Last updated: December 14, 2021
Article
The Transfer Printing Process for Ceramics
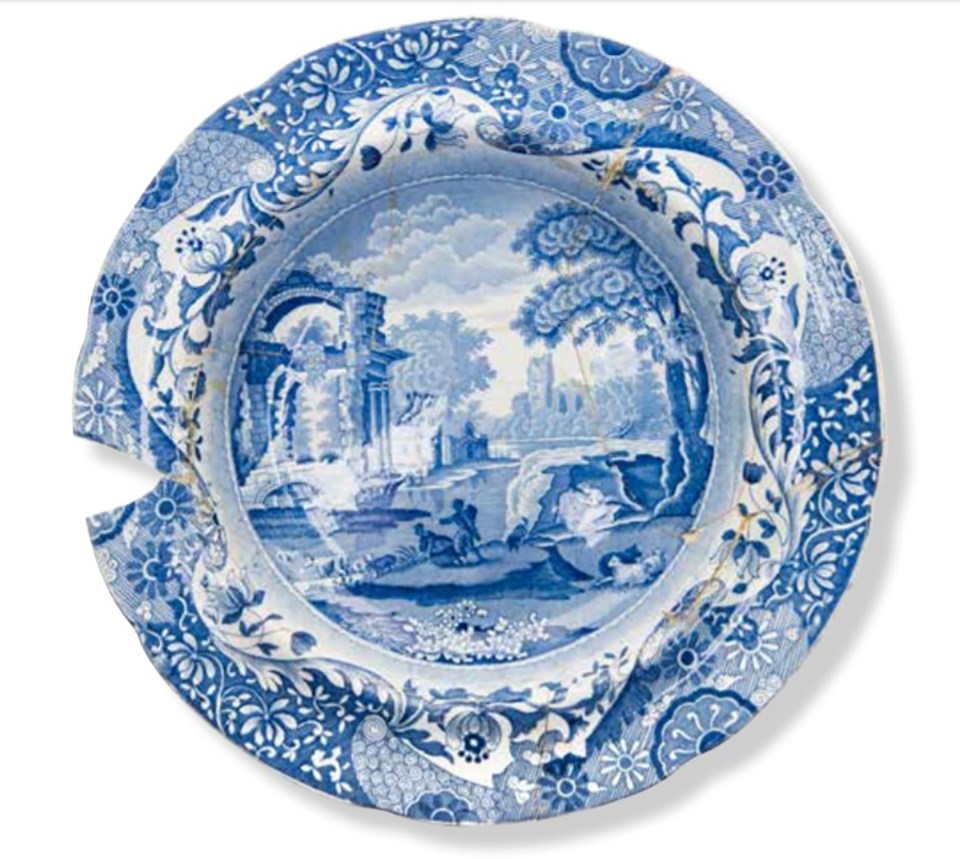
NPS Photo
Transfer printed ceramics are a common artifact type found at Fort Vancouver National Historic Site. Ceramic fragments often comprise almost 25% of archaeological assemblages from the fur trade era of Fort Vancouver (1825-1860), and transfer printed ceramics typically dominate. The transfer printed ceramics recovered during archaeological excavations and now in the national park's museum collection are almost 90& from one manufacturer: the Spode Company of Great Britain. The Hudson's Bay Company (HBC), the fur trade company that operated Fort Vancouver, had a nearly exclusive contract with the Spode Company to import their ceramics to the HBC's sites in North America.
The transfer printing process, involving transferring a design from an engraved copper plate to a ceramic vessel, is detailed below. The patterns engraved on the copper plates were used repeatedly to produce numerous tablewares. Many of these patterns have names and dates of production, providing archaeologists today with a catalog of information that can be used for artifact identification and site interpretation.
Transfer printing refers to the method of transferring a design onto an unglazed earthenware vessel after an initial firing.
To begin the process, an artist's drawing was engraved onto a copper plate. See pictures of copper plates used in the transfer printing process at the Spode Museum Trust here.
Then, color made from inorganic metallic oxides mixed with oils were rubbed into the hot copper plate, and the excess was carefully scraped off.
The copper plate cooled. Then, tissue paper specially prepared with a soap sizer was placed on the copper plate. The paper and copper plate were run through a press, forcing the paper into contact with every line of the drawing.
The copper plate was then heated once more, to dry the paper and soften the color. Then, the tissue paper was carefully pulled away from the engraving, now with the image of the engraving printed on it.
Sections of the tissue paper print were cut out and positioned on the ceramic vessel. The paper was held in place by the tackiness of the color. For a plate or bowl, the center design was placed first, then the border. The print was rubbed down with a brush lubricated with soft soap.
