Last updated: June 19, 2018
Article
Should I Replace My Slate Roof with a Synthetic?
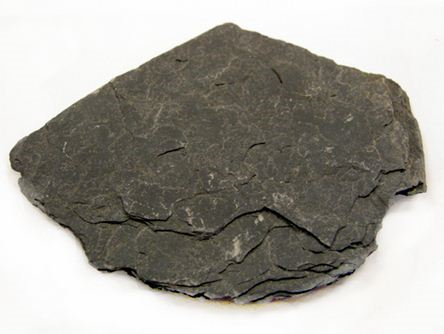
Photo courtesy of upenn.edu
What is Slate?
Slate is a fine-grained, foliated, homogeneous metamorphic rock derived from an original shale-type sedimentary rock composed of clay or volcanic ash through low-grade regional metamorphism (profound physical and/or chemical changes in the original rock structure). It is the finest grained foliated metamorphic rock. Foliation in geology refers to repetitive layering in metamorphic rocks. Each layer may be as thin as a sheet of paper, or over a meter in thickness. The word comes from the Latin folium, meaning “leaf,” and refers to the sheet-like planar structure. It is caused by shearing forces (pressures pushing different sections of the rock in different directions), or differential pressure (higher pressure from one direction than in others). The layers form parallel to the direction of the shear, or perpendicular to the direction of higher pressure. Because of the foliation or layering effect of these stones, very thin sections may be produced, giving way to a variety of uses, roofing “shingles” being only one such use. When broken, slate retains a natural appearance while remaining relatively flat and easy to stack. Also, when considering the material for use on a roof, one should note that slate has an extremely low water absorption index, less than 0.4%, which makes it resistant to frost damage.Slate is available in a variety of colors. The most common are grey, blue-grey, black, various shades of green, deep purple, brick red, and mottled varieties. The presence of carbonaceous matter, derived from the decay of marine organisms on ancient sea floors, gives rise to the black colored slates. Compounds of iron generate the red, purple, and green colored slates.
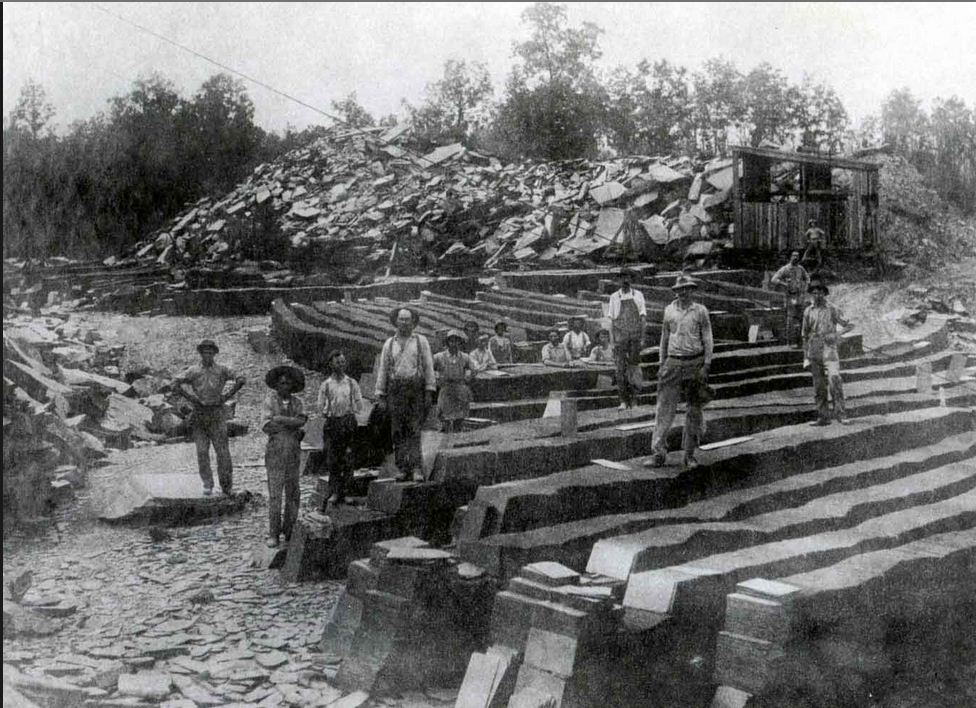
Photo courtesy of slateriver.wordpress.com
History of Slate Use in the United States
Although slate quarrying was not common in the United States until the latter half of the nineteenth century, slate roofing is known to have been used prior to the American Revolution. Archeological excavations at Jamestown, Virginia, have unearthed roofing slate in strata dating from 1625-1650 and 1640-1670. Slate roofs were introduced in Boston as early as 1654 and Philadelphia in 1699. Seventeenth century building ordinances of New York and Boston recommended the use of slate or tile roofs to ensure fireproof construction.In the early colonial period, nearly all roofing slate was imported from North Wales. It was not until 1785 that the first commercial slate quarry was opened in the United States, by William Docher in Peach Bottom Township, Pennsylvania. Production was limited to that which could be consumed in local markets until the middle of the nineteenth century.
