Last updated: April 7, 2025
Article
Podcast 033: Historic Uses of Lime Mortar, and Its Continuing Importance Today
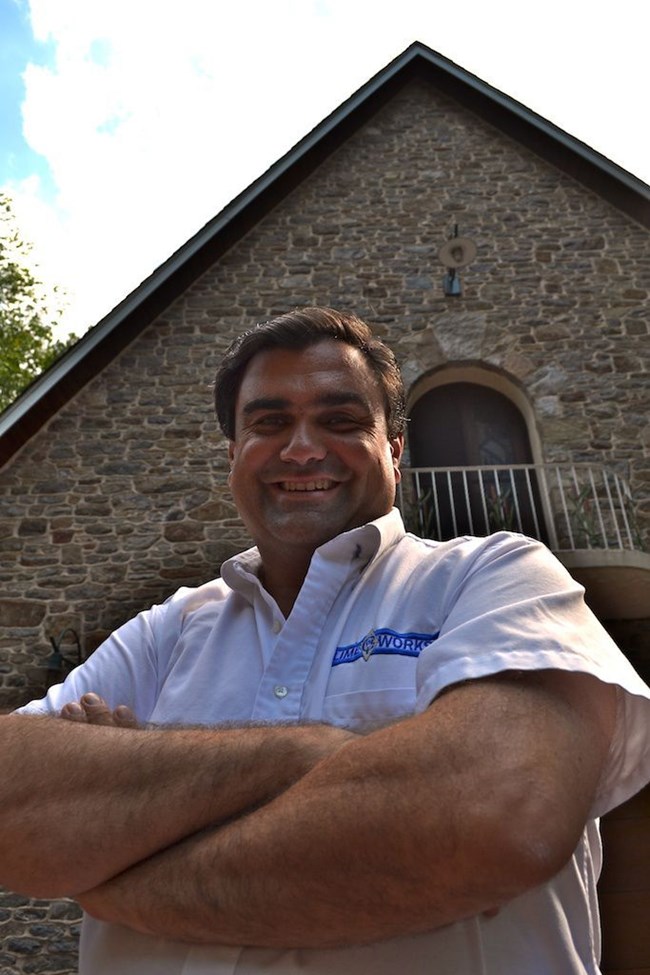
National Park Service
deGruchy's Project Portfolio
Jeff Guin: Tell me about a few of the structures that you have worked on.
Andy DeGruchy: We’ve worked here in Pennsylvania with my other company, DeGruchy Masonry & Restoration, for the last 27 years we’ve been restoring brick and stone buildings. Some of those have included work at Hope Lodge, Daniel Boone’s Homestead, William Penn’s Homestead, James Hobin’s (architect of the White House) memorial in Mt. Olivet Cemetery in Washington DC.
Andy DeGruchy: Also, a myriad of historic Victorian homes, farmhouses in Bucks County, Pennsylvania, where I live and all sorts of accoutrements, smokehouses, and summer kitchens and basements–some not-so-glorious buildings, but just a lot of hard work in the maintenance using appropriate materials to fix these vintage structures.
Andy DeGruchy: Well we’ve concentrated our work within about an hour and a half driving radius of where I live and where my shop is in Quakertown, Pennsylvania. However, we’ve done work as far as Florida and consulting work on the use of our materials as far as Puerto Rico and Maine out to Oregon and all over.
Jeff Guin: …and to Nashville, I know, because that’s where I met you originally at the NCPTT Nationwide Cemetery Summit. Are cemeteries something you work on frequently?
Andy DeGruchy: We do not do a lot of cemetery work ourselves, although I did mention I restored the architect to the White Houses’ James Hobin and his memorial in Mt. Olivet Cemetery, and dotted throughout our history, there has been some work on statuary and memorials.
Andy DeGruchy: But my connection with cemeteries has been at the prompting of a conservator and professor at Columbia who saw our laboratory and the work we are doing and said, “you know, you are the best kept secret, you really need to step up to the plate and tell the world that you are here,” and that is why we are even doing the radio interview now trying to get the word out that we have some great resources.
Types of Lime
Jeff Guin: Taking that a step further, there is a lot of confusion around the terminology related to lime mortars and specifications. I wonder if you could break some of that down for me. Talk about the different types of lime and the differences between historically accurate lime as compared to the improved or modern types.
