Last updated: April 7, 2025
Article
No Thermal Break, No Problem: Upgrading Kahn’s Stainless Steel Windows in the Richards Building
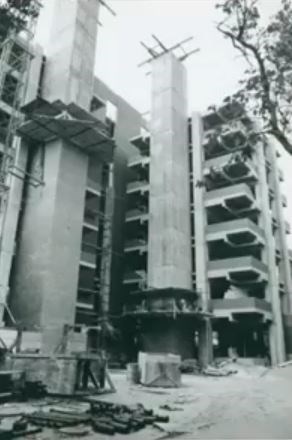
Louis Kahn Archive
Introduction
David N. Fixler: I’m going to venture out on a limb for just a second because James’ presentation recalled something to me, very poignant and very personal about something that happened a long time ago.
Loretta Venturelli who is an architect in New York in the late 1970s, and worked with Donald Judd on some of this work, and I only know it because she taught me in so many ways how to draw, and so much of what she was teaching us were the kinds of wonderful drawing she was doing on these buildings in Maurfa.
I can speak nothing to her involvement of the technical details, but it is, in terms of the power and quality of those buildings, always has resonated with me, and it was great to hear James talk about it in that way.
On to Louis Kahn, the Richards Laboratories, first of all, I want to thank the [National] Park Service and NCPTT and World Monuments Fund, all of you, for inviting us here today. We are honored and thrilled, and I think that they’ve given everything we’ve heard the last couple of days. I think there’ll be some interesting material to add to the archive here.
Louis Kahn: The Richards Laboratories Building
The Richards Lab, as many of you know, was a notorious building before it was even finished. Vincent Scully at the time, it was being designed by Kahn said it clearly, came right out and said, “This is a landmark working 20th century architecture. This is changing architecture.”
The buildup was such that, before the building even opened, it had a solo show at the Museum of Modern Arts, so this is a very, very important building. It’s a building about the integration of structure and systems, and the whole notion of servant and serve spaces, which Kahn became so famous for, really came to the fore for the first time in this building, but what’s poignant about it is you see this quote here.
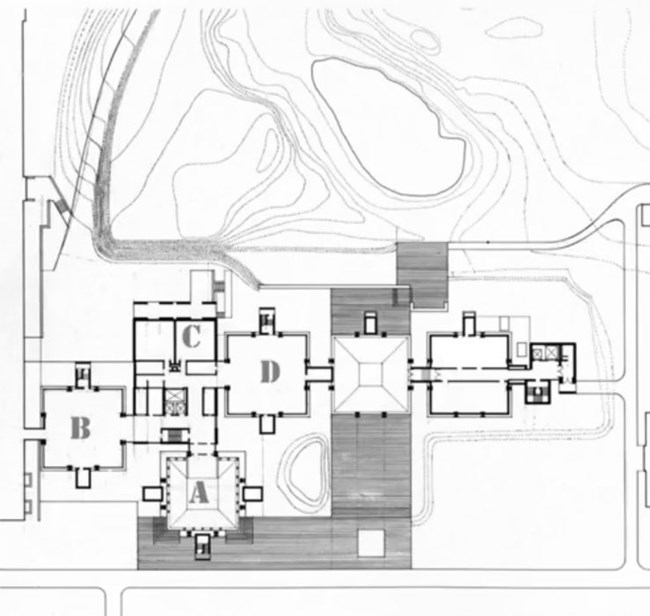
Louis Kahn Archive
What this is all about is, of course, he really thought of laboratories as being like architectural studios. People would want to work in this big, open, light-filled environments. Unfortunately the nature of the programming process, whatever he went through with the University of Pennsylvania in the later 1950s, he didn’t really get to talk enough to the scientists who were going to be using these labs and consequently from the day it opened, besides being internationally famous as upgrade architecture, it was famously dysfunctional.
To the point where the University of Pennsylvania, the people who used this building, were threatening to just leave or blow it up or do anything. But I say that, not so much to criticize the building, but to say to instill in you the need that we had to change things.
This is an instance where it is a national historic building, it is an iconic building, there are certain things you absolutely can’t change, but there was much, specially problematically on the inside, that had to change for the building to survive.
Looking at Richards, basically the original Richards is the four buildings that the four blocks that have the letters in them. The blocks to the right are the Goddard Labs, which were designed also by Kahn, but build subsequently, and under a little bit of a cloud, so a lot of the detailing that was realized there doesn’t come up to what you have in Richards, but it’s the idea of the servant. This is the servant, and these are the serves, so you basically have an essentially the brick box here, and these highly glazed tower surrounding it.
