Last updated: April 7, 2025
Article
Restoration and Replication of Steel Elements at Frank Lloyd Wright’s Fallingwater and Solomon R. Guggenheim Museum

WASA/Studio A
Introduction
Pamela Jerome: Good afternoon and I want to thank the organizers for having invited me here today.
And what I want to talk to about today eludes a little bit what Gunny was talking about this morning in terms of authenticity.
Gunny being a great proponent of authenticity of materials which of course is incredibly important.
But we are going to look at two very different Frank Lloyd Wright case studies: Falling Water and the Guggenheim, both of which I had the great good fortune or maybe the great headache of actually working on.
In fact, Bob Silman was involved with both projects as was Norman Weiss, so I should just mentioned that.
Fallingwater of course is the iconic weekend home of the Kaufmann family who were Pittsburgh department store magnates.
This was their weekend home in south east of Pittsburgh, about sixty miles southeast.
It’s a schlep to get there, is in the middle of nowhere in Highland Morals, in the mountains.
And of course, it’s a famous building, well known, incredibly iconic. This was the building of really kind of put Frank Lloyd Wright back on the map as a modernist architect which he had not really previously been thought about as even though when you get at the Robie House it’s very clear that in 1904, he was miles ahead of everybody else.
Early Residential Use of Concrete
It’s a concrete structure but today what I’m going to talk about are the metal materials that were conserved as part of this project and some replicated.
Obviously, one of the famous images is this with its standing over the waterfall and of course the steel windows and doors which Frank Lloyd Wright himself said it’s the first time they came within residential use- that they could actually use them residentially.
And it’s famous for not having corner mullions. And some of it just dives right into, I think you can probably see the arrow? Right into the stone walls.
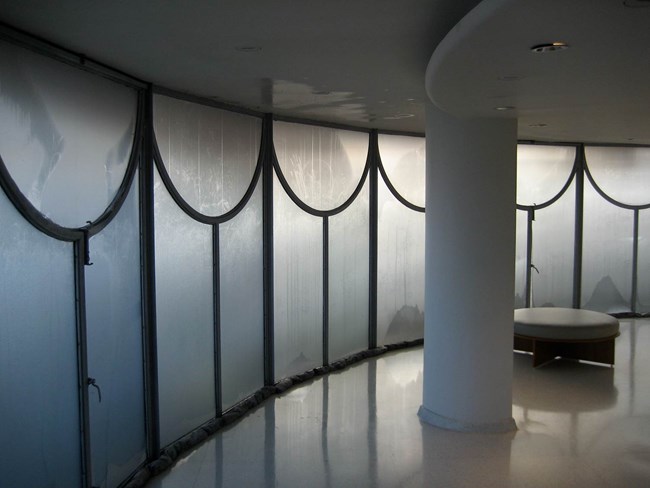
WASA/Studio A
So these were relatively problematic. You can see at the doors and not so necessarily the operable windows, in this case there is one. There are actual drip edges, but the drip edges were totally ineffective. Other areas, he used steel included the supports for to step canopy that goes up to the guesthouse.
But, the real issue was that you’re in a totally, really moist environment. I mean, it’s a marine environment, it may not be seawater but it’s water all over the place. The way the building is designed with the edges of the slabs being semicircular, it leads the water right back into the head off the windows and doors and drips through anything.
This was kind of the condition we found the house in when we started working there in 1989 and we spent about five or six years being like the Dutchman, putting the finger in the dike trying to stop leaks, testing out prototype patching and materials to fix the building.
We also tested out ways to repair the steel and eventually we wound up doing a preservation master plan and a condition assessment and then we went on to do four years of interventions that restored the building. We are looking at the stairs of the stream, very iconic element. And here we have mild steel which penetrates each tread twice, each strap penetrates the tread twice and this was like the impossible situation so we tried trial applied patches, we tried poured in place patches.
They all failed. And we definitely cleaned the metal to bright metal prior to doing any of the patching, but it failed. It’s just, the situation was that the staircase gets partially submerged every time there is a flood and it’s pretty frequent actually there. This was not going to work.
Windows & Condensation
On the other hand, we had steel windows, steel doors, some steel elements. Very poor condition and Fallingwater. But, we had a house museum which left the windows and doors open half the year. Whenever there was good weather, the house has been mandated, part of it presentation and interpretation to show how the people lived there.
