8" | Wood | Clear Glass S 1/6"x5 3/16" |
|
|
124 | J | 2'8"x6'6"x1 3/8" | Wood Panel |
|
|
|
125 | J | 2'8"x6'8"x1 3/8" | Wood Panel |
|
|
|
126 | J | 2'11"x6'7"x1 3/4" | Wood | Clear Glass |
|
|
127 | R | 2'1"x4'7"x1" | 1" Plywood |
|
|
|
128 | P | 2'8"x6'8"x1 3/8" | Wood Panel |
|
|
|
201 | F | 3'0"x6'8"x1 3/4" | Wood S.C. | Clear Glass 1'11 5/8"x2'5 1/2" |
|
|
202 | A | 2'8"x6'8"x1 3/8" | Wood Panel |
|
|
|
203 | A | 2'8"x6'8"x1 3/8" | Wood Panel |
|
|
|
204 | A | 2'8"x6'8"x1 3/8" | Wood Panel |
|
| No Transom |
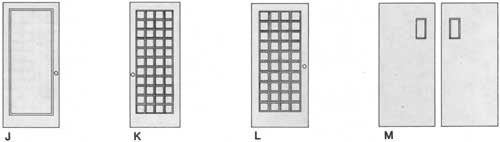 |
205 | A | 2'8"x6'8"x1 3/8" | Wood Panel |
|
|
|
206 | A | 2'8"x6'8"x1 3/8" | Wood Panel |
|
| No Transom |
207 | A | 2'8"x6'8"x1 3/8" | Wood Panel |
|
|
|
208 | A | 2'8"x6'8"x1 3/8" | Wood Panel |
|
|
|
209 | A | 2'8"x6'8"x1 3/8" | Wood Panel |
|
|
|
210 | A | 2'8"x6'8"x1 3/8" | Wood Panel |
|
|
|
211 | A | 2'8"x6'8"x1 3/8" | Wood Panel |
|
|
|
212 | A | 2'8"x6'8"x1 3/8" | Wood Panel |
|
| No Transom |
213 | A | 2'8"x6'8"x1 3/8" | Wood Panel |
|
|
|
214 | B | 2'9"x6 '8"x1 3/8" | Wood Panel | Clear Glass 5 5/8"x5 1/2" |
|
|
215 | C | 3'0"x6'8"x1 3/4" | Wood S.C. | Wire Glass 4"x1 '7" |
|
|
216 | D | 2'0"x6'0"x1 3/8" | Wood Panel | Textured Glass 4 1/2"x5 1/4" |
|
|
217 | D | 2'0"x6'0"x1 3/8" | Wood Panel | Textured Glass 4 1/2"x 5 1/4" |
|
|
218 | D | 2'0"x6'0"x1 3/8" | Wood Panel | Textured Glass 4 1/2"x5 1/4" |
|
|
219 | D | 2'0"x6'0"x1 3/8" | Wood Panel | Textured Glass 4 1/2"x5 1/4" |
|
|
220 | E | 2'7"x6 '8"x1 3/4" | Wood S.C. |
|
|
|
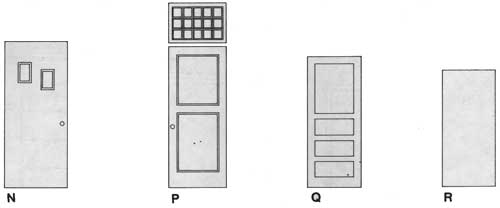 |
221 | P | 2'8"x6'5"x1 3/8" | Wood Panel | Clear Glass |
|
|