Here’s the building under construction. Kahn was very heavily influenced in the design of the structure of this by August Komendant. This was first collaboration with August Komendant, as a sort of visionary structural engineer who worked for 18 years with Louis Kahn, and wrote a very sort of tell-all book about it some years ago. Here you see the building going up, and the idea of the very strong expression of this reinforced concrete structure with these precast Vierendeel trusses, which cantilever off the columns that really formed the centers of each of the served bays.
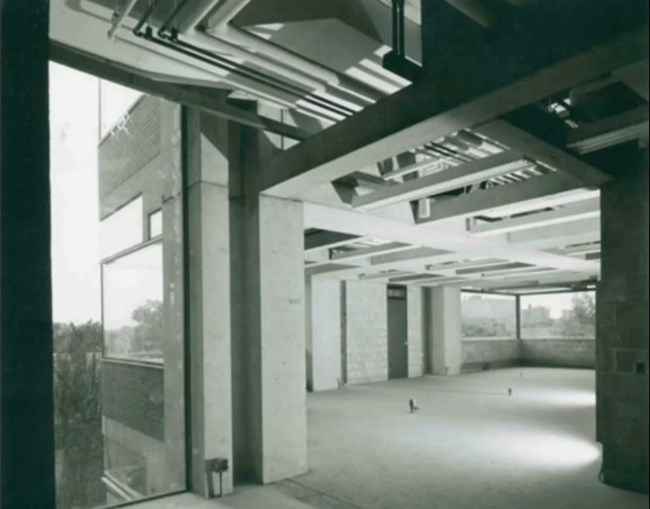
Louis Kahn Archive
Open Floorplans, Natural Light
The purpose of that was to open it up to the world at large, but also in Kahn’s notion of creating community, being able to see into each other’s lab, to be able to have this communication that is evident in this wonderful photo by Mildred Schmertz, shortly after the building opened. The idea that these enormous windows allow light and quality to permeate from one side to the other. Here you see the actual plan. The thing that’s important to remember, which we’re not going to go into in this presentation, but is certainly a very important part of the story, is that interior partition layouts within the glazed towers really were of no consequence to Kahn himself.
As I said, his preference was to keep them all open. However, they did conform to his system which aligned where the partitions really could be used on a line with the structural grid, and here is a reflected structural plan of a typical floor. You see these four squares within the nine squares of each of the corners. One of the things that we had to face was dealing with the fact that if you follow those lines, they don’t meet office standards, and I say, that’s a presentation for another time, but it was a very interesting challenge as to how we dealt with that in coming up with new schemes for the interiors of the building.
Here finally for this introductory piece is the tinker toy pieces in construction going together, and you can see the extent of the cantilevers that you have here, and part of that the movement because of the concrete creeping those cantilevers and the expansion of the brick were some of the things that we had to deal with in facing the changes to the glazing later on. Matt?
Matthew Chalifoux: Thanks, David. Coming through. As David said, there were functional problems from day one, but this another one of these pre almost construction finish photos, certainly gives a sense of what Kahn thought the spaces should look like on the interior. This is actually looking into Tower D from Tower C, so from the servant to the served towers. You can also see in this image, in the Vierendeel truss system above, the organization of some of the mechanical systems that fed the building, which is what I’m going talk a little about because it was also very important to the vision of the building. This is what we are faced with going into the building, so this is how the building has been used pretty much since it opened up. You could see the kind of overlay of systems and things that have been put in and the kind of degradation of the space based on how it was being used.
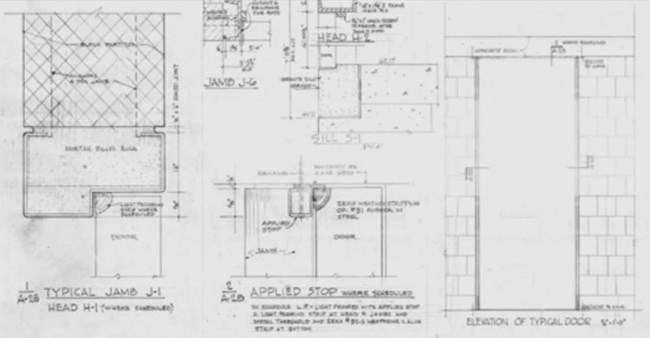
Louis Kahn Archive
Frugality: Energy & ROI*
*ROI : Return on Investment.