Kaufmanns lived there, they lived there with the windows open. They didn’t close the doors and windows when it was nice weather. So, that is the way it’s treated even though there is some significant artwork from their collection in that house, including Picasso and two Diego Riveras. It’s not treated as a museum environment. The exact opposite is the case with the Guggenheim. The Guggenheim has a constant level of humidity interior environment of fifty to sixty percent.
How do you deal with that when you have single glazed steel windows and doors again?
And these were in incredibly good condition but I think you can see from this photograph, unbelievable condensation.
Unreal amounts of condensation. Water ponding on the ceiling, water ponding on the floor. No visibility whatsoever of Central Park. Remember that Frank Lloyd Wright, well known for his organic architecture, inside, outside, all one environment, bring the outside inside, where do you see the outside here?
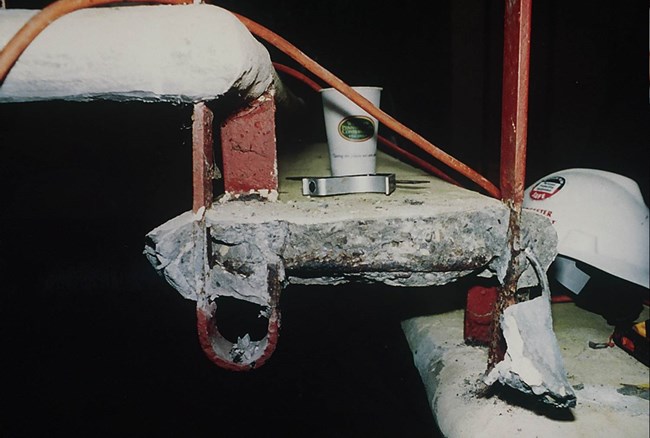
WASA/Studio A
World Heritage & Development of Standards
In fact these rooms were rendered, this is what they call now the townhouse of Pavilion which once was known as the Monitor, rendered completely unusable during the winter and part of the time during the summer. Totally unusable. Had to be blocked up. I swear to God, that reflection on the ceiling is water. Here we had perfectly good steel windows, I mean, they were in perfect condition.
But, a totally unusable situation. So let’s talk just for a minute, theory. And we heard Gunny mention the key works of modern architecture by Frank Lloyd Wright. Ten iconic sites that is going to go forward and presented at the world heritage committee this summer in Germany, in July I believe the world heritage meeting is.
And it’s the nomination from the US and what we need to think about is how our treatments, which I’m going to talk about in a second, impact outstanding universal value, which is how you get on the world heritage list. What does OUV mean? It means cultural and/or natural significance, which is so exceptional as to transcend national boundaries and to be of common importance for present and future generations of all humanity.
This is the world heritage convention, it became of convention in 1972. It did not have operational guidelines until 1977. The first things that were put on the world heritage list were not actually designated until 1977. There are ten criteria for designation. Six of them relate to cultural sites, four of them relate to natural sites and of course you can have a combination of both in the case of cultural landscapes. The nomination for Frank Lloyd Wright uses criteria one and two.
So we have criterion one, this is to prove you have outstanding universal value. Criterion one, it represents a masterpiece of human creative genius. And in the nomination they talk about the symbolic forms expressing function as justification for criterion one and dynamic space and form and also, organic expression.
This second criterion that this is being nominated under is, exhibit of important interchange of human values, over a span of time or within a cultural area of the world on developments in architecture or technology, monumental arts, town planning or landscape design. And here the justification this adaptation to modern requirements and organic influence.
You also, in order to get on the world heritage list, you also have to pass the test of authenticity which in 1977 was described as meeting the test of authenticity in design, materials, and workmanship, and setting. This comes straight out of the Venice Charters monumental Eurocentric approach to cultural heritage.
So, 1964, 1977. By 1994, and again Gunny alluded to this with the Japanese Temple, there was something called the Nara document on authenticity because there was so much concern from member states or state parties as they are known, members of the convention about not meeting the test of authenticity when it came to wooden architecture.
