Last updated: April 7, 2025
Article
Podcast 082: Talking Red Masonry and the Rebirth of Lime with Jimmy Price
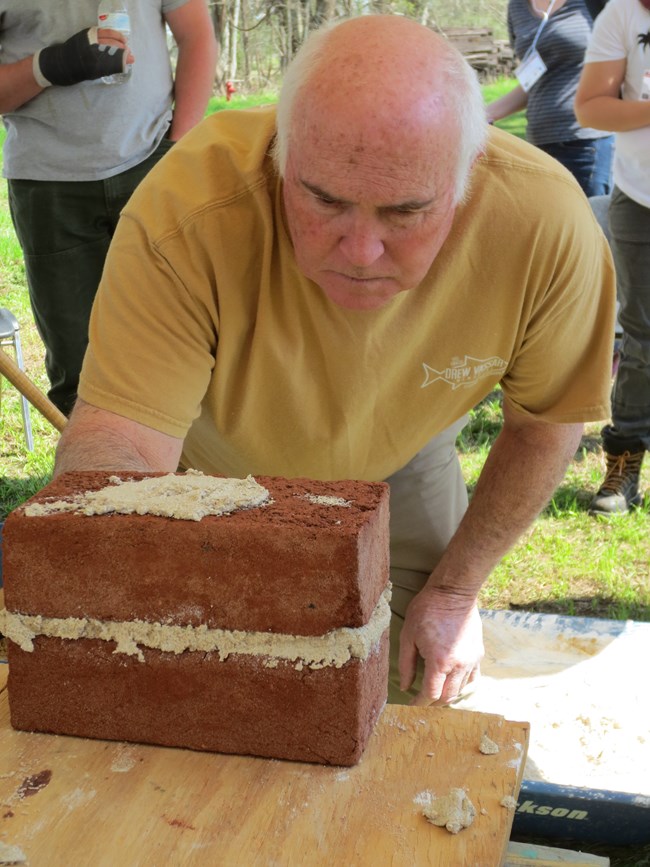
National Park Service
Lime
Jason Church: Today I’m here talking with Jimmy Price, former owner and founder of Virginia Lime Works, owner of Price Masonry Contractors and Jimmy, in the world of historic preservation, you’re really known as the guy who brought lime back. Tell us a little bit about that. What is your background in masonry and how did you get into lime?
Jimmy Price: I started in (19)72 and I started out laboring, pushing a wheelbarrow, worked at a foundry for a while but didn’t mind working because I always worked hard all my life but had a 19 year old wife at home and set working seven days a week, third shift.
Just didn’t seem natural to me and I grew up on a farm, my dad had a grocery store so I was used to being kind of independent working outside so I came back and took another job and ended up going to work for my uncles that were masonry contractors and I started an apprenticeship with them.
Funny thing about coming full circle in a way, the black guy who taught me how to make mortar, he was one of the biggest strongest guys that I ever worked with and his name was Quentin Parnell and he taught me how to make mortar and just good old soul that ever was.
He served with Patton during World War II so he had been all over to be a laborer but he was a really good man.
Later on, I’ll get back to him in a little bit but as we went on, after my apprenticeship, I went in business for myself and doing schools and shop and summers and things like that but always been a history buff and military history has always been a big thing that I’ve been interested in so finally I got to thinking, so I’m going to start doing what I wanted to do and some of the recession years of the early years, so I decided to downsize some and start picking up and getting into some historic work.
And one of the first major projects was Greenhill Plantation, which was a slave breeding plantation in Virginia and it ran about twelve hundred slaves on that plantation and 5,000 acres, but that was the crop was the slave trade there.
And we had a grant to do all this work for the state and that kind of got us started … We had some other smaller things, but then this was a major breakthrough.