As David said, this incredibly important planarity of the exterior envelope, and the way the materials met each other, which has been partially compromised based on minor movements particularly around the corners of the buildings as it relates to the windows.
A critical decision that the university made prior to our evening engagement was the decision to change from wet labs to cognitive neuroscience in this building, which was going to take a lot of the kind of systems on pressure on the building, and allow us a lot of freedom in terms of how we’re going to be designing the building and designing the systems.
Our scope we’re working include initial feasibility study and then renovation of just two floors of two of the towers. It was a limited scope, although they’ve now moved into a full renovation of the entire building.
Penn was not prescriptive about the solutions that they wanted. They did provide a sense of their expectations. Just from the RFP, they stressed that they expected the high sensitivity and coordination between historic preservation, mechanical engineering, and space planning. The design should result in a high performance, energy-frugal, light-filled, and healthy building.
I stress that word “frugal” because it gave us a sense that Penn, which is very aggressive in their energy reduction targets for their buildings, both new and existing on the campus, saw this as a potentially different project. They were not mandating specific reductions, but they were asking us to be energy-frugal which was a nice way to start the project.
I just want to mention that David and I were backed up by an incredible team of people and firms. One of which I want to point you specifically, on the envelope windows are Heintges Associates out of New York, Loretta Polinsky and Aaron Davis.
Much of what they produce is critical to the presentation you’re seeing today. All of these people had to buy into the kind of design approach that we are developing even though the systems and everything are maybe typically thought of as independent. The final partner I want to mention is the construction manager, Intech, because many of the end solutions that were developed were only developed with the input of the contractor and the subcontractor to make sure that they would work.
One of the things that we wanted the feasibility study was to really be able to guide us in terms of how we were going to be dealing with the building. We had to think about some basic design principles that Kahn and his team have developed in developing the design. One of which was how all the materials in the building, the junctions between them, how they meet each other, and how they terminate, and these are snippets from some of the original construction drawings.
This happens to show two cinder block walls would meet, but also a typical door head window where you really only have jams, and you have no head to the window. It really simplifies the lines of the building, and it was something that we had to always keep in mind.
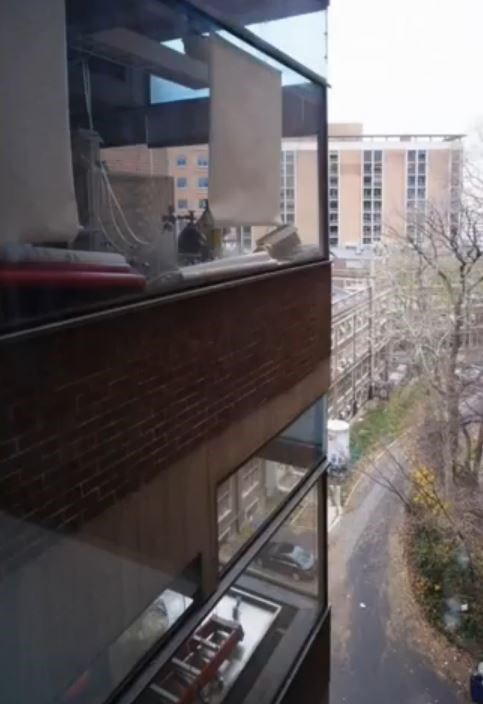
Louis Kahn Archive
Mechanical Systems as Visual Elements
On the mechanical systems, what was really critical in terms of the mechanical systems is that they were treated as a visual element in the building.
Kahn stressed the idea that the architect should understand everything about the structure, and the systems and the construction technology because it all had to be integrated into a whole.
It was not thought of as separate components. The layering and mechanical systems that’s sectioned, it’s at the bottom of the screen, shows how the systems were layered in the Vierendeel trusses were to highly organize them visually, but also to allow the systems to feed up to the floor above for electrical and telephone, and then for the mechanical systems to feed the level below, which meant that you had no systems that had to go through the zone that’s created horizontally by the windows. It’s a very, very important issue.
This diagram was from Tom Leslie’s book, “Louie Kahn Building Art Building Science” and it shows just the rigor of the layout of the systems, and how it was worked into the Vierendeel trusses, which again was something that we had to pay close attention to because we were going to be changing the building systems, but we had to think about what that meant in terms of these designs.
