Last updated: April 7, 2025
Article
The Knapp’s Centre: 1930’s Art Moderne Icon Reinvented
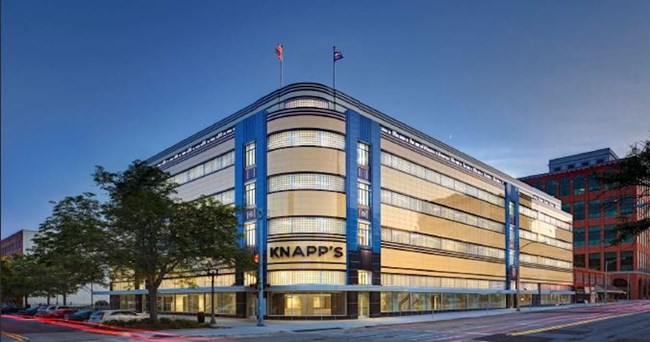
Quinn Evans Architects
Adaptive Re-Use
Bradley R. Cambridge: All right, thank you everybody. I did want to say to, I think the last ten years that I kind of focused a little bit on adaptive reuse. Being in Detroit a lot of properties we have there now really going to the resurgence and so the last ten years I’ve kind of been able to focus in Michigan and taken so of these iconic historic buildings and re-purposing them for new uses.
Today what I want to touch about is the Knapp center and then these are the AIA which I put in here and really nobody else has done them so I will skip through them. Knapp center is located in downtown Lansing Michigan it is about eight floors when you start counting the mezzanine and the basement floor and then the pent house mechanical level, for about a total of 200,000 square feet total.
Construction costs were about 20 million, and it was designed as a downtown department store in the mid 1930s. The map kind of shows item number one here as where Knapp is located. It was actually designed by, I going to pronounce it wrong, by Bowd Munson. Who also designed just up the river the Ottawa power street station which was designed about ten years earlier, and then a relationship right number two is actually the state capital of the state of Michigan.
The Knapp center is actually part of the Washington square retail district- kind of their main retail area and so it was the primary downtown department store when everyone went downtown for their retail shopping and stuff like that. It opened up in 1938 and in 1948 it went through a big expansion. The interesting thing is while the exterior looks exactly the same, you can’t tell a difference from the interior that it was two different types of structures. We’re going to focus on the 1937 structure because it’s a little more interesting but the 1948 structure really was kind of the same panel system but really adhered to a clay tile back up system so the two totally different structural systems from the exterior and we’re going to focus on the 1937 portion of it.
Complete Gut Renovation
The project scope over all was a full complete gut renovation in terms of exterior skin, interiors, as it was developed as a department store in the 1980s then the department store moved out and the state of Michigan came in and filled it all with offices. So the interior with the exception of a few iconic little areas was pretty much already gut and rehab back in the 1980s. There really wasn’t much interior stuff left. The exterior really was just kind of maintained as was, all of the original material was still on the building but it had been there for 75 years and very little maintenance had been done to it.
The project did receive state and national historic tax credits along with kind of the enhanced tax credits the state of Michigan had at the time. But today we’re going to focus on the exterior envelope of the building, more specifically two components, the what we kind of call as the rain screen panel system, which was a Maul Macotta panel system and then the glass block which was used as the ribbons to provide light into the retail area of the department store and then a couple of things at the very end some of the historic K-panels the steel windows and some store front framing. But you can kind of see here the highlighted orange section is where the Maul Mocatta panel rain screen system was and this is kind of where the steel windows and the decorative k-mountings were with the kind of glass block ribbons running each direction.
So when we got onto the project site this is really what it looked like. It’s basically a corner lot, the back two sides are against a property line so those were just basically brick construction which actually was in good shape. Facing Wasna and Washington Street were these Maul Macotta panel system which at the time was kind of referred to as one of the most iconic art deco buildings in Michigan and actually in the mid-west.
Building Materials & Component Failures
This is some of the failures we ran into. You can kind of see in the photo on the left hand side here the metal panels that had slide off the concrete, concrete panels that were completely missing. And then when you actually ripped off the interior wall, you could see that the concrete was eroding from the inside as well, leaving exposed steel reinforcement and even in some areas over here you can briefly see the back side of the metal panels. From the outside you can see all of the individual glass blocks that had been taped over, patched, or somehow trying to prevent water from getting inside as a lot of the glass block also had failed. That was kind of the condition we saw the building when we got there.