Scroll down to see what happened next!
The transfer printing process, involving transferring a design from an engraved copper plate to a ceramic vessel, is detailed below. The patterns engraved on the copper plates were used repeatedly to produce numerous tablewares. Many of these patterns have names and dates of production, providing archaeologists today with a catalog of information that can be used for artifact identification and site interpretation.
The Transfer Printing Process
Transfer printing refers to the method of transferring a design onto an unglazed earthenware vessel after an initial firing.
To begin the process, an artist's drawing was engraved onto a copper plate. See pictures of copper plates used in the transfer printing process at the Spode Museum Trust here.
Then, color made from inorganic metallic oxides mixed with oils were rubbed into the hot copper plate, and the excess was carefully scraped off.
The copper plate cooled. Then, tissue paper specially prepared with a soap sizer was placed on the copper plate. The paper and copper plate were run through a press, forcing the paper into contact with every line of the drawing.
The copper plate was then heated once more, to dry the paper and soften the color. Then, the tissue paper was carefully pulled away from the engraving, now with the image of the engraving printed on it.
Sections of the tissue paper print were cut out and positioned on the ceramic vessel. The paper was held in place by the tackiness of the color. For a plate or bowl, the center design was placed first, then the border. The print was rubbed down with a brush lubricated with soft soap.
Scroll down to see what happened next!
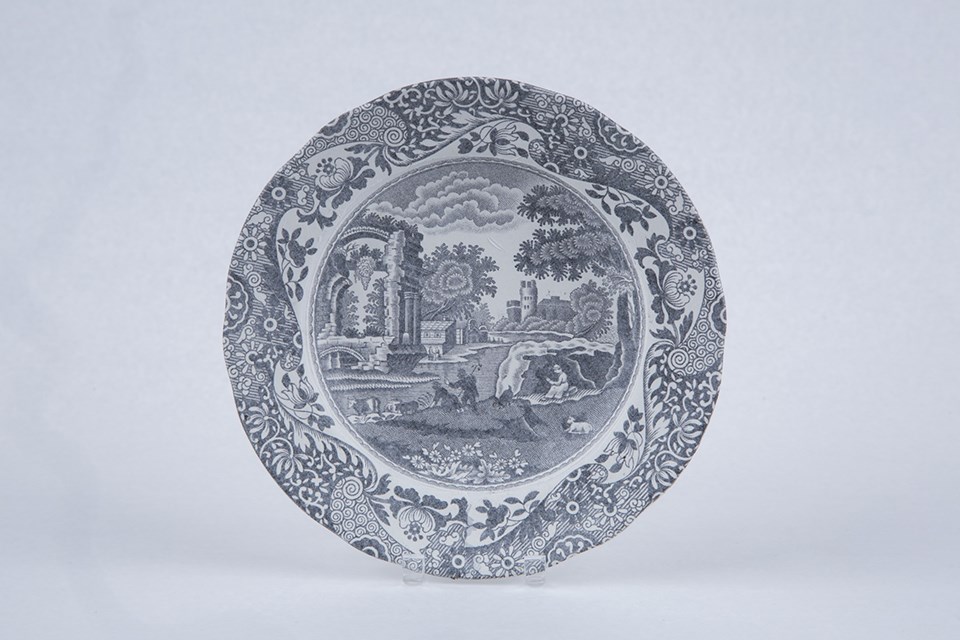
NPS Photo
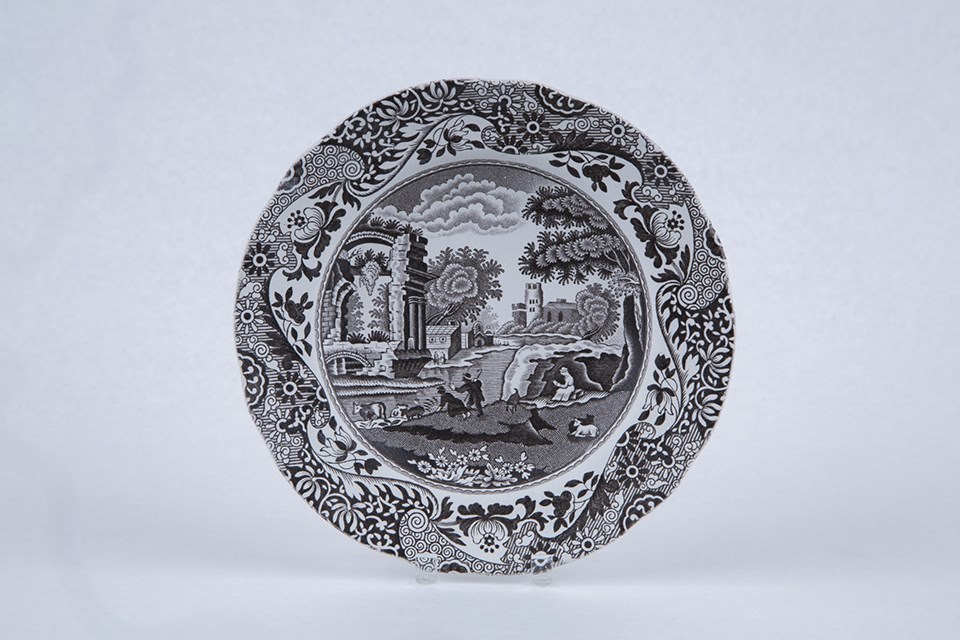
NPS Photo
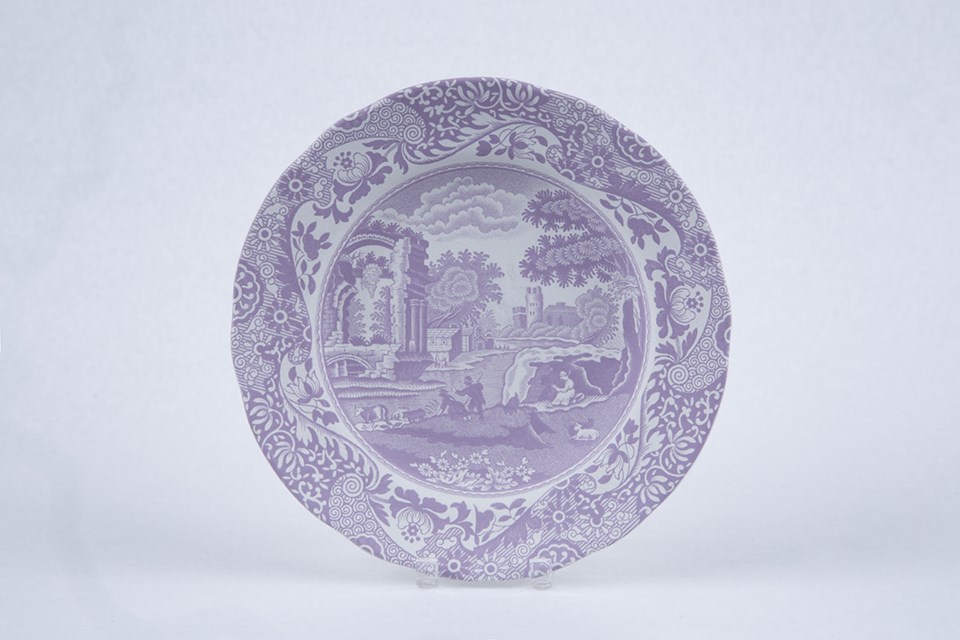
NPS Photo
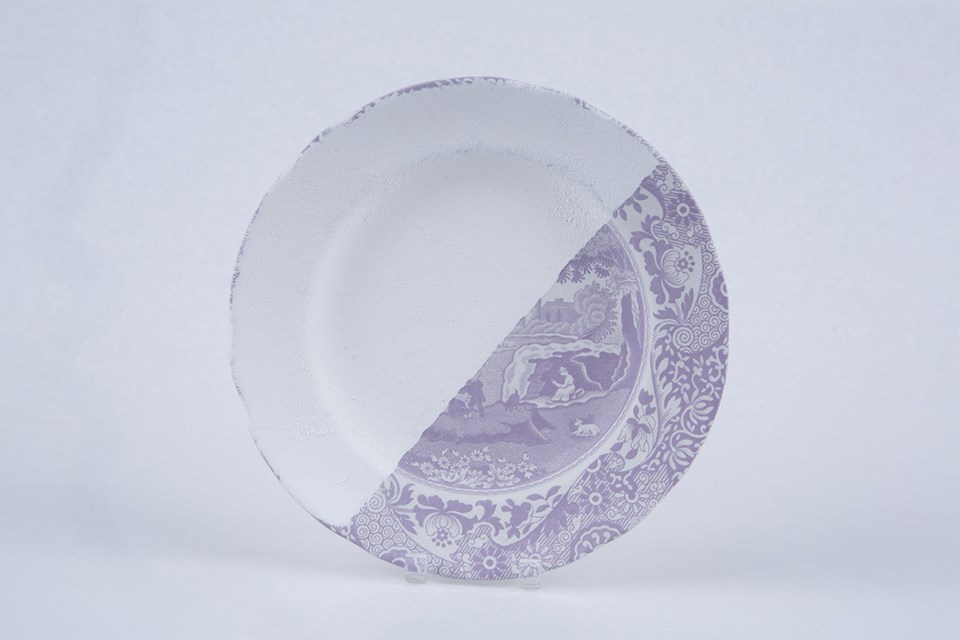
NPS Photo
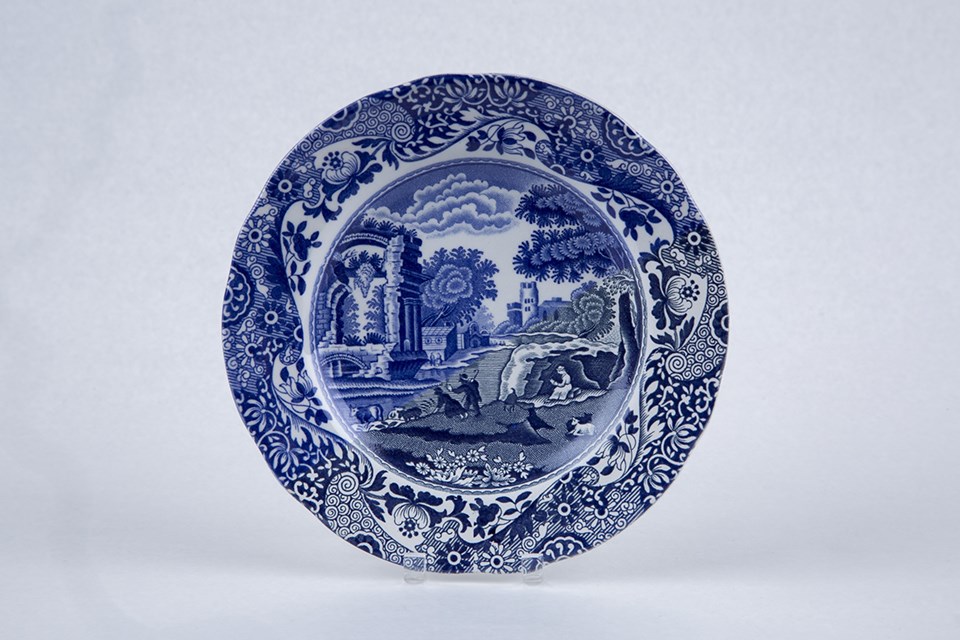
NPS Photo
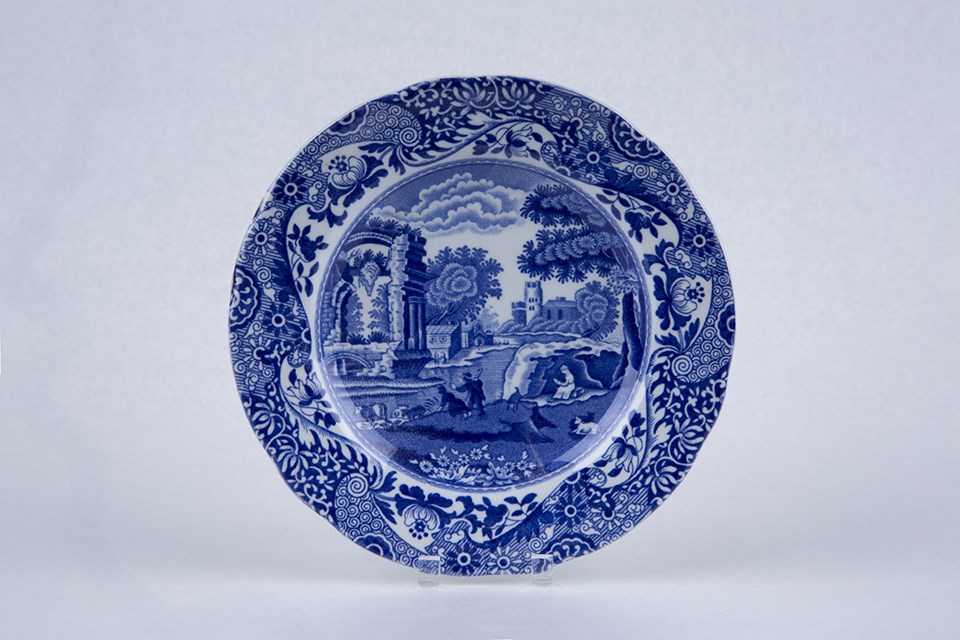
NPS Photo
Learn more about Spode!
See examples from the Fort Vancouver museum collection and learn more about Spode patterns.