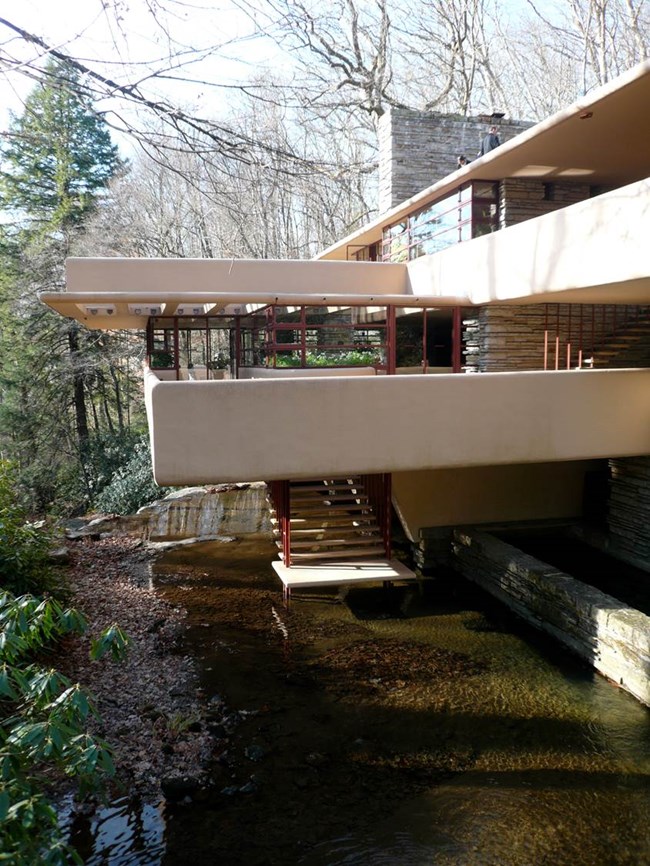
WASA/Studio A
Documentation, Standards, and Materials
For a ephemeral materials this doesn’t work. The materials, the design, workmanship, and setting. Instead, the new passing the test of authenticity as a result of the Nara document which are now part of the appendices of the world heritage operational guidelines is form and design, materials and substance, use and function, traditions, techniques and management systems, location and setting, language, and other forms of intangible heritage, spirit and feeling, and internal and external factors. There is also the test of integrity. Which means that the property must contain all of the elements necessary to express its outstanding universal value.
I am going to ask you to remember this and the fact that the definitions of authenticity have changed and evolved. And then the criteria which were selected to designate the key works of Frank Lloyd Wright of which Falling water and Guggenheim are two of the ten and then think about how we intervene, of course long before we knew that these buildings could potentially end up on the world heritage list.
Let’s go back to Falling water. As I said, the mandate of the Western Pennsylvania Conservancy who owns the building since the early sixties is to show the building as it was lived in. Despite the deplorable condition of the steel windows and doors including this hatch to the stream which was so corroded that it was actually immovable for decades, until we had restored.
There was no question in our mind that this building, which is totally a Frank Lloyd Wright building and the only changes that were made to the building were made by Frank Lloyd Wright himself, within three or four years off the construction of the main house, the guesthouse was constructed. Basically, with the exception of the carports, which were converted quite sensitively into a kind of lounge for visitors at the very end and they give you the spiel, donate money of your tour. Nothing has happened to alter the site. So we have pristine authenticity in a way of at least the architects concepts and a lot of the original materials are still in place.
We brought out from, I believe it’s, I can’t remember where this guy was based. Peekskill, now? This is a picture of him, you know, twenty years practically doing the hatch to the stream, which was the litmus test. Could he fix this thing and he fixed it so that you can push it with one finger. I mean, just incredible, it’s all on ball bearings.
And here is, looking much younger then he is today. He also fixed the corner windows and so we knew we had the right contractor. And in fact, about in 2002, he was hired and he did all of the windows and doors throughout the complex and since then they’ve been touched up in 2010. And I have to say that I go there every single year and bring my students and I am quite impressed with the paint, which is industrial paint, that it’s held up so well.