A quick diagram, one of the key things that the university also wanted to explore was the idea of changing from their standard design HVAC VAV systems and go to chilled beams systems. The benefit of this was both energy savings, but also further reduce the size of some of the duct work and the routing that we’re going to have to deal with, simplified some of the coordination issues for us.
We also had offshoot benefits specifically as it related to the window design. It also posed us with the problem though of we’re going to have new objects in the space, and what were they going to look like. Chilled beams, there’s not a lot of range of them available in the market, so again thinking about how they are going to lay out in the building. We did all of the layout design of the systems in rivet.
We used it as a design tool. We actually would use it in design meetings with the owner to understand exactly visually how this was going to look in the building.
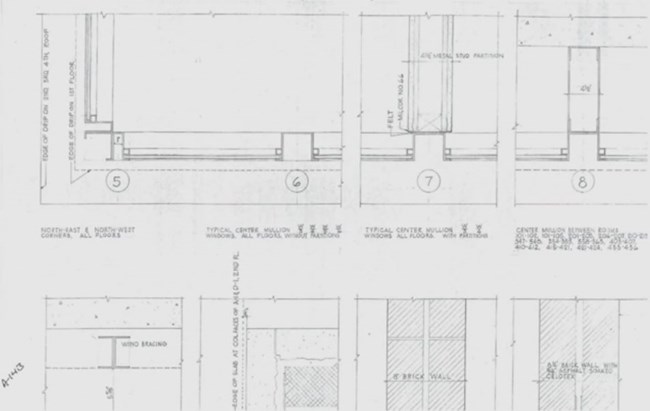
Louis Kahn Archive
Vitrine Windows & Elements on Display
David N. Fixler: Now we’re into the windows, this is a construction photo, and I think it shows a late construction photo. It is before they start to put in any of the interior partitions, and it emphasizes the vitrine-like quality of these windows, and the incredible Christmas ... of the system that Kahn was able to develop. I’ve been doing a lot of research on this system, and it is quite ingenious.
This is where the no-thermal break no-problem comes in because it does not have a thermal break, but it is an incredibly elegant system. Given all of the chatter that was happening in the 1950s and 60s about making very, very minimalist curtain walls, nobody really talks about just how well a job, how a good job Kahn did in achieving precisely that.
The building on the left is the AFL Medical Services Building that he did in Philadelphia, which was unfortunately torn down in the 1970s. But this is where he first began to develop this, basically it is a matte finish, break metal, stainless steel folded plate system that he uses to create these windows. There on the right, you can see a view down the window.
I also want you to take note, if you look really, really carefully, you can see a little bit how the brick wall comes out and the corner mullion comes in, and that kind of deformation in geometry was one of the really tricky parts that we had to deal with all along.
These are details of the, very quickly going to go through the evolution of Kahn’s thinking about windows, these are steel windows in the first proposal for the AFL Medical Building.
Similar to actually the steel windows, he did at the Art Gallery, which was of course, some of the building that he had finished right before then, but as he’s working through the design, he also proposes an aluminum alternate, and then finally goes forward with a folded plate, break metal, stainless steel system. Here are the design drawings, and then here are detailed drawings from the actual construction and submittals that went through in the construction.
He’s thinking very hard about this, and working on this idea of creating this incredibly sheer surface because there are no tubes. The sections are very, very light, and they get all their strength from just being folded.
Here now is a detail sheet from the Richards Laboratory. You see, first of all, the size of these lights, they’re almost 14 feet by 5 and a half, the big ones, and they were just quarter-inch polished plate. The dark sections that you see in the upper right hand corner are the actual profiles, a jam at the top, and the sill at the bottom of this.
You could see how incredibly minimal that is, and very, very little. The only projection really from the surface is where they had tracks for exterior shades, and a very, very minimal drip.