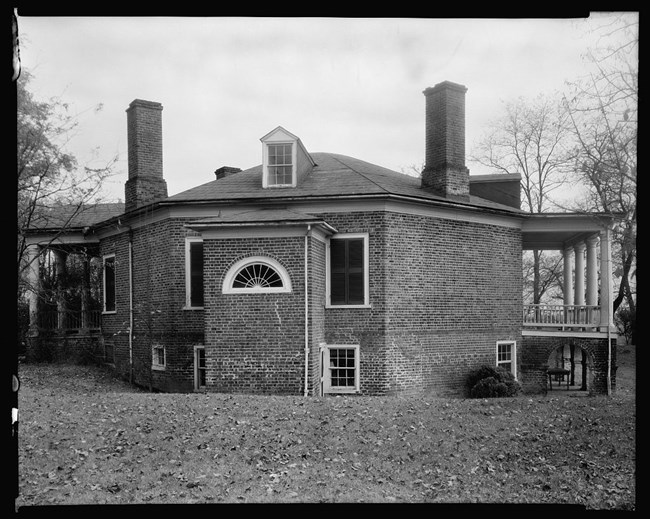
Carole J. Buckwalter.
Poplar Forest
So, as we got into it, found out that the owner in 1790, who in the heyday of this plantation, was John Pannell and it’s kind of funny that Quentin was from Gladys from this area so all the Pannells, right then.
That was the Pannell blood line and they were noted for their big males and that was Quentin, the nicest fellow you ever met, and that’s who taught me how to make mortar, ended up being back restoring their roots and where the whole family came from.
I always thought that was a pretty good twist to it. After that, we got into some other different things and then Thomas Jefferson’s home at Poplar Forest.
We got in there and ended up being in there for off and on 14 years with Travis McDonald there at Poplar Forest, but the more we got into it, it’s like … And I really enjoyed … It’s like how can specialize in historic masonry when the right mortars haven’t been made in 100 years and everything that’s been done or going on has failed.
That’s kind of what was driving force, like, okay, well, if we can do this, it’s got to be a good thing. I guess I’ve never been afraid of anything so I’ll give it a try and do it, so that’s what we did.
Through Poplar Forest, I worked with the architects, Mesick, Cohen, Wilson and Baker out of Albany, New York. They were fantastic because they believed in tradespeople and to learn from tradespeople and what they have to offer and what their insight is, what their opinion is and not just what the architects say.
I wouldn’t be here today if it wasn’t for those guys because they encouraged and wanted you to learn and grow and help them figure it out. And that’s exactly what we did.
Kiln
We found a stone source for Poplar Forest and built a wood fired lime kiln to start off with. I guess the bad thing was we were successful because we kept going. So, there’s lots of trial and error and failure and failure and you don’t do this and you don’t do that and after several years and tons of firewood of burning and burning and you learn all your mistakes and all of that and tweaking.
I built another bigger kiln and went from there. So, it’s kind of like bootlegging lime with what it was because how could you get a permit. How could you do it when you didn’t know if you was going to succeed or work. It was just burning a wood chimney, so I just did it. And that’s kind of how it went with.
By doing so, you just reinvented that wheel and then that started into the techniques. We were already working with lime at Poplar Forest and that’s what we ended up doing was producing all the lime mortar for the wing of offices at Poplar Forest and all the interior plaster work. We ended up doing all the brick work and then as it was coming along and we was finishing up the brick work, out of necessity and we already had a good crew at Poplar Forest, and in following at Chisholm Irish Masons who did the brick work at Poplar Forest.
When he finished up, the plaster didn’t show up and Chisholm ended up plastering that at Poplar Forest. We had to try our skills and pretty close, but it was a lot we needed to learn too.
My travels in Scotland in England that I met Alex Hollins, a Scottish plasterer over there and he ended up becoming my mentor and got him involved coming over with us to cross train us and work with us at different phases at Poplar Forest, like first coat and second coat and finish coat. He was more of a gypsum plasterer, but did some historic stuff. He had done Sterling Castle there in Scotland. One of the bigger restorations for historic Scotland.
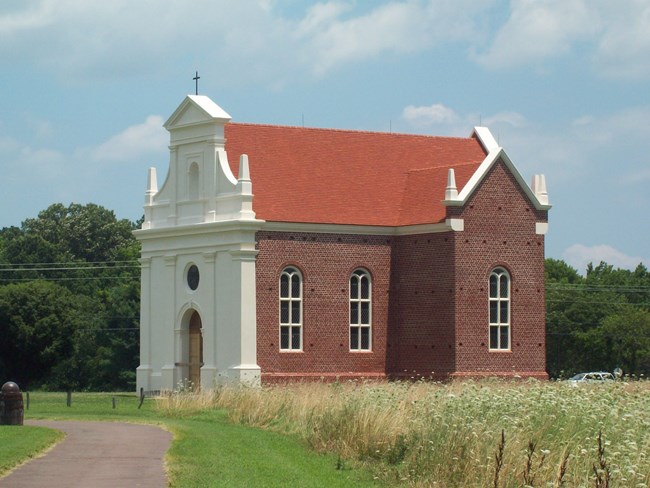
Pubdog, Wikipedia
We became close friends and worked together a lot over the years and kept growing from there and learned a tremendous amount from him. It’s like reaching back into antiquity and pulling a lot of this forward and what have you. It was a great experience there. Then you end up having two really good crews of top line plasterers.
