Last updated: February 14, 2022
Article
Multi-Functional High Performance “Green” Nanocomposite Coating For Metals (2018-05)
Long Jiang, Department of Mechanical Engineering, North Dakota State University
Xiaolin Qi, Center of Excellence for Surface Protection, North Dakota State University
Executive Summary
The goal of this research is to develop a removable coating material for metallic heritage preservation. Thermally reversible Diels-Alder (DA) reaction was used in this research to achieve the reversibility goal. Furan functionalized cellulose nanofibers, epoxy resin, and electroactive compound were synthesized. The furfuryl groups in these compounds can react with bismaleimide through the DA reaction to produce a thermally reversible coating system. Coating was prepared on steel test panels using different formulations and coating thickness. Coating hardness, solvent resistance, impedance, thermal property, and corrosion resistance were investigated. Differential scanning calorimetry and actual scraping tests confirmed the retro-DA reaction and that coating could be removed at elevated temperatures. The incorporated functionalized cellulose nanofibers increased the solvent resistance and rubbing resistance of the coating by increasing mechanical strength of the coating. Corrosion resistance of the coating was investigated by electrochemical impedance spectroscopy and prohesion (salt spray) tests. The results shows that the incorporation of the cellulose nanofibers can increase impedance of the coating, but lead to a higher number of coating defects, which deteriorate corrosion resistance of the coating. Further research can be conducted to improve the dispersion of the nanofibers in the coating to increase coating homogeneity and reduce coating defects. Research to reduce or even eliminate the brown color of the coating is also desirable.
Introduction
The coatings for metallic heritage preservation should provide strong protection from corrosion while should also be removable when needed. Traditional coatings are challenged to meet these contradictory requirements simultaneously and therefore innovative solutions are needed. Cellulose is the most abundant natural polymer on earth. It imparts structural strength to all plants through forming cellulosic fibers as the reinforcement, which are embedded in the semicellulose and lignin matrix of the plants. The cellulosic fibers exhibit a hierarchical structure (Fig 1a) 1 and the elementary cellulose fibrils can be isolated from plants to produce CNFs (Fig. 1b).
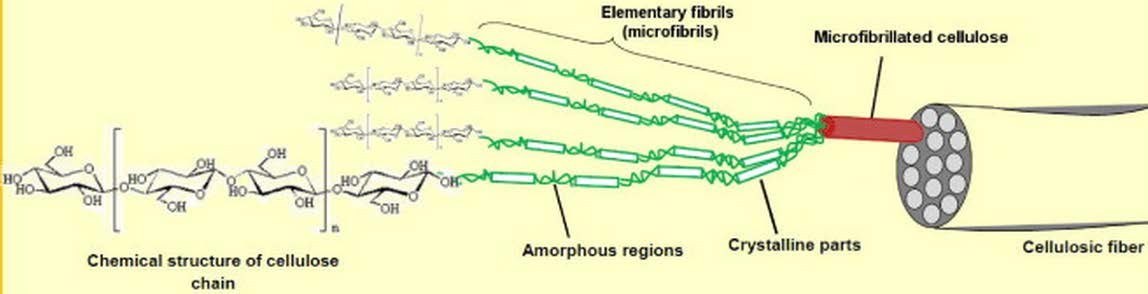
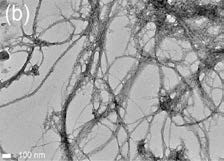
Research on CNFs has experienced an explosive growth in recent years. Among the many potential applications, CNFs are especially useful in the nanocomposite field as enabling or performance-boosting additives because of their nanoscale dimensions, high surface area, rich surface chemistry, low density and superior mechanical properties2,3,4,5,6,7 . Strength, modulus and toughness of the nanocomposites can be simultaneously increased at low cellulose nanofiber concentrations (i.e. without nanofiber agglomeration) as demonstrated by PI’s recent results2,3. Oxygen and moisture barrier property and scratch resistance of polymers can also be significantly improved by forming polymer-cellulose nanofiber composites or cellulose nanofiber coats on polymer substrates1,8.