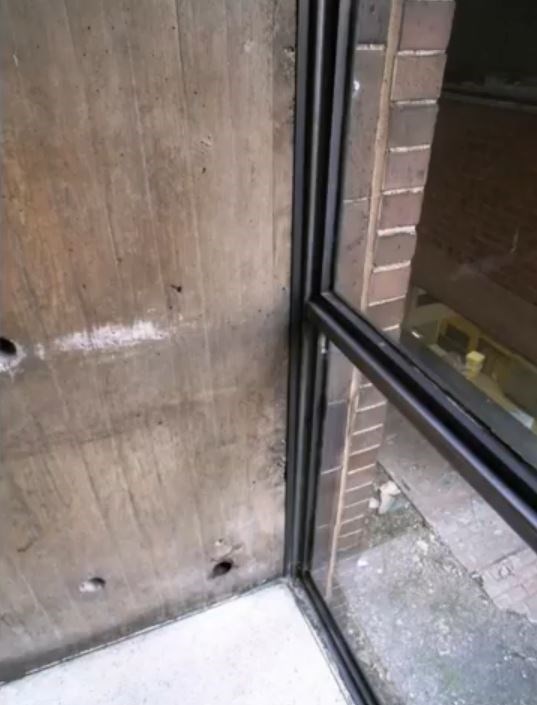
Louis Kahn Archive
No Perfect Solution
This is a pretty good look at an original installation as it stood about two years ago. Again the proportion of the wall, you can see there the numbers laid out, so obviously we’re dealing with a very, very high energy loads on this building. One of the things that people always talk about when we say we’re working on this is, “Oh yeah, that’s the building that’s covered with tin foil” because there was very little in the way of sun control that went along with this, and that was again, part of our mandate.
One of the things I just wanted to point out very briefly is that there is also, in the slot between the towers, a very early use of an IGU, these are the welded metal seams. Most of them, not all, but most of them had held up very well. Certainly better than you would expect a contemporary IGU being 52, 53 years down the road.
Looking here, again, at the existing condition, a typical section on the left, typical plan at that very, very elegant corner on the right, and obviously a big energy sink, so one of the things that we had to do since Penn, like many institutions, is trying to adhere to a mandate to achieve 30% energy reduction in a fairly short period of time.
There’s a large number of universities around the country that have signed on to this, and so they’re looking at every project with the idea of what can we do to be frugal, as Matt said, is possible.
They weren’t demanding, but they said you have to explore every alternative, so we did look. We said, “Okay, can we somehow mimic these profiles in a thermally broken frame?” Well, there are two problems with this. One, is the frame really is a little- Or three. The frame is a little bulkier, or maybe way bulkier than we would want it to be.
Two, and most important, you’re having to rip out the original frame which means you are disrupting both the concrete frame, and the brick and fill around it. Three, you still have the problem at the corner of the lack of a thermal break, so it’s never going to be a perfect solution.
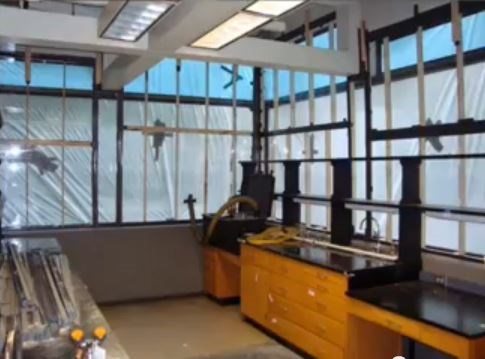
Louis Kahn Archive
We continue to develop, and again, looking on the left, that’s the existing. In the center, is saying, “Okay, what if we keep the frame, but still try to introduce an IGU?” This was just deemed to be too tenuous for a lot of reasons, and a lot of that had to do with the fact of the distortion that was planned, and it’s hard enough to take up distortion in a monolithic piece of glass, but to try to do it in an IGU because none of the replacement lights of glass were actual rectangles. They all had deformed corners of one kind of another.
High-Performance Laminated Glass
On the right, what we eventually came up with, and this echoes a little bit of what Walter said yesterday, the use of high-performance laminated glass- the idea that we could with a laminated glass, a significant improvement and performance over the quarter-inch polished plate, a more permanent solution because it does not have the problem of the degradation of the seals, and the ability to both put an inter-layer in this which would help in terms of solar control, still invisible, and keep it flat. It was very, very important, the flat quality of this glass, which you’re not going to get with an IGU, and you’re not going to get with tempered glass because of the roller wave phenomenon, but it is possible to do that with laminated glass.
Here at the transom, one of the things we had to deal with the laminated glass, which you see on the right, worries about the possible exposure of that piece of film. At the intersection between that two lights, we did some testing on that, it was determined not to be an issue with the glass, and so we went forward with that.
