Last updated: April 7, 2025
Article
Podcast 060: Laser Cleaning and Laser Scanning with Martin Cooper
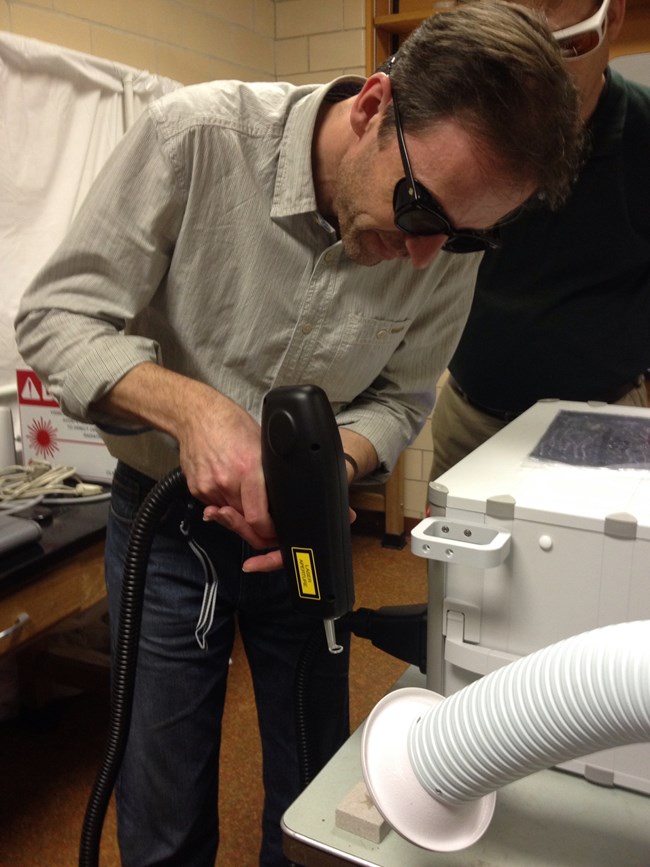
National Park Service
Lasers in Conservation
Jason Church: Dr. Cooper, we know you mostly through lasers, that’s how I was introduced to you. How did you get into lasers and conservation?
Dr. Martin Cooper: Pretty much by mistake. I studied physics at University in Loughborough in England, applied for a few jobs, and didn’t get offered anything, and was toying with the idea of doing some research, PhD, and I just happened to see one day in the department there was an advert for a PhD looking into developing lasers for cleaning sculpture, in particular, bits of medieval cathedral from Lincoln. I thought that sounded interesting so we had a chat to the supervisor, who I knew, and I thought, “Yeah, I have a go and see what happens.”
Jason Church: How long did you stick with that?
Dr. Martin Cooper: I spent three years at Loughborough working with Dr. David Emmony in the Physics Department there, did my PhD. Basically we were looking at different types of lasers for removing in particular hard black pollution crustaceans from limestone, medieval limestone carvings.
Dr. Martin Cooper: I spent three years studying that. We ended up developing a prototype laser cleaning system that we tried out on a few bits of Lincoln Cathedral with the permission of the conservators there, of course, and that was pretty much it. Three years at Loughborough.
Dr. Martin Cooper: The work at that time, initially it was sponsored by the Victoria and Albert Museum in London through John Larson, who was head of the sculpture conservation there, so he got that program set up and running.
He then, while I was doing my PhD, moved up to Liverpool to National Museums Liverpool so this project went there with him.
Dr. Martin Cooper: By the time I finished my PhD, John had managed to get more funding to continue this research and development work we were doing. I finished my PhD then moved up to the Sculpture Conservation Department of National Museums Liverpool.
Jason Church: You were there for…
Dr. Martin Cooper: Initially I thought I was going to be there for a couple of years, ended up sticking around for twenty. No real planning there. Initially, we managed to get some funding from various charitable foundations in the UK to continue the work and help introduce this technology in the UK and training up conservators at the Museum there.