Two additional factors helped push the slate industry to maturity; the immigration of Welsh slate workers to the United States and the introduction of architectural pattern and style books. Slate production increased dramatically in the years following the Civil War as quarries were opened in Vermont, New York, Virginia, and Lehigh and Northampton Counties, Pennsylvania. By 1876, roofing slate imports had all but dried up and the United States became a net exporter of the commodity.
The U.S. roofing slate industry reached its highest point in both quantity and value of output in the period from 1897 to 1914. In 1899, there were over 200 slate quarries operating in 13 states, Pennsylvania historically being the largest producer of all. The decline of the U.S. roofing slate industry began in 1915 and resulted from several factors, including a decline in skilled labor for both the fabrication and installation of slate and competition from substitute materials, such as asphalt shingles, which could be mass produced, transported and could be installed at a lower cost than slate. Only recently, with the increasing popularity of historic preservation and the recognition of the superiority of slate over other roofing materials, has slate usage begun to increase. Slate, laid in multicolored decorative patterns, was particularly well suited to the Mansard roofs of the Second Empire style, the steeply pitch roofs of the Gothic Revival and High Victorian Gothic styles, and the many prominent roof planes and turrets associated with the Queen Anne Style. The Tudor style imitated the quaint appearance of some English slates which, because of their granular cleavage, are thick and irregular. These slates were often laid in a graduated pattern, with the largest slates at the eaves and the courses diminishing in size up the roof slope, or a textural pattern. Collegiate Gothic style buildings, found on many campuses, were often roofed with slate laid in this manner.
Common types of sheathing used include wood boards, wood battens, and, for fireproof construction on institutional and government buildings, concrete or steel. Open wood sheathing was employed primarily on utilitarian, farm, and agricultural structures in the North and on residential buildings in the South where the insulating value of solid wood sheathing was not a strict requirement. To help keep out dust and wind driven rain on residential buildings, mortar was often placed along the top and bottom edge of each batten, a practice sometimes referred to as torching. On roofs with concrete decks, slates were typically nailed to wood nailing strips embedded in the concrete. Beginning in the late nineteenth century, asphalt saturated roofing felt was installed atop solid wood sheathing. The felt provided a temporary, watertight roof until the slate could be installed. Felt also served to cushion the slates, exclude wind-driven rain and dust, and ease slight unevenness between the sheathing boards.
Slate roofing tiles are still manufactured by hand using traditional methods in a five step process: cutting, sculping, splitting, trimming, and hole punching. In the manufacturing process, large, irregular blocks taken from the quarry are first cut with a saw across the grain in sections slightly longer than the length of the finished roofing slate. The blocks are next sculped, or split along the grain of the slate, to widths slightly larger than the widths of finished slates. Sculping is generally accomplished with a mallet and a broadfaced chisel, although some types of slate must be cut along their grain. In the splitting area, the slightly oversized blocks are split along their cleavage planes to the desired thickness. The splitter’s tools consist of a wood mallet and two splitting chisels used for prying the block into halves and repeating this process until the desired thinness is reached. The last two steps involve trimming the tile to the desired size and then punching two nail holes toward the top of the slate using a formula based on the size and exposure of the slate.
Historic slate roofs should be repaired rather than replaced whenever possible. All too often slate roofs are mistakenly replaced when, in fact, they could have been effectively repaired. Given the permanence of slate, it is poor economy to use anything but the most durable of metals and the best workmanship for installing flashings. Copper is one of the best flashing materials, and along with terne, is most often associated with historic slate roofs. Copper is extremely durable, easily worked and soldered, and requires little maintenance. Lead coated copper has properties similar to copper and is even more durable due to its additional lead coating. Lead coated copper is often used in restoration work.
The use of artificial, mineral fiber slate is not recommended for restoration work since its rigid appearance is that of a manmade material vs. natural. Artificial slates may also have a tendency to fade over time. And, although artificial slate costs less than natural slate, the total initial cost of an artificial slate roof is only marginally less than a natural slate roof. This is because all the other costs associated with replacing a slate roof, such as the cost of labor, flashings, and tearing off the old roof, are equal in both cases.
Replacement of a slate roof will be expensive; however, the superiority of materials and craftsmanship will give years of continued service. If amortized over the life of the roof, the replacement cost can be very reasonable. Over the long term, natural slate tends to be a better investment because several artificial slate roofs will have to be installed during the life span of one natural slate roof.
Originally published in "Exceptional Places" Vol. 8, 2013, a newsletter of the Division of Cultural Resources, Midwest Region. Written by Mark Chavez.
Condensed from the National Park Service (NPS) Preservation Brief No. 29, "The Repair, Replacement, and Maintenance of Historic Slate Roofs" by Jeffery S. Levine: http://www.nps.gov/tps/how-to-preserve/briefs/29-slate-roofs.htm.