Andy DeGruchy: Yes, that’s a very good question, and it is a little bit of a peeve with me because, you know, really lime is lime is lime and has been the same raw material from the beginning of time until now. Nothing has changed, but a lot of smoke and mirrors and confusion puts the end user, building owners, architects, engineers, and masons in a state of confusion.
Categories of Lime: Pure (98%+ Calcium) and Impure (Dolomitic or Magnesium)
Andy DeGruchy: Really, it is a very simple thing to understand:
- That is, lime has always fallen into two categories;
- it’s always been pure high calcium, 98% pure lime.
When I say lime, I do mean the shells and bones of marine life that build up over millions of years without any impurities in it. - If it was 98% pure, just comprised of that, then that is called high-calcium lime and then it falls into the second category, which is impure lime. Now we designate that into a breakdown of two areas.
- One would be dolomitic, which would have a smaller percentage of magnesium and then
- a magnesium lime which has a larger percentage of magnesium.
- it’s always been pure high calcium, 98% pure lime.
Ancient Structures Used Durable Materials
Andy DeGruchy: We look at ancient structures throughout the world, a lot of materials scientists will study them and say, “let’s not look at what is broken about this building, let’s look at what’s working so well that it is still here after 500 years.” They will find common denominators. And with the mortar, they find that the basic rule in masonry is, you never can fight water and win.
Andy DeGruchy: Water will always win in the end. So, the mortars in these ancient buildings had a lime and sand composition that would help to process moisture out to the atmosphere again. It would not trap moisture. Had it trapped moisture, or reacted with sulphates and other negative reactions, then the demise of the structure would have been accelerated, and it would not be here 500 years later.
Processing of Lime for Durability
Andy DeGruchy: But they found that when you use a lime that is a catalyst of processing water back to the atmosphere, now you have a symbiotic relationship with nature and with water. Therefore, you are now not in conflict with nature, but you are going to survive because you found a way to get along. The way that it does get along is that when the limestone, which could be a block of this sediment that I mentioned, is burned, it is the one stone that when you cook it for 48 hours, maintained at between 1,650 to 2,000 degrees, you will push off the carbon dioxide content in the stone.
Andy DeGruchy: In doing that, after the stone has cooled, it weighs 44% lighter than it did when it went into the kiln. When you reintroduce water to it, it will violently take that water in what’s called slaking–like slake your thirst–and it will boil the water it sits in within a 10 minute period.
Lime mortar draws atmospheric carbon dioxide, re-converting to lime
Andy DeGruchy: However, a little known fact is that if you look at that same mortar now that has been made with that lime putty and sand has been added to this putty that has had the water reintroduced to the limestone, you can go with a future 10 years, 20 years and 30 years and the lime is always slowly converting back into a limestone again through carbonation. It violently draws carbon dioxide out of the slaking bath at first, and it is a young buck at that time. But 5 years later, 10 years later, 50 years later, it is still trying to convert back into a limestone and will always draw carbon dioxide out of the air.
Andy DeGruchy: So that is the symbiotic relationship again with nature. When all these nor’easters and wind and water blow on buildings, they are delivering carbon dioxide and the lime mortar joints are hydrophilic. So these walls that get saturated actually give up their water towards the attracting lime mortar which then says, “can we have that carbon dioxide from you because we are still converting back into a stone” and then releases the rest of the vapor out to the atmosphere.
Andy DeGruchy: So this dynamic that has been going on, which material scientists have come to understand, is something that has preserved historic fabric. Because no longer does the soft sandstones and bricks that had they had the wetting and drying cycles go through there, faces would have exfoliated and been damaged. Now the historic bricks and stones give up their moisture to the hydrophilic in attracting lime mortar.
Roman lime versus modern lime
Andy DeGruchy: When the Romans who were famous as architects and builders, they burned lime at this time-honored temperature to maintain the reactivity of the lime between 1,650 and 2,000 degrees, it had the ability to convert back into a limestone. However, today’s modern production dead burns lime and in many cases and overcooks it. When you say to the lime that you can get it at any hardware store available in the country today, and say well, I’m going to add water and sand to you, I’d like you to convert back into a limestone and become as hard as hopefully you were at one time as a stone: that inert dust can only be used for adding plasticity, a flowability to a cement mortar or controlling the setting time of a cement mortar.