Rain Screen System
So first let’s kind of focus on the rain screen system, we’ll talk about kind of the technicalities of what failed and how it was designed and why we think it failed and then the proposed new systems to replicate it. So this is the Maul Mocatta panel system developed by the Maul Mocatta company, I don’t think in business anymore, in all of our research I couldn’t find a phone number or anything like that. But essentially it was this concrete panel that was hung or supported off a series of steel girds, and in reality it really was kind of an early curtain wall system.
We have this metal panel kind of right here in the middle and on one side it was finished with a porcelain enamel finish and then the back side was the raw material. What then wrapped that metal panel then was an aluminum trim band and then the panel then was backed with concrete. And the way they adhered the concrete to the panel was all of these individual copper clips that were welded to the back of the metal panel prior to the panel being finished and then the aluminum trim then had kind of a- I almost refer to them almost like a dry wall B. Kind of an edge to it, then that the concrete could form into. So essentially you’re kind of creating a concrete form work for the concrete to rest in.
Then what it did was it actually sat on a series of steel angles and then followed up with a bunch of steel clips that were bolted into the back side of the concrete and basically this just hung off of the base of the building. The steel was attached to a separate concrete structure that was traditional but this really was kind of the first rain screen system.
Rain Screen & Wind Barrier
Looking at the historic drawings the interior finish was nothing but plaster so as we started getting into the details we realized there really was no rain screen or really no wind barrier, water barrier. There was no insulation in this historic system and so you started to understand how it really was constructed and how it had developed over the years. When we got to the site we realized that every single joint was caulked, so these panels were basically side by side butt end to butt end and what they had done is every single one of those aluminum trim panels they caulked that thing.
Which prevented water from getting in but also prevented moisture from getting out and then also in the 1970s when the project went through some rehab and I guess in the 80s too when the state came in, they then furred out the walls and put in insulation because there was no insulation, sort of make it a little more comfortable they did that. Our understanding really was they kind of started trapping moisture in the building and going from there.
The steel structure really was a bunch of vertical H-sections and then off of that a whole bunch of steel horizontal beams for all of the panels to sit in. Apparently the highlighted areas have slid but if you look over here you can kind of see where the ribbon glass blocks sat, they sat on the steel and then in these areas here where we kind of have all of the additional steel that is where the concrete panels then sat.
When you got to these big monuments actually there was a brick backing and you can kind of see the coins back there, that is where the panels actually rested and sat and that’s how they then attached the panels at those brick coins to the supports.
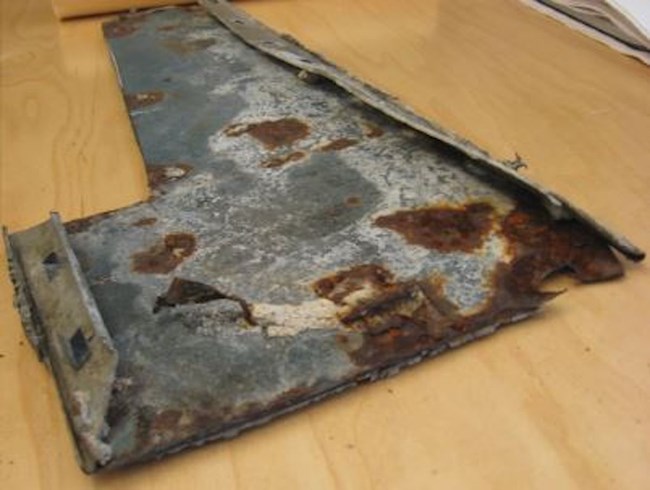
Quinn Evans Architects
Materials After 75 Years In-Situ
So these are what the metal panels looked like when we kind of started taking them off. You can start to see rusting points on the back side and while copper doesn’t rust what they use to adhere the copper to the metal panels did rust. So the panels that we started seeing falling or the metal that we started seeing falling from the concrete that’s because these panels actually rusted enough that the weight of the metal panels- because the metal panels themselves probably weighed close to thirty pounds as they were quite large, would actually shear off the concrete. You also start to see you had some issues with deterioration and rusting along the edges, rusting within the porcelain enamel finish and then you can kind of start to see here the edge aluminum trim as it was damaged and caulked over and stuff like that.