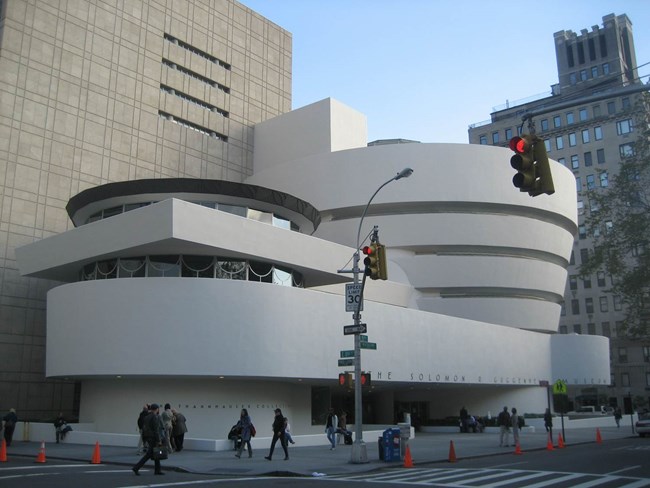
WASA/Studio A
Here is the restored, by the way, hatch to the stream. Now, with the stairs to the stream, we had the other issue. We have the issue of, how do you make steel not corrode when it gets submerged. Well, you can’t. It’s just an impossible fact. We were, with further research we figured out that the stairs to the stream were not an original feature. They had been knocked off by a storm carrying debris in the fifties. So, they were a reconstruction already. Then, we felt a little better about it. It was like “phew, it’s a reconstruction. We can do what we think we need to do.”
And in fact, Bob Zellman’s office designed this stainless steel straps that now support the stairs to the stream. Getting paint to stick to stainless steel as you well know is not an easy feat and we needed paint that was both submersible and non-submersible, and that was done. And again, hugely successful, it hasn’t spalled since. Low and behold. These have been completed over 10 years now, so I think we can safely say that they are going to remain and survive.
Now, with the Guggenheim, we had really good material, in excellent condition. But one that just was inadequate in terms of its performance for a world-class art museum. So, we had to face the fact. In fact, we tried all sorts of things. We went through all kinds of testing, we looked at beefing up, in other words, pushing out sort of the layered class, putting in double glazing.
But the long and short of it was that we had a non-thermally broken steel fright and there was nothing we could do to get around it. No matter what we tried and tested, we could not guarantee that it was going to work and in fact, we were pretty certain it was not going to work, and we were also dealing with the building that the interiors designated as well as the exterior.
And if you know anything about the New York landmarks commission, they are pretty tough when it comes to aesthetics of designated sights.
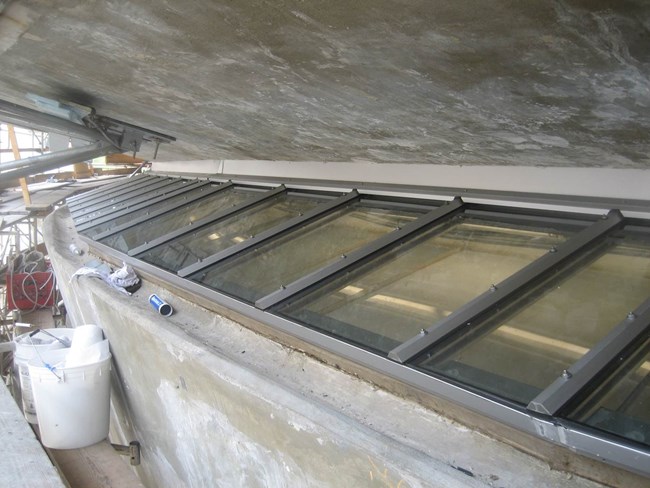
WASA/Studio A
Authenticity of Usage over Authenticity of Materials
They don’t mind if you replace it with aluminum as long as it looks identical. Well, we weren’t about to go there. Instead, what we ended up doing is, we went to several different manufacturers and we finally came up with a manufacturer out of Torrance California who custom made identical windows and doors and replicated them in steel. Because, the only way you were going to get that incredibly thin profile was with steel.
But, thermally broken steel. Here’s a case where the authenticity of usage took precedence over the authenticity of materials. It was very painful for us to make this decision but it was inevitable. If they were going to continue to use that space all times of the year and if this was to be a world-class art museum it could not have ponds of water sitting on ceilings and floors, it was just untenable. It just didn’t work.
And we ended up with the added positive effect that we’ve now reconnected the townhouse or Pavilion to the park across the way. We’ve reinforced the organic nature of Frank Lloyd Wrights philosophy which is part of the criteria for nominating into the world heritage list.
This view was just impossible nine months of the year and it just made no sense to live with the perfectly good material. Believe me, we’ve thought about everything, including putting on storm windows, everything you can imagine to save this original material. But, in the end the thing that made the most sense was to replicate it.
So, I am going to leave you with that idea, but also just to let you know that we had the same issue with the skylights. Now, the main rotunda skylight had already been replaced in 1992 with double glazed skylight.