Today all these skills have been lost.
Montpelier
After Poplar Forest and the main part and the plaster work was done there, just as Chisholm ended up leaving there and going to President Madison’s home at Montpelier.
Funny thing was, the same architects that were doing Poplar Forest was doing Montpelier and here we followed Chisholm’s footsteps again from Poplar Forest to Montpelier and we did, I guess it ended up being $25 million dollar restoration in Montpelier and supplied, I think it was 240 tons of lime plasters and mortars to do the work at Montpelier.
One of the unique things about Montpelier and the learning curve and moving forward at the same time and understanding of all these historic mortars, that archeology has letter of ownership where Madison owned a particular quarry in Gordonsville and it matched up to a period of time of construction and then it was sold, but then he bought it back.
And it was during another period of construction that Mont P was all brick. It was no stone so why would you need a quarry. So, a good choice would be he’s using this to make the lime mortars for Montpelier.
So, we took mortar and plaster samples from those eras of construction and from this quarry site and sent them to a material scientist in Scotland, Bill Reavy, and he did an XRD and Petrographic analysis and what have you and came back it was the forensic side and that was the exact stone that we used and was a dolomitic argillaceous limestone that was moderately hydraulic.
So, by having this information and the skills that we had developed over the time, we knew on cooking that stone and we actually got the stone that was a real odd slatey stone, I probably wouldn’t have thought it was a limestone if I saw it.
It ended up that’s what it was and it was kind of slatey so you had to split it just like slate and when you loaded the kiln, it was like loading a dishwasher almost. You couldn’t just throw it into a pile.
You had to … Just like loading a dishwasher with plates and then the opposite way because you have to maintain the airflow through a kiln and that’s how we burned the limestone for Montpelier and took the same sands and clay content from the boarding house to replicate that mix.
It wasn’t a replica mix.
It was the like for like mortar that Madison did use.
Well, you don’t get to do that every day, so it makes it interesting there.
And then another one at the same time we had going on was the Chapel at St. Mary’s, Maryland. That was the first English speaking Jesuit chapel in the colonies at the time.
Fourth colony there be in Maryland. We were very unique to work with the same architects. Just kind of having that team put together and following along, plus, like I said, I enjoy the history side of it, like the present and we actually did the Jesuit chapel, which had been lost for 300 years.
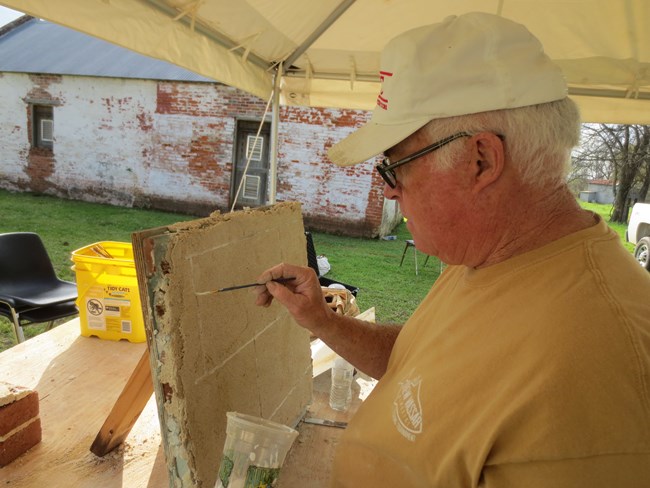
National Park Service
Virginia Lime Works
Jason Church: So, how did you go from doing your own work and burning your own lime, to starting Virginia Lime Works?