Matthew Chalifoux: Just quickly, we did do energy analysis on the building overall, our engineers really drove this. This was helpful in helping Penn come to grips with the decisions that they had to make. I didn’t mention before, we had a number of constituencies at Penn. We worked for facilities in real estate services, which is where the campus architect’s office is, but the building is occupied and essentially owned by the School of Medicine, so the funding for the project came from the School of Medicine. Their priorities weren’t all the same, in terms of what they’re trying to achieve out of the project, but you can see we did do a study of different ways of looking at the building, in terms of systems and glazing.
This was an early pass at understanding what kind of energy reductions we’re going to get from the design. Essentially the one on the left was the existing energy usage, and the one on the right, was using chilled beams with IGUs. You could see that’s obviously the best option in terms of energy reduction, but the difference between that, and just using chilled beams with a laminated glazing, wasn’t significant enough. The greatest energy savings was out of the mechanical systems upgrades, and not out of the glazing. It allowed Penn to sit back and think that maybe the preservation issues in this case were enough to drive the decision because they were getting significant energy benefits out of the other elements of the design, and that satisfied them.
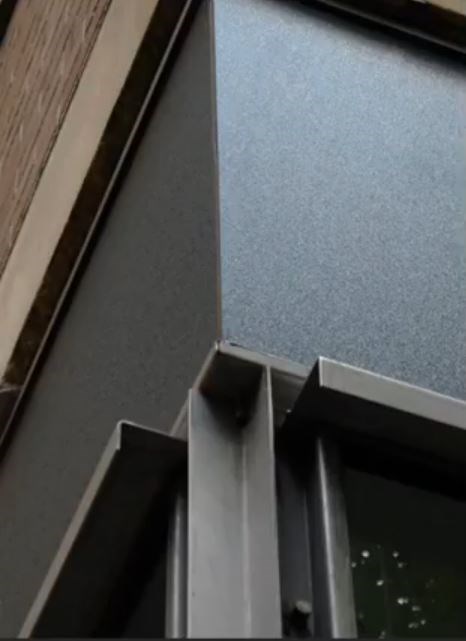
Louis Kahn Archive
The good news is that after the mock ups were done, we retested the new installation, and the CFM is down to below 1, 1 CFM well below what is allowable. Water penetration identified some weaknesses in workmanship that we were going to have to deal with in full installations, but really was at a level that was low enough that positive pressurization of the building with mechanical systems would deal with that, was not going to be an issue.
Mock-Ups & Installation
David N. Fixler: Now we’re getting to the actual mock ups and installation. The first thing we did was look at the glass itself, and because of the scale of these lights, we decided to make the glass choice prior to fabricating the full 14 by 5 and a half foot units.
We worked very closely with a couple of glass manufacturers, eventually settling on Viracon, looked at both the VLE 70 and VLE 85, looked at combinations of low iron and clear glass against two layers of clear glass, and a laminate, and finally came up with the closest match being the VLE 70 with a low iron on one side, and a clear glass on the other side, virtually identical to the original in appearance, but much, much more robust.
We also looked at, just in terms of the restoration of the steel itself looking at that corner, the steel was in excellent condition. There was no corrosion to speak of, and they were really the only things that we really had to do with it was lightly clean it because it is this very matte finish that Kahn would grow increasingly fond of as he worked through his career, this very, very almost pewter-like stainless steel finish.
It was really just a matter of re-passivating the areas where we were going to be re-glazing, and doing a very, very light cleaning on the rest of it. We did do a full corner mock up, two lights of glass and two of the big lights, and all of the transom lights. Looking up at the corner, there you see it without the clips. The reason we decided not to use the stainless steel clips is because they were not part of Kahn’s original detailing.
They were done for expediency because of concerns about how well that corner could actually be sealed, and we didn’t feel it was honest to put them back. They would be purely decoration. Frankly, it’s one of the things too, if anybody feels strongly enough about it in the future, you can go up and glue them on which is all they’d be anyway. The technology that one uses to put glass these days is far advanced from what it was in 1961, and so we felt quite comfortable leaving it the way it is, and as I say, more honest, a more honest approach.
There was a lot of discussion about exactly how to set these windows. We tried initially to do a mechanically fastened stop on the inside. We spent literally hours in the field arguing over an 8th 16th of an inch tolerances and dimensions to try to get this to be just right. In the end what we ended up with was a structural silicone sealing. We’re using a Dow 995 silicone to set the windows. The aluminum stop is adhered with a 020 VHB tape, but it really is not performing any structural function at this point. Here is the midst of that discussion that I talked about where we were looking at this. I think it’s a tribute to the designer, the specific designer of the glazing, Aaron Davis, he’s there on the left from Heintges.