Dr. Martin Cooper: Many sculpture conservators to work with the laser. It became fairly routine standard technique that they were using. We started to run training courses where we had conservators coming from around the world started running four of those a year. Yeah, I spent I guess about ten years working with the laser cleaning side.
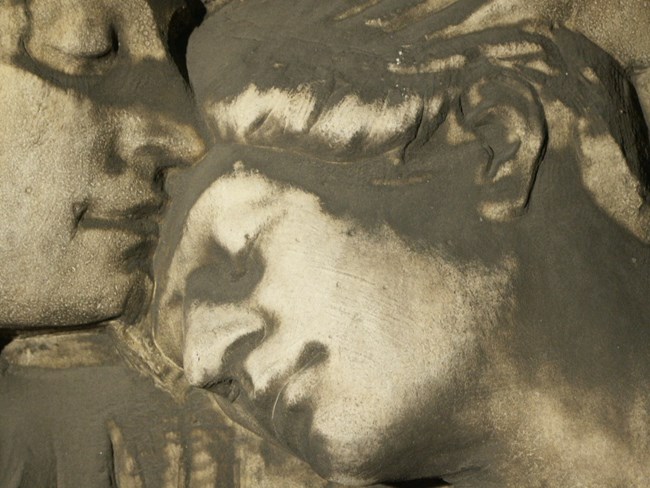
Lynton Lasers
Laser Ablation of Different Materials
Dr. Martin Cooper: I’m looking at the interaction of laser ablation of different materials as well, so all sorts of sculpture materials, things like limestone, marble, conductor stone, terra cotta, plaster, also doing various projects with students, so I’m looking at interaction of laser ablation with textiles and parchment and so on.
Dr. Martin Cooper: After about 10 years, we began to get a little bit more interested in 3D laser scanning and we were successful in getting a big grant from the UK Government, which enabled public sector organizations such as the National Museums to basically generate funding instead of start to commercially exploit the research and development that they were doing
Dr. Martin Cooper: The Museum in Liverpool, which gleaned that we started offering our services on the laser cleaning side and sculpture conservation, but also on the 3D laser scanning side to other museums, to heritage organizations, Liverpool authorities, and so on, as a way of furthering the technology, introducing it, and so on. Also, it’s we’re generating income potentially for the Museum, which could then go on to funding more development and research work and so on.
Dr. Martin Cooper: I think I spent about 10 years working with my colleagues there, Marie la Ponce and Joe Parsons and various other people looking at developing 3D laser scanning techniques for cultural heritage applications, so very accurate 3D recording of sculpture, for example, monitoring decay, or replication artworks, which were at risk, that kind of thing, and also for reverse engineering and producing missing parts of sculptures and monuments that were being restored.
Replicating Art
Jason Church: You mentioned replicating. How does that process working?
Dr. Martin Cooper: We were using; we were keen to develop or look into application of 3D scanning on the replication side. Being able to use that in a way, which allowed us to replicate sculpture without touching the surface. We were working with very fragile pieces, which you just couldn’t touch, you couldn’t take a mold from, maybe a piece where maybe it’s been outdoors, it’s so badly degraded, someone’s decided it has to come indoors, and then we can create a very accurate copy, which can go back in place.
Dr. Martin Cooper: We would typically scan the original object, two resolutions of about .1, .2 millimeter, then process the data to produce a very accurate 3D computer model, and then that could then be used to create the physical model and physical replica either go down two different routes that you go down, one of which would be computer-controlled machining where we could use the data captured from the scan to control a very accurate 3D milling machine to cut out a copy direct into a block of stone or we could use 3D printing technology.
Dr. Martin Cooper: Again, using the scanned data, to print a very accurate model, which itself could be the replica piece on this piece or we could then use that as a master pattern and take a mold from it and then cast into whatever material we want to use in these sorts of technologies.
We are able to very accurately replicate marble busts in marble or into bronze, all those kind of things.
Jason Church: You moved on from that. Now you’re with Lynton Lasers.
Dr. Martin Cooper: That’s right.