We are trying to understand how we can now restore these materials. We had a plethora of different materials or a plethora of different conditions of this material. One way obviously was can we take the concrete off the back of the metal panels, keep the metal panels that are in good condition and then fabricate new metal panels to match. Well it became an issues of how do we attach. I couldn’t weld anything new to the back of the metal panel because that would heat up the metal panel enough that would damage the porcelain enamel finish so that option was out. The second option was then to mechanically fasten from the outside going back in, the problem with that was you would see then all these restored panels that would then have mechanical fasteners all the way around the perimeter to keep the metal anchored. So that really wasn’t an option that we really wanted to go down either.
The second option was to fabricate all brand new porcelain enamel panels and there are companies out there that do porcelain enamel panels, you’ll see them a lot on retail development stores that type of stuff. Porsche uses a lot of them in their high end design stores. So getting a metal panel today is easy, the problem was we couldn’t get one with the aluminum trim edge. Companies don’t do both of those, so one option was to either A pre drill the holes and try and get another company to match the holes and every panel was a bit different sizes and it became a kind of a coordination nightmare to get one company to do one thing, ship it off to another company to do the other thing in hopes that everything align and then to put it on the building in hopes that everything looks good.
So once we realized that we couldn’t kind of one stop shop this thing and kind of guarantee to the owner in the end that you’re going to have a building that looks good, we ended up going down the third route which really was full, full replacement. So this is just kind of an image of them removing the concrete backing from the back of the panels, panels that were actually in good enough condition we’ve actually donated them to an art site and so they are trying to come up with some art sculpture of some sort to try and use the panels in some way or form. So this was kind of the cross section area of the details. You can kind of see here this is the historic side, this is what we kind of submitted into the state for the tax credits, but you can see how the panel kind of integrated in with the steel angles and then a couple of things I wanted to point out here is the dimensional here of the glass blocks sitting back from the inner of the panel and then over here I kind of have the overall panel width. The panel with the new system had to grow a little bit, so we were really concerned about making sure that these sight lines relatively stayed in place because we could not adjust the glass block location because it sat on the steel.
Our original designs was really to remove all of these intermediate steel angles that weren’t necessary, come in with a new structural steel wall that sat on the existing concrete and then hang off a new rain screen system off of that. That basically pushed the boundaries out about an inch and a half greater than what it was but we kind of thought that was a good idea and acceptable.
This is kind of what cross section of what the panel kind of looks like. You can kind of see it is a composite panel and then this is a clipping system then that goes on to a dense glass or some sort of sheeting then and so basically this whole dimension here is two and a quarter inches. The company was then able to, and it’s really hard to see in this angle, but put on a custom edge metal trim piece in order for us to have kind of that metal edge trim look. Each one of these pieces came pre-assembled and then slid onto site.
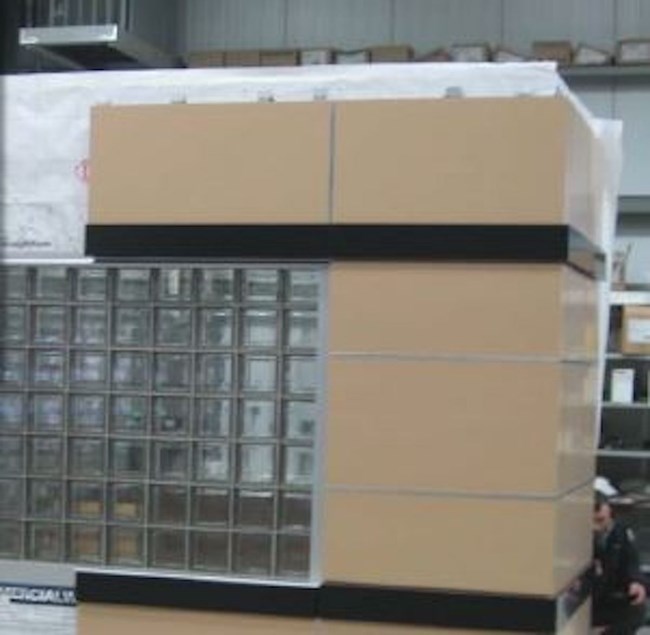
Quinn Evans Architects
Buy-In for Plans: Full Sized Mockups
In order to make sure we got everyone’s approvals and buy ins and we understood how the process was going to go, we did actually a full size mock up prior to actually fabricating all the panels so you can kind of start to see basically how the details were going to go. You can kind of see the building wrap and then next to your panel systems goes on top of that, colors are not original but we’ll match them identically, and then you can actually start to see kind of the new details.