I think also to the fabricator and installator, the people who put these things in and who were able to get the tolerances to such a way to accommodate all the deformation in a way that still pass, as Matt said, the test that we’ve run on these windows post installation. Here’s where we are today where the windows have been installed. They are temporarily braced until we get the stops, and just as a matter of precaution, but really the building from the outside doesn’t look any different, it just looks a little bit cleaner. I think once we’re done on the inside, if you’re going to notice differences, it will be elsewhere in the building, and not on the glazing. Thanks.
Abstract
The Alfred Newton Richards Medical Research Laboratory (Richards Building) at the University of Pennsylvania is one of the most important buildings in the career of architect Louis I. Kahn and one of the great buildings of the 20th century. Designed 1957-1958 and completed in 1961 the Richards Building was at the time deemed an architectural milestone worthy of a solo exhibition at the Museum of Modern Art in New York.
In 2008 the Richards Building was nominated for and granted status as a National Historic Landmark (NHL). As a NHL the building must be treated with exceptional care, with particular regard for its outward appearance and the integrity of its material palette. As an occupied, working building any renovations must with equal vigor and discipline consider necessary changes to the interior and exterior to better serve the functional purpose and the needs of present-day occupancy and operations.
One of the signature elements of the Richards Building is the remarkably detailed and constructed exterior envelope consisting of co-planar exposed concrete structure, brick and monolithic, polished plate, fixed glazing set in custom fabricated bent stainless steel frames. Kahn’s use of heavy gauge, matte (‘pewter’ in his parlance) finish sheet stainless steel, both as panel and brake-formed as a framing material became a trademark – though little discussed – element of his design vocabulary until the end of his career.
The use of this material begins with the AF of L Medical Services building in Philadelphia (demolished 1973) designed 1954-55, where we can witness Kahn’s testing early details utilizing more conventional rolled steel and extruded aluminum glazing sections before finally arriving at – and executing – a bent plate design. The system employed In Richards evolves out of these early explorations into one that uses the folded steel to create both shadows and strength, enabling a frame of unique lightness and remarkable elegance – that allows the glass itself to float almost weightlessly within the building frame.
A comprehensive renovation project was the catalyst for fully evaluating the exterior envelope and developing a design approach that retained the iconic visual and material characteristics of the building as viewed from both the exterior and interior while radically improving the energy performance and functional qualities of the building. This presentation will review the history and development of Kahn’s glazing system and unveil the comprehensive approach that was undertaken by an integrated design team including architects, engineers, materials conservators and building envelope specialists on how best to conserve the original steel framing and bronze entry doors while optimizing the overall performance of the exterior envelope and building systems.
The process included developing a detailed understanding of the original design intent for not just the building envelope but the entire construction including the engineering systems and using that knowledge as a basis for developing design alternatives and a conservation plan that responded to the stated design objectives at different levels. In concert with the owner and the contractor a final design was developed that best balanced preservation, energy efficiency, economy and constructability.
Speaker Biographies
David N. Fixler, FAIA is a nationally recognized leader in the field of historic preservation with a particular focus on the preservation of buildings of the mid-20th century Modern Movement. He has written and lectured internationally on the subject and has been an active leader in both APT and DOCOMOMO on the local, national and international levels since the 1990s. His projects have involved buildings designed by some of the leaders of the Modern Movement including Alvar Aalto (Baker House, MIT), Louis Kahn (Richards Building, University of Pennsylvania), Le Corbusier & Oscar Niemeyer (UN Headquarters) and Eero Saarinen (Kresge Auditorium and the Chapel, MIT).
Matthew Chalifoux, AIA is a Senior Historic Preservation Expert with over 30 years of experience in the renovation and rehabilitation of historic buildings. While his projects have ranged in scale from house museums to state capitols they have all included the sensitive insertion of new technology and systems to provide appropriate levels of climate control, life safety and security while also being environmentally sensitive and sustainable. His projects have received local, state and national awards for design, historic preservation and construction.
This presentation is part of the Mid-Century Modern Structures: Materials and Preservation Symposium, April 14-16, 2015, St. Louis, Missouri. Visit the National Center for Preservation Technology and Training to learn more about topics in preservation technology.