Andy DeGruchy: The majority of the available hydrated dolomitic Type S hydrated lime in the United States has just sand and water added to it as a stand-alone binder. It does not have the ability become as significant and durable as the historic mortars because of the burning temperature.
Andy DeGruchy: So the problem–although there is only two kinds of lime in the world and always has been–the way the lime is cooked has been changed in that it is being sped up for the process of production because the key elements it’s only asked to do today is that plasticity and control of setting time of a cementitious mortar. We have personally not had any success with using a Type S hydrated lime and adding sand and water and then putting it into service as an exterior above grade mortar in extreme free stall cycles like the northeast, mid-Atlantic states where I am from.
Andy DeGruchy: The limes to reproduce historic mortar when we work at some local building, someone might say, “Are you going to go build a kiln and find local lime and reproduce every element as it originally was?” Well, the cost becomes a problem, so we import the natural occurring hydraulic lime, which is pure high calcium and evenly dispersed silica so that we know when we add certain percentages of sand, we are going to get a final result that is going to have a known value for liquid and vapor permeability, PSI strengths … So it is true that in the United States and Pennsylvania, maybe these historic structures were not built with French hydraulic lime but it is a suitable replacement that pound for pound and cost-wise, is reasonable and we are putting in an in-kind replacement that will do no harm.
Jeff Guin: Do you see lime being used just in historic applications or are there new applications for lime now?
Andy DeGruchy: We have a 100,000 bag order for a tropical resort that we are creating a lime for a green build. Because, as I mentioned, the mortars that we have used for historic restoration, our intent was only to use them to do an in-kind replacement like-to-like–instituting no material that was going to cause an associated damage to historic fabrics surrounding the stone or brick, you know, like the window frame or something expanding and damaging because of what we used.
Andy DeGruchy: However, as I mentioned about people from the cemetery, conservators and fine arts finishing people–we’ve also found that it really meets the criteria for gold and platinum LEED credits. When you are trying to lower the embodied energy, the building of what has been used by reclaiming and recycling, you know, existing post consumer material and getting all sorts of energy advantages in improving indoor air quality, they find that the lime just to begin with–because there is 7,500 years of building history proving that it works, where modern cements although introduced in the 1870’s in the United States, in my opinion did not fully take hold until after WWII.
Modern lime is low efficiency
Andy DeGruchy: So the window of time where cement absolutely dominated for all veneer mortars and building and stucco and everything, came like 1945 until now. But the embodied energy to create a pound of Portland cement, which is the binder for modern stuccos and brick laying mortar and stoneware is incredibly high. Matter-of-fact, I believe the efficiency is very low because there is more waste than there is usable product.
Jeff Guin: Now lime mortar does have to be re-applied occasionally because it does work with the environment. How often does that have to be done?
Historic mortar superior to modern mortar
Andy DeGruchy: Well there are many historic structures that are in the United States that are only just receiving their first re-pointing. So, in the Philadelphia region, the area where I am from, we will see a historic building that you know, maybe was re-pointed in the name of preservation and maybe under the guidance of some government agencies and done only in the 1980’s, and yet it has to be re-re-pointed and it had a Type O or high lime content mortar with a little Portland cement added. Yet, the 200 year old buildings in this region (down the street from the one fixed in the name of preservation) we will find that sometimes these buildings are actually in better repair.
Andy DeGruchy: What my goal was originally was to import lime from France and do the things that we were doing was kind of pursuing excellence and saying you know, if there is the concept of getting a 100-year fix because we see that these buildings are 100 – 200 years old and no one’ s re-pointing them. They did not have the budget to fix it and it is in better shape than the one they did have the budget to fix.
Andy DeGruchy: Maybe we should try to mirror the properties of the original material. So, I would say that if a lime application is done appropriately, there is no reason–just like you see in Europe, old plaster over stone, brick and stone buildings or pointed buildings and no one is touching them for 100 years–there is no reason why you won’t get a 100 year life cycle if the project is done correctly.
Mortar Repointing
Jeff Guin: Is using lime mortars and re-pointing something that everyday people can do or is it just something for the experts?
Andy DeGruchy: It’s all dependent upon the skill level of the individual. So, we’ve met homeowners who do better work than some masons that we know and then we know young masons that their skill level just comes right out. So what it comes down to, just what pointing is. It is not rocket science. It’s just binder and aggregate.