As construction started we realized that the existing steel was actually in really good condition. We didn’t anticipate on using it because we anticipated it on being in poor condition but in the end we were able to keep that existing steel framing and actually frame up to that. What that actually did though, ironically, was it pushed our system forward a little bit more, so we ended up pushing it out a little bit further which adjusted the sight lines but again in the end you’re talking an inch and a half difference overall and from a street level you really don’t notice it.
So these are just some of the photos of the new panel systems being installed, some of the corner conditions again you can kind of start to see that metal edge trim as it wraps around, historic k-panel and how we deal with some of the flashings, stuff like that. The historic k-panels just for everyone’s information is, we kept those actually in place the entire time, that was too difficult for us to remove and put back in hopes that we would be able to save them. We actually kept those in place, we protected them with plywood and worked around those.
The next component was the glass blocks system. While we all new that glass block can be made today there’s a lot of changes that we wanted to have made in order for the building to function today. The glass block originally was a prismatic glass block so the idea back then was, it’s a department store, we want natural light to come in to highlight what we want people to focus- on the articles of goods, we don’t want people to look outside. The prismatic glass block did not allow people to view in and out, but secondly and more importantly today the prismatic glass block is not made. They’ve replaced it kind of with this new cross ribbed glass design. The option really was to kind of go back with this cross rib glass design or in our opinion we wanted to go back with a clear glass block. Being used as a department store have a prismatic and not views was important being adaptively reused into an office space being able to visually see inside and outside and have an idea of what was going on, whether was really critical to us and to the owner. So we were trying to get the change from a prismatic glass block to this clear glass block.
In order to do so they want you to show them that it’s not going to change, so we did full size mock up again on the building and trying to illustrate the visual impacts from both the interior and the exterior, what people would see between the clear and the cross ribbed glass block. So the top image you can see on this side here is the clear glass block followed with an existing panel in between followed by the crossed rib glass block. From the interior down here you can clearly see there’s a difference between the two. On the clear side you can see these hints of building shapes and sizes and forms from the exterior and thankfully it was a sunny day in Michigan that day, but you can see sky light, you can see that it’s blue.
From the cross rib side you really had no clue what it was outside, it could have been cloudy, raining, snowing, and you really had no idea, no connection to the exterior by using the cross ribbed version. However from the exterior it looked exactly the same and I’ll point out here a little bit, you can kind of see a light fixture hanging here in the clear glass block and you can see that same light fixture hanging over here in the cross. From the exterior you really didn’t get the difference as much. Now you do have a difference between the existing prismatic and the clear and we ended up working with the state to make sure that things were, just for reference the whole ceiling was being removed as well so you weren’t going to see this light fixture in the end, we were moving the ceiling up.

Quinn Evans Architects
Modifications & Final Installation
From the exterior you wouldn’t be able to really see anything that was kind of going on from the interior so in the end we were able to get the clear glass block. The other thing I want to point out because it’s going to lead into the next thing is the whiteness around the new glass block versus the existing glass block. You can see that even though 75 years later the mortar was probably extremely dirty. When you looked at a grey mortar that was used around this glass block compared to the grey mortar used around the existing it still looks very, very white. So that was another issue that came out of this mock up that we then had to begin to address. So we started digging into that.
Historic glass block was basically two pieces of glass fused together with a piece of lead. Right around the perimeter of the glass block would be then this lead joint that was heated up, the two pieces of glass were put together and that’s what created that glass block, historically.
Today they don’t use lead in construction, I’m not sure why but they don’t. What they do today is they actually use glass as the fusing piece between the two separate pieces so you really don’t have this dark trim around the perimeter like you did with the historic so when you saw it from the exterior the glass block, visually, actually looks a little bit bigger than the historic because of that non lead being there.
The other thing that they do is for adhesion of the mortar is they actually paint a white trim around the entire perimeter and that then allows basically the light to reflect once it’s inside that glass block, again making it look lighter and wider and then actually makes the mortar look whiter.
One day after work I was told I had to go to Home Depot and I bought six cans of spray paint, all different ranges of gray and the next day at the office all we ended up doing was painting perimeters of the glass block to try and get kind of a dark trim around the outside. This was kind of a mock up that we had done and you can kind of start to see here around this very edge how this is kind of a darker, darker grey. It’s not quite a solid color, but it’s a bit darker than if it was white. Really what that is, is the light reflecting off of this grey painted glass block perimeter that kind of mimic that edge of what the lead joint was at one point and time.
