For the equipment operators, the most challenging years are ones with snow so deep that you can’t see a trace of the road, but you find it by feel, or a subtle visual clue like brush you recognize from years of driving the road.
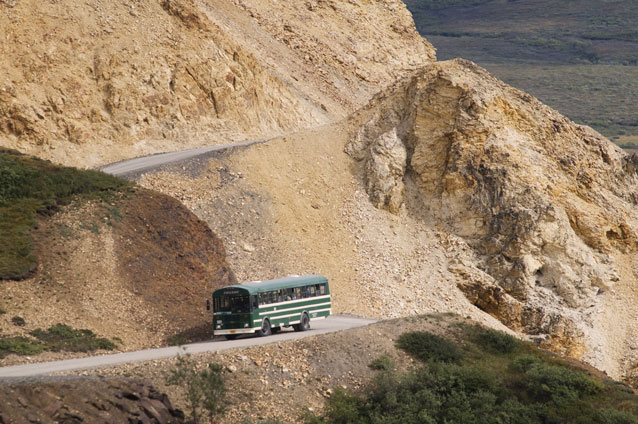
NPS Photo / Kent Miller
The road in Denali National Park and Preserve is unpaved for all but the first 15 miles and transitions to a single lane at mile 32 to preserve wilderness character and allow the free movement of wildlife in a more natural setting.
When the Alaska Road Commission (ARC) built the Denali Park Road (1922-1938), it combined landscape engineering suitable for northern environments with NPS aesthetic road design principles. The original ten-foot-wide (3-meterwide) gravel road with wooden bridges and ford sites possessed a rusticity that reflected its remote location. The road was blasted from rock and routed over passes to allow travelers to view expansive landscapes and vistas that, for the most part, are unmarred by the presence of the road itself.
Historical Significance and Character
The road is significant for its association with the period of scenic road development in national parks (1920s and 1930s), as well as for its association with the Mission 66 park development program (1950s and 1960s) when changes were made to the road corridor. The road was nominated to the National Register of Historic Places in 2013.
Natural and Human Forces at Work
Road operations and maintenance take three to five employees in winter and 26 to 30 employees, mostly seasonal, in summer. The annual cost of maintaining the park road is $1.9 million ($1.3 million for the unpaved portion) and includes the cost of 30,000 gallons of diesel fuel to run equipment, such as graders and bulldozers. A gravel road requires continuous maintenance and periodic replacement or addition of surface material to offset the losses from traffic, wind, and maintenance activities, such as grading and snow plowing. Maintaining the road with a crowned center is important to allow water to shed to the sides and protect the road structure.
Rain, snow, ice, wind, and vegetation all affect the road. Heavy rain and spring runoff erode road edges and wash out sections. Rain causes mudslides and rock fall and transports surface gravels to the road edge. Wind strips away surface binding material in the form of dust. Brush undermines the fill slope and road edge causing a false and soft road edge. Geologic forces such as slumps, landslides, and heaves, cover or move the road surface vertically and laterally. Much of the road was never constructed to carry the quantity or weight of vehicles that travels the road today. Bus traffic wears the road surface and stresses the subgrade causing soft spots and rutting.
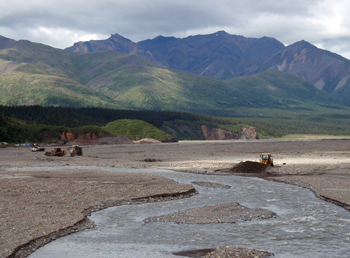
NPS Photo / Brad Ebel
Grading and Gravel
The road crew has placed an average of 6,800 cubic yards (5,200 cubic meters) of gravel on the road per year since 2005. The crew is still building road surfacing depth and crown from the years when no such material was available to the road crew. Some gravel is processed out of material extracted every other year from the Toklat floodplain by the park road crew. The curved scrapes to gather gravel mirror the natural channels in the braided river floodplain, so the visual impacts of these scrapes are as short-lived as possible. Using in-park gravel reduces traffic bringing gravel into the park, reduces the cost of extraction and processing, and already includes the addition of a binder.
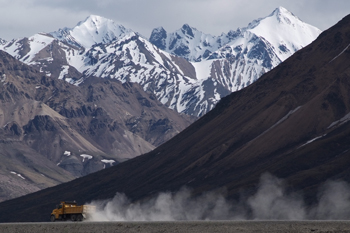
NPS Photo / Rob Parenti
Keeping Dust Down
On dry summer days, dust is kicked up by each vehicle on the park road. Calcium chloride (CaCl2) is a dust suppressant that stabilizes the road surface, conserving the cost of adding replacement road surface materials, and reducing the negative impacts of dust on visitors, vegetation, and wildlife. About 100 tons of CaCl2 is applied each year. The downside of CaCl2 use is its cost to buy and apply and its potential adverse impacts to soils or vegetation when it leaches off the road.
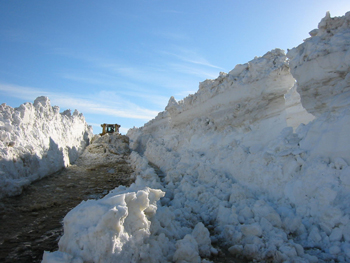
NPS Photo
Opening the Road in Spring
During Spring Road Opening, road supervisors manage an operation that begins in mid-March, or earlier, and goes to mid-May, running seven days a week. It involves keeping 10-12 staff performing safely, using up to six pieces of heavy equipment, a steam truck, a generator, and numerous support vehicles and other equipment.
- Plowing snow
There are “snow” years and “ice” years. If there is a lot of snow to plow, there is less ice to rip away, and vice-versa. In a snow year, crews will encounter drifts of 15 feet (~5 meters) deep on Sable and Polychrome passes, and sustained drifts of this size west of Toklat—at Highway Pass, Stony Hill, Thorofare Pass, and Eielson Bluffs. In these areas, there may be a half mile or more with a consistent 10-foot (3-m) depth. At Mile 60.5, drifts can reach 20-foot deep, which can take an entire day to remove.
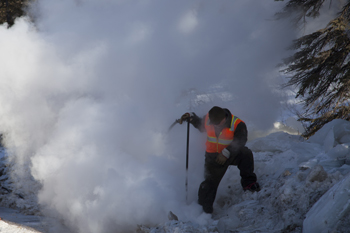
NPS Photo / Daniel Leifheit
- Steaming culverts
The road crew uses steam to open 200 culverts each year, some of them more than once during the freeze/thaw of spring breakup. Many culverts have been fitted with lines of pipe where steam is injected. It takes 3-10 hours to open a culvert. Steaming culverts is both a science and an art. For example, knowing how to use the boiler, and knowing by feel what is a rock or culvert joint and how to steam around it with a piece of straight rigid pipe.
Legacy of the Road Continues
To provide safe passage for traffic, yet retain its character, park staff plan for the needed resources (funding and staffing) to tend and maintain the park road—season after season, year after year.
Last updated: April 2, 2019