Diels-Alder (DA) reaction has been recently used to produce thermo-remendable and recyclable thermoset polymers. In these systems, the thermally reversible covalent bonds (DielsAlder adducts) produced by the DA reaction break under heat (see Fig. 2), which allows removal and recycling of such thermoset materials9.

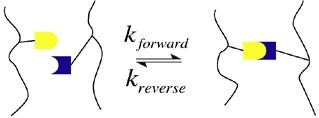
In this project, CNFs and DA reaction were used to develop a novel nanocomposite coating that could provide strong protection to metallic heritage and could be removed when heated. CNFs was incorporated into the coating to improve mechanical and barrier properties of the coatings for enhanced protection. An electroactive polymer (EAP) was also used in the coating to improve it anticorrosion performance. Both CNFs and EAP were functionalized for the DA reaction.
Materials and Methods
Surface modification of CNFs
Aqueous CNF suspension was dispersed in pyridine. The mixture was distilled before aminopropyltrimethoxysilane was added. The distillation continued overnight to hydrolyze the siloxane and to remove the produced methanol. More pyridine was added and the distillation continued to remove the watery pyridine azeotrope. The modified cellulose was resuspended in THF and refiltered several times. The modified cellulose was reacted with furfuryl glycidyl ether in THF at 69 °C and the product was filtered and washed with THF to eventually obtain furan functionalized CNFs (FFCNF).
Synthesis of furan functionalized epoxy resin (FFER)
Phenyl glycidyl ether (PGE, 0.5 equiv), bisphenol A diglycidyl ether (DGEBA, 0.75 equiv) and furfurylamine (FAM, 1 equiv) were reacted at 100o C under nitrogen for 15 minutes using monosodium-p-hydroxybenzenesulfonic acid (0.01 equiv) as a catalyst and hydroquinone as an inhibitor of furfuryl group polymerization. Isopropyl alcohol was used to quench the reaction and the mixture was refluxed and was finally dissolved in THF.
Synthesis of furan functionalized electroactive compound (FFEC)
P-phenylenediamine (1 equiv) and furfural (2 equiv) were reacted to produce a solid mass, which was then dispersed in THF. Sodium borohydride was added and the mixture was stirred under room temperature for 24 hours. The reaction product were purified by flash chromatography and vacuum dried.
Coating preparation
Coatings were formulated by mixing the three furan functionalized materials, i.e., CNFs, epoxy resin, and electroactive compound, and commercial bismaleimide. The fraction of each component was based on estimated stoichiometric ratios of the components. The coatings were applied on Q-panel standard steel panels using the draw-down method. The coatings were cured at 100o C for half hour. For comparison, the coatings containing FFER/bismaleimide and the coatings containing FFER/FFEC/bismaleimide were also prepared.
Hardness testing
Hardness of the coating was evaluated using a pencil scratch method. A pencil was selected (hardness between 10H and 9B) and a line (about half inch) was made on the coating. The test was started using the softest pencil. A harder pencil was used if the pencil did not scratch the surface. The first pencil that scratched the surface was reported.
Solvent resistance rub test
The coating surface was rubbed with cheesecloth soaked with acetone until failure or breakthrough of the coating occurs. The number of rubs was recorded at failure.
Electrochemical impedance spectroscopy (EIS) test
EIS measurements were performed using a Reference 600 Potentiostat by Gamry Instruments set up in the traditional three-electrode test configuration. The scanning frequency range was from 10−2 to 105 Hz with 10 points per decade. An O-ring glass cell was attached to the coating surface with a glass tube clamp and the cell was then filled with 3.5 wt% NaCl solution to cover the testing area of the coating. In this test, a platinum counter electrode, a saturated calomel reference electrode, and the metal substrate as the working electrode were used.
DSC testing
The thermally reversible Diels-Alder reaction of the coating was investigated using differential scanning calorimetry. The sample was heated at 10o C/min to 200o C. The heat flow associated to the reaction was recorded.