Jimmy Price: Well, just by demand because nobody had it and we were the first in the United States actually to do it. In the preservation community, when you hear something going on at Poplar Forest because that’s when we got connected with the National Park Service because Tom McGrath and Chris Robinson brought because of some of the stuff that they’d heard and what we were doing a Poplar Forest brought two van loads of the HPTC staff down and when they saw …
We were pretty advanced at that time with what we were doing and basically the only thing survived at Poplar Forest was Jefferson’s brick work.
So, we were living archeology is what we were doing to save Jefferson’s brick work, so there was a little bit more to it than just laying a brick and chunks of mortar in a hole. That sort of thing.
We did a lot of reconstructive surgery with brick patch making our own brick dust from brick from Poplar Forest and reconstituting and dental work as you would call it and different things and crack repairs and basically growing brick and that sort of thing to go back and do the restoration work.
So, when Tom and Chris came down with the crews and they saw that, they wouldn’t make me feel good, kind of put them and said whoa, we have a lot to learn to catch up. In the meantime, started collaborations, so I end up working backs and forth with the guys down in Frederick for years and still collaborating so I’m here today so it’s been great and a lot of fun. A lot of good friends and that sort of thing, comradery and the whole thing, so it’s like a family reunion seeing everybody again.
That’s kind of where that started at and once that information starts circling out and it’s the same need, everything that everybody was doing was failing with cement mortars and hybrid blends of kind of like the park service mix with that little bit of cement. Just enough to cause it to retain moisture and still failed, but it was sympathetic, you were trying to make it work and that’s what drove it further.
Fortunate to spend a lot of time in Scotland and collaborating on plasters and lime washes and things like that over there because we had the mortars and we were way underway for mortars and the learning curve and then we found out more about natural hydraulic limes in France that just were coming into the UK a little bit then, so next thing we started bringing the hydraulic lines in to the United States and took a chance, I said, okay, we’ll see what we can do.
Nobody has it, so we just kind of were the leader and bringing it in and making it work and then we’re still working with the training and stuff like that too to help them out because we wanted everybody to be successful because it’s a pretty big learning curve because of geographic location and what somebody’s doing in Charleston you’re not going to be doing it in Boston or Michigan and that sort of thing.
It’s kind of trying to keep everybody safe as you can to make sure they’re successful with their projects and things so, that’s kind of developed that part of it and I figured, well, I have my whole family involved. My daughters were in the office. One of the daughter’s is doing the color matching. My son-in-law was running the plant part making all the stuff and then my son is doing all the technical stuff. He is a computer whiz. So, everybody had a very distinct role in the company. It wasn’t just using your kids.
Well, they were used, but everybody had a special talent that I couldn’t have done it without them. Just with those specific talents, because I can build I’m a good builder. But I’m not the best mechanic in keeping a machine that I don’t know anything about and keeping it running and that’s what my son-in-law, they can keep the mixes running the baggers and the airpackers and all the electrical and I say, no way. I’d be lost as could be and the same thing with the computer stuff. I’m still computer illiterate right now.
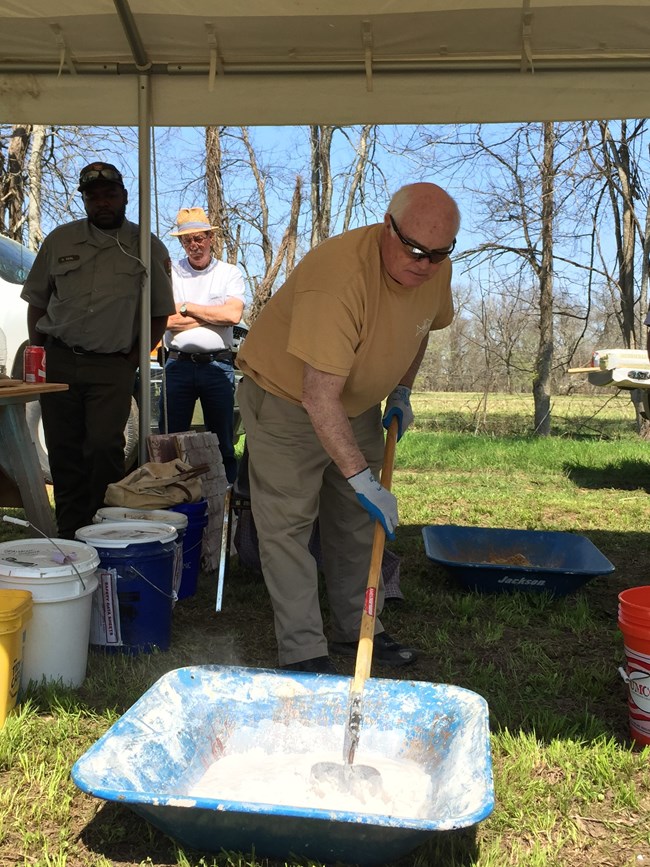
National Park Service
Training
If I go give a talk and the button doesn’t come on, I’m in a panic. I’ve had that happen plenty of times just like the other night here. You’re always relying on somebody else.