You can look at this mock up here and you can see that the grey mortar which was the same color we used actually out on the mock up really now starts to come off as a grey mortar just by doing a couple of those little tweaks. Ironically enough, and I’ve never seen this done before, but we actually had the glass blocks, since we had so much glass block, fabricated in panels off site and then shipped to the site then like this and then they were actually laid in the joints kind of in these panels, which actually I thought was kind of interesting.
And this is kind of what it looks like from the exterior so again you really can start to see the grayness around the perimeter versus the white that we had on the other sides.
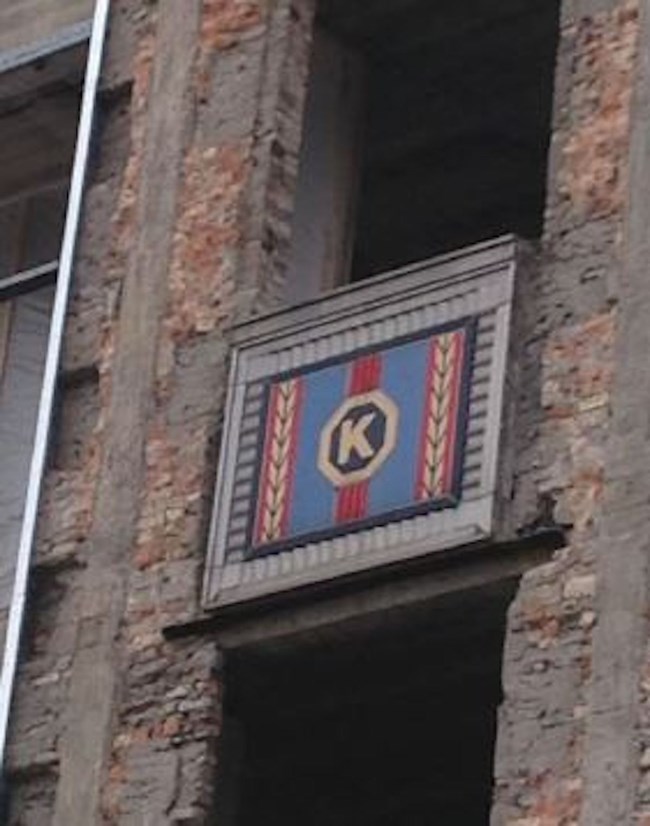
Quinn Evans Architects
Quickly and then I’m going to try and go through a little bit of the historic panels as I said on each of the pylons, there were the historic panels, k-panels as they’re referred to for the Knapp center, and so we kept those in place because we didn’t really want to get into trying to take those off and put those back. The store front similar to the Mako building that we saw earlier today had the large store front glass system. It was an un insulated single pane glass that if I pushed on it the whole system would move in and out five inches. We ended up coming back and strengthening that on the back side of it so you didn’t see from the exterior but keeping the same pane size but we were also able to go to an insulated glass too. Which would help from a standpoint of a comfort level right up against the windows.
So here’s kind of a photo of the k-panel kind of in place during the deconstruction of the rest of it. Then on the corner of the building was the Knapp sign edge and those panels were actually removed, sent down to Tennessee, restored, re fabricated, one piece was re fabricated as it was damaged and then actually sent back in and re installed.
This next round of photographs is about ten of them it’s just kind of a sequence from beginning to end. So this is what the building looked like when we took a hold of it, and then as you kind of start to see now the panels are being taken off from the left to the right. The steel is being exposed, more panels are coming off, and now you start to see that we’re starting to put on the steel framing, the metal framing with the dense glass, wrapping it, and then of course then we’re putting on the thi-vex. We now have the thermal moisture barrier going around it. Now it’s spring as we’ve got leaves on the trees and now the metal panels are starting to get installed. There’s actually a plastic film that they kept on the metal panels just to protect it from the sun as long as they could just to protect them- I guess more from construction. Then we started kind of finishing it and there’s kind of the final, the final image.
So here are some final images of kind of what it looks like and so in the end basically it’s a brand new exterior skin, from metal panels, insulation, glass block, everything is brand new but in the end it almost looks identical.