But, around the perimeter of the building, on the rotunda, or unseen skylights that are below lay lights which is what you see on the interior. And those things condense like crazy because again, they were single glazed, thermally broken steel skylights.
We ended up replicating them in aluminum because they are completely invisible. But we used basically the same concept as he did and now we don’t have ponds of water on the lay lights or dripping in between in the interstitial spaces. And so, this is what it looks like. Yeah, I know, this little thingy here is supposedly a gutter.
I don’t know why Frank Lloyd Wright thought that rain was not so important, all of his buildings look notoriously leak, but that was his thing.
Abstract
Frank Lloyd Wright used steel windows and doors in innovative ways for his time. At Fallingwater, a weekend home designed for the Kaufmann family of Pittsburgh, he incorporated Hope’s steel casement and fixed windows to create a dramatic effect, often without corner mullions or dying directly into the stone walls with no frame. For the Solomon R. Guggenheim Museum, he employed Hope’s window-walls on the Thannhauser Pavilion.
WASA/Studio A served as preservation architect for both structures. In the case of Fallingwater (1936-39), cantilevered over a stream, the steel elements were found to be significantly corroded and had to be stripped to bare metal. Fixed windows in the main house had no drip edge at the head; this was corrected subsequently for the guest-house addition.
Both the heads and sills lack waterproofing, and deformation of the concrete roofs and terraces left enlarged gaps that promoted moisture penetration. This was further exacerbated by the curved profile of roof edges, which also do not include a drip. In several units, areas of deteriorated steel had to be cut out and new sections welded on.
The hatch over the stairs to the stream, an iconic element within the living room, was so severely corroded it had not worked in years. A specialty steel-window contractor, Seekircher Steel Window Repair of Scarsdale, NY, executed the work. In addition, when the stairs to the stream were reconstructed, the mild-steel straps from which they were hung had caused the ongoing deterioration of the cast-in-place concrete treads; these were replaced with stainless steel. WASA/Studio A specified the industrial-paint system for all exterior steel elements, which in the case of the stairs to the stream, had to also withstand partial submersion.
By contrast, at the Solomon R. Guggenheim Museum (1959), the original steel window-walls were in excellent condition. However, the high relative humidity in the museum’s interior environment, favorable to the artwork on display, resulted in extreme condensation at the single-glazed window-walls, rendering the Thannhauser Pavilion unusable during the winter months.
In this case, with the assistance of William B. Rose Associates, our building-envelope sub-consultant, we undertook a thorough investigation into the efficacy of retrofitting the existing frames, including evaluation of the aesthetic impact (the building is also a NYC-designated interior), as well performance. It was concluded that the window-walls could not be reliably upgraded, nor could the introduction of storm windows guarantee the resolution of the condensation issues. Therefore, we specified steel-framed replicas that were thermally-broken and double-glazed, unprecedented in the US at the time, which were custom-fabricated by Torrance Steel Window Co. out of Torrance, CA.
Although in both cases, Frank Lloyd Wright relied on single-glazed steel-frame windows and doors, our philosophical approach to Fallingwater was completely different from that of the Solomon R. Guggenheim Museum. Fallingwater is a house museum, and the house is interpreted and presented in the way the Kaufmanns lived in it.
As such, the windows and doors are open during the months of good weather. Despite the fact that there is important artwork from the Kaufmann’s personal collection displayed in the main house and guest house, these are intentionally not kept in a museum environment. This condition is reversed at the Solomon R. Guggenheim Museum, where authenticity of use – that of a world-class museum – had to take precedence over authenticity of fabric.
Speaker Biography
Pamela Jerome, AIA, FAPT, LEEDTM AP is partner in charge of preservation at WASA/Studio A, a New York City-based architecture and engineering firm. She is also an Adjunct Associate Professor at Columbia University’s Graduate School of Architecture, Planning and Preservation.
Ms. Jerome is extremely active in the International Committee on Monuments and Sites (ICOMOS) Scientific Council, where she is also an expert member of the International Scientific Committee on 20th Century Heritage (ISC20C). Her expertise is in masonry conservation, waterproofing and cultural-site management. She has consulted on cultural-heritage preservation in the US, Mediterranean, Black Sea, and Middle East.
This presentation is part of the Mid-Century Modern Structures: Materials and Preservation Symposium, April 14-16, 2015, St. Louis, Missouri. Visit the National Center for Preservation Technology and Training to learn more about topics in preservation technology.