222 | J | 2'0"x6'6"x1 3/8" | Wood Panel |
|
|
|
223 | *P | 2'6"x6'8"x1 3/8" | Wood Panel | Textured Glass |
|
|
224 |
| 2'5"x6'7" |
|
|
| Cased Opening |
225 | P | 2'8"x6'8"x1 3/8" | Wood Panel | Textured Glass |
|
|
226 | J | 2'0"x6'6"x1 3/8" | Wood Panel |
|
|
|
227 | P | 2'6"x6'8"x1 3/8" | Wood Panel | Textured Glass |
|
|
228 | *P | 2'8"x6'8"x1 3/8" | Wood Panel | Textured Glass |
|
|
229 | P | 2'6"x6'8"x1 3/8" | Wood Panel | Textured Glass |
|
|
230 | P | 2'6"x6'8"x1 3/8" | Wood Panel | Textured Glass |
|
|
231 | P | 2'6"x6'8"x1 3/8" | Wood Panel | Textured Glass |
|
|
232 | N | 3'0"x6'11"x1 3/4" | Wood S.C. | Clear Glass 5"x8 7/8" |
|
|
Windows
Feature Window Schedule
Type |
Size | Description |
Lite Size | Trim Type |
Remarks |
A | 3'9"x4'7" | Casement |
|
|
|
B | 3'9 9/16"x6'7 3/4" | Casement W/Transom |
|
| Configuration Same as 'A' |
C | 3'3/4"x7'6 1/2" | Glass Display Case |
|
| Transom Same as Type 'B' |
D,E | 11'3 1/2"x8'8 3/4" | Type 'D' Sliders Type 'E' Fixed |
|
| 2 Center Panels Slide in Type D' |
F,G |
|
|
|
| Similar to D & E |
H | 3'1 1/8"x4'6" | Casement |
|
|
|
I | 3'1"x4'5 7/8" | Hung |
|
|
|
J | 2'8"x3'7/8" | Hung |
|
|
|
K | 4'7 5/8"x4'7" | Fixed (Picture) |
|
|
|
L |
|
|
|
|
|
M | 6'2"x4'7" | Fixed (Picture) |
|
|
|
N | 3'0"x3'10 1/4" | Hung |
|
|
|
O | 4'8 5/8"x4'7 3/4" | Fixed Sash |
|
|
|
P | 2'8 1/2"x2'10 1/8" | Hung |
|
|
|
Q | 3'1"x4'4 5/8" | Hung |
|
|
|
R | 2'3/4"x2'10" | Fixed Sash |
|
|
|
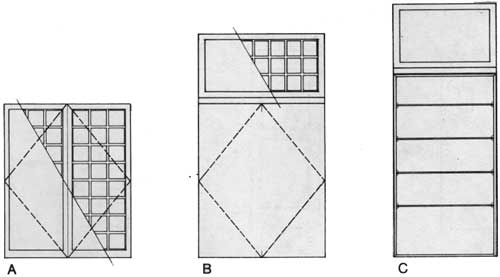
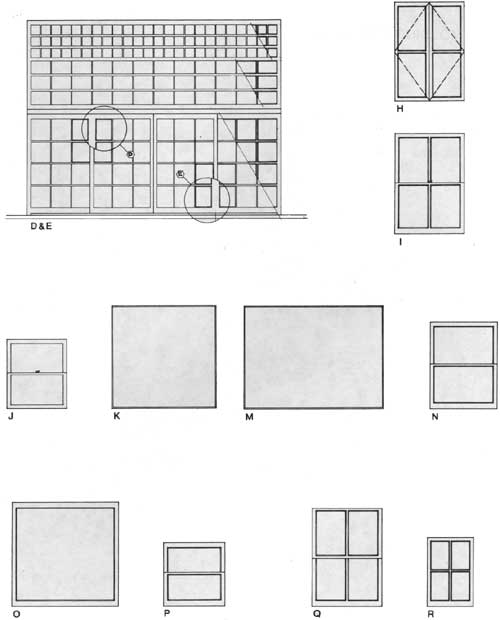
Molding Types
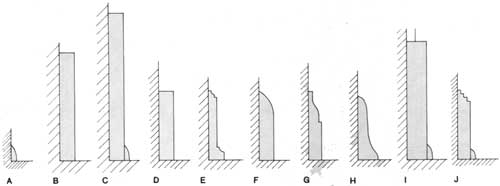
lake_crescent_lodge/sec3.htm
Last Updated: 23-Jul-2010
|