Part of a series of articles titled Lowell, Story of an Industrial City.
Article
Lowell, Story of an Industrial City: Mill Power Drives
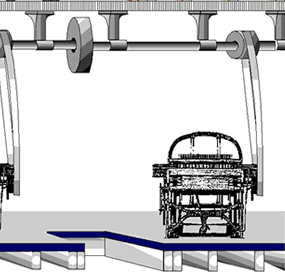
National Park Service
---
From: Dublin, Thomas. 1992. Lowell: the story of an industrial city: a guide to Lowell National Historical Park and Lowell Heritage State Park, Lowell, Massachusetts. Washington, D.C.: Division of Publications, National Park Service, U.S. Department of the Interior.
Last updated: June 15, 2018