That’s kind of the evolution of it there. After that part, then after being on Quinque like Chris Robison was over there at the same time. We actually shared apartments a couple times during the training and the Quinque experience. I was over there for 10 weeks and on that stint and getting to do different things I like to do, but when you’re submersed in that culture and seeing from medieval buildings to Georgian buildings to everything in between and it’s just stone, lime mortar, lime plaster, lime paint and these buildings are performing fantastic right now, that’s what pushed me.
I said, we’ve got to do something better because all the buildings are making everybody sick right now. Just like historical buildings that if you’re not repaired properly, mold and damp issues and unhealthy building syndrome, that sort of thing is so bad and modern buildings doing the same thing.
If you’ve got the best brick, the best block, the hardest cement and flashings and everything that you can do, how come these buildings are so sick and you can’t get the dampness out of the walls and out of the building. It’s kind of blending the technologies of old and new from what worked historically, but doing it in an easier way and that’s when I ended up developing environment building system that we came up with.
Right when we came with that, so, we had that going with a lot of testing and things like that and right when we had the big opening house in August 2007, so we had the cottage that we had built and brand new building and try to set it on fire. I had diesel fuel and gasoline on a couple sides and lit it up and had the fire department there and a big media event and tried to burn it down and that didn’t work. Just soot up my lime plaster up a little bit. It didn’t hurt a thing, so we blocked the doors up with plywood and caulking and rubber and pumped 32,000 gallons into a brand new building and we all jumped in and went swimming and had a big time.
Today, no mold, no mildew and no paint peeling and you kind of wonder what is going on that we can’t grasp this technology, but it’s the difference of myself living in two worlds of seeing the old ways and how they work and the new ways at the same time and trying to make it work and the timing. I said, “Lord’s willing and he’ll come back around when he’s ready.”
Have the building system like that. Then like next month Lehman Brothers collapsed and everybody slammed the brakes on with, to me, the best building system that ever came up with and it can only be improved upon from this point moving forward. Yes, it’s been quite a ride I guess you could say.
Jason Church: So, what’s next?
Jimmy Price: I have no clue. Every day’s an adventure. Like I say, we’ve had a rough few years here when it takes $10 and you only get $6 and you just keep on. I’ve been in construction and ups and downs for 46 years, I guess, now and it’s been challenging and I get it. It’s just what it is and especially if you’re in the private sector.
You’re on your own. If something don’t work, you don’t get paid and you do without and then you recover and go again. That’s kind of where we at, but everybody used to say, with everything we did, and so proud of the family of what we did and all that. I laugh, but I don’t know that I’ll put a family through that.
It’s life and it’s what it is, but the knowledge and information is still there. Things can still be done. I’m just kind of waiting for the next step to see how things unfold and develop. Still training. This is kind of the first one for a while. I did do a historic church back in the Fall. Kind of neat. And really first class brick work and I think that some of Jefferson’s masons from Charlottesville and UVA. I was on my toes when I said that I had that much respect. These guys were good and I had to really … Took me a little while to get their style down, but most of the time if you’ve done enough of it, it takes a little bit to see with their eyes and pick up their style as we did. That was a fun job to do that last Fall there.
I’ve just been working on some of my own work. I get pulled in some different consultancy things from time to time. Thinking about getting back into, you know, because there’s such a need. So many people ask and I step back into it a little bit and set up at the office to do some, maybe, week long training sessions once a month or something like that and see what happens there.