Prohesion test
The test was performed on the coated steel panels for 450 hours in a Q-Lab CCT Chamber. The electrolyte solution contained 0.05% sodium chloride and 0.35% ammonium sulfate. A two-hour prohesion exposure cycle includes one hour salt fog at 25°C and one hour dry-off at 35°C. 6
Results and Discussion
Coating observation
The coatings had a brown tint, especially when the coating was thick. This is due to the presence of the furan and amino groups, which darken over time in air. When functionalized CNFs were incorporated, roughness of the coating surface appeared to increase. These properties may be disadvantages for the heritage preservation application. Photos of the coated steel plates (1 mil and 2 mil coating thickness) are compared in Appendix Fig. 1.
Hardness test
All the coatings showed a similar pencil scratch resistance of ~ 6H. It appeared that the formulation changes did not cause marked variations in coating hardness.
Solvent resistance rub test
Rub test results indicated that both FFER/bismaleimide and FFER/FFEC/bismaleimide coatings started to show sign of coating failure at the 10th rub, and an almost complete removal at the 25th rub. However, the coating that contained the functionalized CNFs, i.e., FFER/FFEC/FFCNF/bismaleimide only started to show sign of coating loss at the 25th rub (Appendix Fig. 2). These results demonstrated that FFCNF improved solvent resistance of the coating, most likely through increasing the mechanical strength of the coatings.
DSC test
The Diels-Alder (DA) reaction produces a mixture of two diastereomers - the endo and exo adducts. During the reverse reaction (rDA), the endo adduct breaks first at a lower temperature followed by the cleavage of the exo adduct.10,11 Appendix Fig. 3 shows the rDA of the endo adduct and the exo adduct at about 110o C and 150o C, respectively. At 160o C, the coating softened significantly and felt like a liquid glue because all the D-A bonds were cleaved under this high temperature. The coating can be easily removed by scraping the steel panel surface using a spatula (Appendix Fig. 4A). The materials in the circles are the coating stripped from the panel surface by the spatula. Although the peak temperature for the rDA of the endo adduct was 110o C, the reaction actually started at a much lower temperature, and the softening of the coating could be noticed at about 80o C. Scuff marks could still be made at this temperature by the spatula (Appendix Fig. 4C), but it was harder to achieve than at 160o C, as indicated by the much less coating being removed by the tool. At 120o C, the coating showed an intermediate performance (Appendix Fig. 4B). The DSC and scrape test results collectively demonstrated the thermos-reversibility of the coating.
EIS test
Appendix Fig. 5 shows the impedance modulus as a function of the applied frequency. The curves measured after different periods of immersion time are plotted in one figure for comparison. The impedance at low frequency is a strong indicator of the corrosion resistance of the coatings. 12,13 Fig. 5A shows that the impedance of the FFER/FFEC/FFCNF/bismaleimide coating decreases with increasing immersion time, indicating its deteriorating corrosion resistance. On the other hand, the coating without FFCNF shows a more stable resistance with time (Fig. 5B), although its impedance is smaller than that of the first coating. We noticed that the incorporation of FFCNF led to increased coating surface roughness, which was likely due to the agglomeration of the nanofibers. The agglomerates could produce localized coating defects that allowed fluid ingression and therefore resulted in decreased corrosion resistance. The coating without FFCNF were more uniform and so provided more stable protection.
Prohesion test
The test results confirm the trend observed from the EIS test. In Appendix Fig. 6, sample A contains no FFCNF and it shows much lower degree of corrosion than sample B, which has FFCNF incorporated. Both samples show severe corrosion along their side edges, which can be ascribed to relatively poor coating cover on the panel sides. As explained earlier, the more severe corrosion on the FFCNF-incorporated coating is due to its larger number of defects caused by the FFCNF agglomerates. This issue can be alleviated by increasing coating thickness. Sample C was coated twice and it possessed significantly improved corrosion resistance, as shown in Fig.6. 7
Conclusions
In this research furan functionalized cellulose nanofibers (FFCNF), epoxy resin (FFER), and electroactive compound (FFEC) were synthesized. They were blended with commercial bismaleimide to form a coating system that exhibited thermal reversible behavior due to the reversible Diels-Alder (DA) reaction between a furan and a maleimide. DSC and actual scraping tests confirmed the occurrence of the retro-DA reaction and that coating could be removed at elevated temperatures. The incorporated FFCNF increased the solvent resistance and rubbing resistance of the coating by increasing mechanical strength of the coating. Corrosion resistance of the coating was investigated by EIS and the prohesion test. The results shows that the incorporation of the cellulose nanofibers can increase impedance of the coating, but lead to a higher number of coating defects, which deteriorate corrosion resistance of the coating. Further research can be conducted to improve the dispersion of FFCNF in the coating to increase coating homogeneity and reduce coating defects. Research to reduce or even eliminate the brown color of the coating is also desirable.