Jason Church: Tell us a little bit about what you’re doing now.
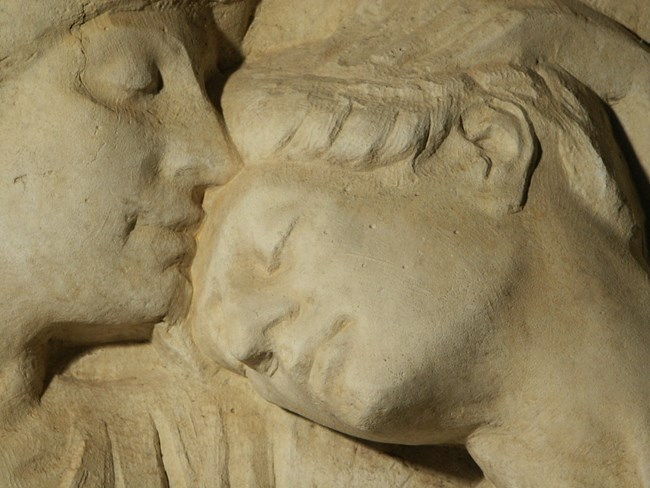
Lynton Lasers
Lynton Lasers
Dr. Martin Cooper: I left actually Museums of Liverpool just over a year ago. I’ve known the guys at Lynton for 20 years, and Doctor Andrew Charlton, who’s the Chairman there at a meeting we had a Liverpool University years ago, got talking, and realized that the laser cleaning technology that we were using, for sculptural conservation, was very similar to the technology that Lynton Lasers was using for cosmetic and medical applications such as things like tattoo removal, for example, it’s the same type of lasers. They were, Andrew was very interested in getting involved in conservation side, same kind of technology, new income streams.
Dr. Martin Cooper: We worked with Lynton for a few years there to turn the prototype laser cleaning system that we had in the studio into a more user-friendly commercially-available piece of laser cleaning equipment. I think initially when Lynton got involved in the conservation side; they were expecting conservation to be quite a lucrative market. I’m not sure where he got that idea but I think quite quickly I realized that wasn’t the case but it was a very interesting field to be involved it.
Dr. Martin Cooper: The bulk of the company’s business is medical and cosmetic but they’ve been involved with conservation now for 20 years, small parts of the business, but interesting part of the business, and yeah, when Andrew found I was leaving the Museum, he offered me some work at Lynton just to see if we could spend a bit more time concentrating on the conservation side to help it develop and maybe offer a few new things, not simply building the lasers to sell, but also offering things like training courses, consultancy, testing, that kind of thing as well.
Dr. Martin Cooper: I’m now involved on working full time with Lynton purely on the conservation side and so helping them make contacts in the conservation field, sell lasers, install lasers, train up conservators to work with it, work with conservators to carry out testing, that kind of thing.
Jason Church: What kind of things do you cover in the training workshops that you do?
Dr. Martin Cooper: Usually start off with a bit of background information about laser cleaning, where it’s come from, right from the beginning when lasers were first built back in the 1960s, when the pioneering work of Dr. John Asmus in the early 1970s and a bit of the history of the laser cleaning, look at what basically what a laser is, what laser radiation, what’s unique about laser radiation, why is it useful for cleaning applications, properties of laser radiation, look at a little bit about how the actual cleaning works, so what mechanisms, the underlying mechanisms behind laser cleaning.
Dr. Martin Cooper: We’re working on artworks, and then obviously there’s the practical side and just going through setting up the laser, how to use it safely, looking at the health and safety issues, of course, also how to use it safely on an artwork as well from testing to practical work.
Laser Scanning & Cleaning
Jason Church: Can you tell us about interesting projects that you worked on in your career with both laser cleaning and scanning.
Dr. Martin Cooper: Certainly on the laser cleaning side, it’s only, if you were lucky enough to visit lots of interesting places both here in America and Boston and Philadelphia, and more recently I’ve been out to Australia to work conservation workshops there.