The interesting thing about Lansing is every time we were there, you know I had my hard hat on and I remember coming into this store and I remember seeing Santa, and I remember shopping with my Grandmother and there is a lot of nostalgia with this building. Without being able to really redo the entire exterior skin, this building would’ve met the demolition crew I’m imagining.
Then just a couple interior- I didn’t get into the interior that’s another whole half hour portion of the presentation, but in order to help make it a class A office space because it was really only faced with windows on two side, very little natural light actually go deep into the building. The photograph on the left is a 40 foot by 60 foot atrium space that we cut into the middle of the building for the office floors in order to bring natural light in, so every office tenant will have access to natural light in some way or form. The images on the right, like I said the interior was pretty much gutted in the 1980s for the state, but a few of the decorative elements especially around the stairs, the railings, the aluminum railings with the gold cap was still in existence so we were obviously able to restore those stairs and kind of create a new exciting, exciting entrance.
That wraps up the Knapp center redevelopment project.
Abstract
Built in the 1930’s art moderne style, the redevelopment of an original downtown department store, the Knapp’s Centre renovation included a complete reinvention of the exterior envelope to match the original 1930’s design. Experimental materials and techniques of the art moderne style have caused some buildings to become obsolete or viewed “beyond repair.” This innovative solution saved an historic building creating a new exterior envelope to meet modern day design criteria while maintaining the historic qualities of the 1930’s art moderne movement.
The Knapp’s Centre is a historic six story Art Moderne building in Lansing Michigan. The building was designed by Orlie Munson of the Bowd-Munson Company. The art moderne elements on the exterior included a metal panel system with strong horizontal banding and ribbon glass block windows. The metal panel system was constructed of several sections of pre-formed concrete, faced with a metal enamel panel. This innovative system was called a “Maul Macotta” panel which was a copyrighted product of the Maul Macotta Company. The horizontal banding of windows was comprised of prismatic glass block. The horizontality of the glass block windows with the Macotta panels are then interrupted by vertical blue macotta pylons, that mark the four building entrances.
The building was designed to house the main department store of the Lansing based JW Knapp Company. The building received great praise when opened for it moderne style, and today is considered one of the finest intact examples of Art Moderne commercial buildings in the Midwest. The building eventually closed as a department store and opened later as a converted office building. The building has been vacant since 2003.
Incorporating historic tax credits and meeting the Secretary of Interior Standards for Historic Preservation, the building was redeveloped and opened in 2014 as mixed-use, incorporating ground floor retail, three floors of office and top two floors as residential. The major challenges to the redevelopment included restoration of the exterior envelope including the historic Mocatta panels and the prismatic glass block.
Thorough understanding of the building envelope became critical to the viability of the project. Through dissecting the historic construction, an understanding of how the panels were constructed and installed along with the modifications over the coming years, led to a conclusion as to why the panels were failing. That understanding informed the design of a replacement system that was able to replicate the exact art moderne characteristics of the Mocatta panel.
The historic prismatic glass block was used for four levels of ribbon windows along the two main elevations. This style of glass block projected light into the showrooms while limiting views out. Similar to the metal panels, matching the appearance from the exterior was critical. Due to the differences in the historic and modern construction techniques of the glass block, special provisions need to be made to the replacement glass block to mimic the historic construction techniques.
Overall, the redevelopment is a huge success story in preserving the historic qualities of the 1930’s Art Moderne style, while modernizing the building to meet the necessary requirements of the twenty-first century.
Speaker Biography
Bradley Cambridge, AIA, LEED AP, is an architect and planner with the Detroit office of Quinn Evans Architects. He has over 15 years experience restoring historic structures including public landmarks, small community landmarks, and modest buildings within local historic districts. His interest focuses on urban rehabilitation and renovation projects across Michigan, strengthening our urban cities. Brad earned his Bachelor of Architecture and a minor in Urban and Regional Analysis from Miami University and a Masters of Architecture from the University of Michigan.
This presentation is part of the Mid-Century Modern Structures: Materials and Preservation Symposium, April 14-16, 2015, St. Louis, Missouri. Visit the National Center for Preservation Technology and Training to learn more about topics in preservation technology.
Tags
- gateway arch national park
- ncptt
- mid-century modern
- mid-century modern structures
- mid-century modern structures: materials and preservation symposium
- conservation
- st. louis
- bradley cambridge
- conservation
- detroit office of quinn evans architects
- the knapp's centre
- the knapp's centre: 1930's art moderne icon reinvented