Andy DeGruchy: It’s sand and lime and then it’s just placing that between bricks and stones but as you know and many who have observed historic buildings throughout the country, they will see blaring examples of bright white mortar that did not match the texture, the tooling, the color of the surrounding area and you have to wonder what were they thinking when they did that pointing job or built that wall like that and to this day, I still do not know what they are thinking but it is everywhere.
Homeowners: Workshops and Research
Andy DeGruchy: So, I think it boils down to not that it is so hard to do, but is someone willing to take the time and care for the project. That being said, some of our best customers, the ones who we love to work with, who are just savvy homeowners who have done their own research, they concluded what they wanted, how to do it, they will take a class and then they will take the time if they are going to do point the whole home, they will commit themselves to: “I’m going to do maybe one square foot but I’m going to do it right.”
Jeff Guin: Tell me about Ian Cramb.
Andy DeGruchy: Ian Cramb is a great man, 83-year old Scottish stone mason who lives in Bangor, Pennsylvania. He and his family have been steeped in stone masonry since 1750 in Edinburgh, Scotland and along the way. I think the common denominator of all these craftsman and artisans is love for the trade, and that caused him to assemble a book back in 1992 called The Art Of The Stone Mason. What made it very popular was in it, you could see the love he had for the trade and just carefully sketching out details describing how to cut a stone or how to build a stone arch or naming parts of a wall.
The Stone Mason’s Gospel According to Ian Cramb
Andy DeGruchy: All these things were very popular with masons because it was a throwback to how masonry had historically been done and those details again that is a common denominator that is going to make the outcome of any project become excellent and last for the 100-year fix. So, he began to develop a following of people in stone masonry and I being one of them, bought his book years ago and then of course he is local and I touched base with him about some things and became friends with him. Next thing you know, he had to get all the information together for his second book, which is The Stone Mason’s Gospel According to Ian Cramb.
Andy DeGruchy: As we drove along one day while on some projects we were building, he said, “You know, I can’t finish my second book and it’s all your fault,” and I said, “Well what you mean by that,” and he said, “You know, in all the conversations we have regarding the lime, you really have a better handle on the technical aspects and how to explain it than I do and I want to put that in this book.” So he asked me to edit and read through his book and understand what he is writing, then put some information that is going to clarify lime. So I helped him produce this second book with my computer science major son who is in college, to produce the book on the internet and we produced a few hundred copies and we have them now actually on our website for sale and that is The Stone Mason’s Gospel According to Ian Cramb.
Historic Masonry Trade Secrets
Jeff Guin: So you kind of see it as part of your job, your responsibility, to pass the knowledge along; to make sure that people understand not just why it’s important but what the history of lime mortars is.
Andy DeGruchy: Yes, very much so. I think that there was a time when masons would of course hide the trade secrets. They had their mason marks and they would mark the stones that they produced and shaped and dressed and they got paid piecemeal that way and some of the ancient trade secrets that sort of trail off into the Masonic tradition of the non-operating masons. In today’s masonry, as we know, all our buildings are accelerating in degradation and as the buildings are getting older and older and fewer and fewer people are going into the trade, it has been my position to say there is no more time for trade secrets.
Andy DeGruchy: If anybody wants to know a trade secret we are glad to share it because it just does not seem like anything that resembles close to actually doing physical hard work, is not getting much of an audience of young people wanting to get into it.
Cubicle to Trowel
Andy DeGruchy: However, those who do get into it, find it incredibly rewarding and then ask themselves, what was I thinking, I was going to go to college and I was going to be stuck in a cubicle somewhere, so I am very much in favor of disseminating knowledge, giving it away, but I see a lot of exploitation of historic resources for the sake of personal gain by keeping a patient sick and not getting in there and putting in a repair that would give a long service life, and so I am totally opposed to that and I want to blow the blinders off of that thing and I want to shed as much light on these subjects so that we can move on with the good and excellent conservation of our nation’s historic resources.
Jeff Guin: Andy thanks so much for being on the podcast.
Andy DeGruchy: I’m glad you could include me and hope that it was informative.
Read other Preservation Technology Podcast articles or learn more about the National Center for Preservation Technology and Training.