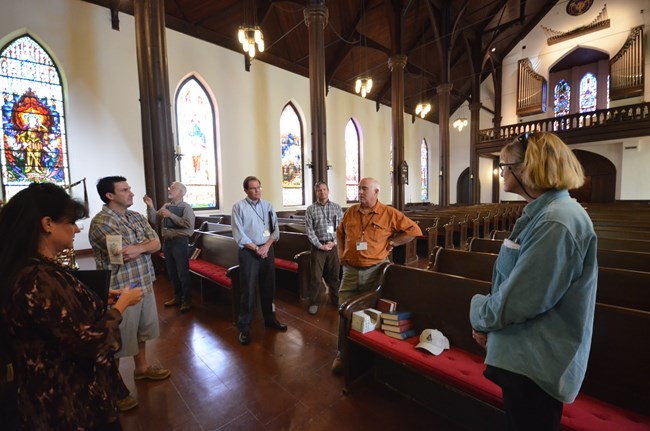
National Park Service
Jason Church: We’ll keep our eye out for new Jimmy Price trainings.
Jimmy Price: We’ll do that and the lime paint that we had. I really loved that out of all the different paints. You can do a simple lime wash that is pretty straight forward, but the lime paint, I just love that to death. And with the girls and all, I think I got a couple of grandkids getting ready to go to college, so they’re kind of thinking, I could use the extra income. Let’s get the paint back out there again, so there’s another little step, so you might see something there. We’re just taking baby steps to … Like say after having a rough few years and kind of see where it goes from here.
Jason Church: Any projects that you remember fondly?
Jimmy Price: We had a lot of neat ones, but once in a lifetime … You kind of say that and then all of a sudden you get pulled into something else, but St. Mary’s was a very unique project. I’m a history buff anyway and to get to apply history in a modern situation and, like I say, with the scaffolding that we did, we had people come and just to see the scaffolding and really not the church sometimes because it was over the top. It was a hoot and the people of St. Mary’s that I worked with you couldn’t have had any better. Dr. Henry Miller and Roger Hill that we worked with up there. They were fantastic, so it was good to be a part of living archeology, which is what it was. And that’s what we got to do. And then when you’re doing it, okay, it’s one more thing that nobody else has experienced and it just opens you up that much more and understanding. It’s a little harder at first and then, hey, there’s nothing to this. I can build that scaffolding just as fast as you can do conventional scaffolding, pretty much. Once you get into the groove and get your initial setup.
So, it’s things like that, that … And to do the brick carving and things that we did like that and is very unique at the same time and you had control of the job site and not waiting on shapes from the brick companies. We had so many different shapes and things I think it would have drove the architects completely crazy to do all the shop drawings and then if you ever got them approved and got them done, you would have never got to do them, by the time it would have taken years and it was easier for them because they had Montpelier going on and they just had your basic drawing. I knew I had my pieces worked and cuts and everything like that, so all I needed was a profile. They gave me a profile and I went from there and we’d do the carving and stuff during the winter months when we’re not on site. We were working a traditional season again, so it kind of started in April and finishing up in September and that sort of thing.
It was a very unique one, but Poplar Forest was very unique too, to get started and do that whole thing there, too. It’s been a very interesting thing because when you find out and you go somewhere and you’re looking at something and you’re up in the attic in one of these historic buildings or down in the basement and nobody sees the stuff and you get to check out and you learn from it and see and then you go to the UK to be on top of Hampton Court Palace with all these hundreds of hand carved chimneys and things like that on top of Stirling Castle, Canterbury Cathedral and Fonte De Gaume.
I’m glad you said that because one of the neatest things I’ve ever saw when we were bringing over materials from France, we got to go to Fonte De Gaume and see the 40,000 year old cave paintings. That was cool. You go inside and see these bison and then all the animals that there holding a torch in there and chiseling around the outline of these bison with a little stone tool. Like a stone chisel, then painting, and using the stone features for the shape of the stones to form and define the legs and bellies and things like that. And then they can walk right outside and get eaten by a Saber Tooth Tiger. I thought that was really cool. It’s been pretty cool to be in some of these places and things have been quite the adventure I guess. I don’t think it’s quite over with yet.
Jason Church: Definitely not.
Jimmy Price: It’s been pretty cool. And then on top of Rosslyn Chapel that nobody would be in the top of Rosslyn Chapel on top of the roof and all, up in the scaffolding doing restoration there. Yeah, its been quite a hoot.
Jason Church: Our listeners will have to stay tuned to your next adventures.
Jimmy Price: Well, we’ll see what happens. Hope so.
Read other Preservation Technology Podcast articles or learn more about the National Center for Preservation Technology and Training.