Dr. Martin Cooper: I’ve certainly been lucky enough to travel and meet very interesting people. The thing about particular projects in the early 1990s, when it was still a relative, although John Asmus has done a lot of the work back in the 1970s, in the 1990s, it was still pretty much a new and innovative technique.
Dr. Martin Cooper: We did quite the interesting tests there where we would take out our old prototype Nd-YAG laser cleaning system that we’ve thrown together in the lab in Loughborough, where we’d literally you’d just gone and bought a laser off the shelf, built a trolley, screwed it together, stuck an arm on top, and there you go.
Dr. Martin Cooper: That was our prototype piece of kit, which we would then shove in the back of a very clapped out old van and take to various places and doing all sorts of cleaning tests on bits of cathedrals such as Lincoln, we’d go ahead and do some work there with the conservators.
Dr. Martin Cooper: We’re doing some cleaning tests on the outside of Victoria and Albert Museum years and years ago, quite high up, various other cathedrals in the UK, we did some work on the Houses of Parliament as well. Certainly around the UK, we’ve left our mark usually in the form of a few cleaning squares, maybe a few centimeters square that probably touched since we’ve been back.
Dr. Martin Cooper: We did one some cleaning tests with Lynton when I was at the Museums of Liverpool, we out to Copenhagen to what’s called the Marble Church in Copenhagen now where the conservators were very interested to try and look at using laser technology to remove thick, black pollution crusts from things like Swedish limestone and then Norwegian marble on the cathedral, on this particular church, but that was a long up from the scaffolding.
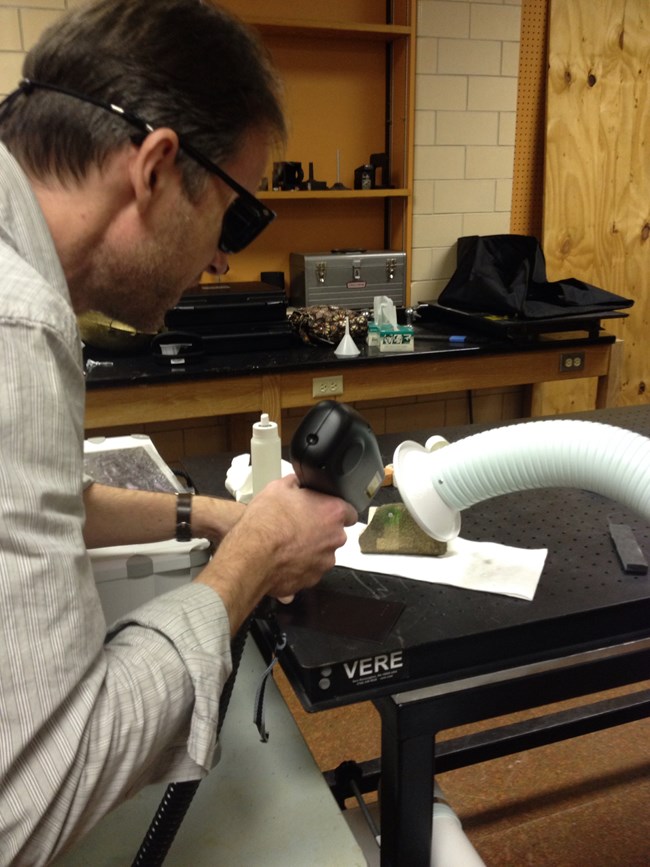
National Park Service
Dr. Martin Cooper: I remembered that from moving and the wind quite hairy moments where we shipped, we’d flown the laser out, which at that time was quite a big, heavy unit, seen that it was all weighing maybe 100 kilo.
Dr. Martin Cooper: It was hoisted up on a very fragile-looking hoist. I’ve still got pictures of it being suspended 100 feet in the air, fingers crossed, hoping that it was going to get onto the scaffolding okay. It turned out all right. Looking at the scanning side, because again, there were a few people in the UK doing the kind of work we were doing at that time, we tended to get involved in all sorts of weird and wonderful projects that no one else would go near.
Dr. Martin Cooper: You had other laser scanning bureau services, more typically we used to scanning engineering parts, bits of cars, that kind of thing, nice, smooth surfaces, but they wouldn’t be interested in scanning bits of artwork, which obviously far more complex and involve a lot more processing of the data afterwards to get good results.
Dr. Martin Cooper: We tended to get the most interesting projects, which initially we would take on and that sounds good and then you scratch your head a bit and think, “I’m not sure quite sure how we’re going to do this,” but we muddle through and get some quite interesting results and we help develop the applications and the technology, but we were involved in reproducing a marble bust of Emperor Caligula for the Glyptotek Museum in Copenhagen, which is one of the early projects we got involved with, and also we did a gilded bronze head of Minerva for the Roman baths in Bath in the UK, which was quite nice.
Gilded Bronze Head of Minerva
Dr. Martin Cooper: Obviously that involves quite a few steps in the process so basically this head of Minerva is one of their main pieces, important pieces, gilded bronze head; it was too fragile to touch. You can’t take molds from it so we were able to scan this head.
Dr. Martin Cooper: We then printed a master pattern into nylon, our process called selective laser sintering, and to finish that off, so take out the build layers so that these models are built up in layers of about 0.1 in thickness. Take out these contours, hand finishing, that was then sent to the foundry, that was cast into bronze, then came back to us, patinenated the surface and re-gild it, conservators in the sculpture department worked on that one.
Dr. Martin Cooper: Remember, we’re doing one project, which lasted a bit longer than we anticipated. We’re working for Manx National Heritage for the conservator there, Christopher Weeks, who I’ve known for years, who was interested in scanning a boat, 18th century boat, I think the last of its particular type, so it’s about 8 meters long.
Dr. Martin Cooper: Normally to scan something of that scale, you wouldn’t use close-range laser scanning, so you wouldn’t be scanning it to a resolution of .1, .2 mill. You’re using one of the longer-scale scanners type thing that we can use on buildings.
Dr. Martin Cooper: The problem was, this particular boat was in a cellar, this old building, and there was only about a meter clearance all the way around, and it was actually very close to the sea, very muddy cellar, and in the olden days, this boat had gone out of the doors, which you could go straight out into the docks, so basically when the tide came in, the wind was blowing in a certain direction, this is on the Isle of Mann, the water came in, because you couldn’t get one of these long-range scanners to scan it, the only option was to use a close-range scanner.
Stitching Complicated 3D Scenes
Dr. Martin Cooper: We took this really expensive, very accurate piece of kit from our studio, nice warm studio, into this cellar, and spent a week, the two of us, me and Annemarie La Pensee spent a week in this basement in January in the Isle of Mann, freezing cold, water coming in, lapping at your heels, scanning this boat, basically having to leapfrog the tripod all the way around, so we ended up with something like 16 different stations or positions where we’ve done the scanning from. The only way you’re going to capture that data, great resolution, any problem you then got is how do you stitch all this data together into one model that’s useful for someone?
Dr. Martin Cooper: We got there in the end several months later well Annemarie did, you basically generate huge amounts of data and try it turn it into something, which is useful, but maintaining the accuracy of the models, so it’s quite challenging, so we learned a lot from that particular project.
Jason Church: Martin, Dr. Cooper, thank you for talking with us today. Hope to see you in Miami at AIC. I know Pam Hatchfield at the Museum of Fine Arts Boston is putting together a laser workshop as part of the AIC Convention this year, coming up in Miami, so I hope to see you there.
Dr. Martin Cooper: Yeah, I’ll see you there.
Jason Church: If not, maybe we can catch up with you at the next LACONA Conference.
Dr. Martin Cooper: Krakow, in Poland, 2016.
Jason Church: All right. Thank you for talking with us.
Dr. Martin Cooper: You’re welcome. Thank you.
Read other Preservation Technology Podcast articles or learn more about the National Center for Preservation Technology and Training.