Acknowledgements
The PIs of this research are grateful to the financial support (grant # P15AP00088) awarded by National Park Service/National Center for Preservation Technology and Training. Dr. Mary Striegel, the point of contact of this grant at NCPTT, is greatly appreciated for her assistance and guidance since the start of the proposal.
References
- Lavoine, N.; Desloges, I.; Dufresne, A.; Bras, J., Microfibrillated cellulose - Its barrier properties and applications in cellulosic materials: A review. Carbohydrate Polymers 2012, 90 (2), 735-764.
- Xu, X. Z.; Liu, F.; Jiang, L.; Zhu, J. Y.; Haagenson, D.; Wiesenborn, D. P., Cellulose Nanocrystals vs. Cellulose Nanofibrils: A Comparative Study on Their Microstructures and Effects as Polymer Reinforcing Agents. Acs Applied Materials & Interfaces 2013, 5 (8), 2999- 3009.
- Xu, X. a. W. H. a. J. L. a. W. X. a. P. S. A. a. Z. J. Y. a. L. R., Comparison between Cellulose Nanocrystal and Cellulose Nanofibril Reinforced Poly(ethylene oxide) Nanofibers and Their Novel Shish-Kebab-Like Crystalline Structures. Macromolecules 2014, 47 (10), 3409- 3416.
- Eichhorn, S. J.; Dufresne, A.; Aranguren, M.; Marcovich, N. E.; Capadona, J. R.; Rowan, S. J.; Weder, C.; Thielemans, W.; Roman, M.; Renneckar, S.; Gindl, W.; Veigel, S.; Keckes, J.; Yano, H.; Abe, K.; Nogi, M.; Nakagaito, A. N.; Mangalam, A.; Simonsen, J.; Benight, A. S.; Bismarck, A.; Berglund, L. A.; Peijs, T., Review: current international research into cellulose nanofibres and nanocomposites. Journal of Materials Science 2010, 45 (1), 1-33.
- Habibi, Y.; Lucia, L. A.; Rojas, O. J., Cellulose Nanocrystals: Chemistry, Self-Assembly, and Applications. Chemical Reviews 2010, 110 (6), 3479-3500.
- Ten, E.; Turtle, J.; Bahr, D.; Jiang, L.; Wolcott, M., Thermal and mechanical properties of poly(3-hydroxybutyrate-co-3-hydroxyvalerate)/cellulose nanowhiskers composites. Polymer 2010, 51 (12), 2652-2660.
- Peng, B. L.; Dhar, N.; Liu, H. L.; Tam, K. C., CHEMISTRY AND APPLICATIONS OF NANOCRYSTALLINE CELLULOSE AND ITS DERIVATIVES: A NANOTECHNOLOGY PERSPECTIVE. Canadian Journal of Chemical Engineering 2011, 89 (5), 1191-1206.
- Poaty, B.; Vardanyan, V.; Wilczak, L.; Chauve, G.; Riedl, B., Modification of cellulose nanocrystals as reinforcement derivatives for wood coatings. Progress in Organic Coatings 2014, 77 (4), 813-820.
- Long, K. N., The mechanics of network polymers with thermally reversible linkages. Journal of the Mechanics and Physics of Solids 2014, 63, 386-411.
- Canadell, J.; Fischer, H.; De With, G.; Van Benthem, R., Stereoisomeric Effects in Thermo-Remendable Polymer Networks Based on Diels-Alder Crosslink Reactions. Journal of Polymer Science Part a-Polymer Chemistry 2010, 48 (15), 3456-3467.
- Froidevaux, V.; Borne, M.; Laborbe, E.; Auvergne, R.; Gandini, A.; Boutevin, B., Study of the Diels-Alder and retro-Diels-Alder reaction between furan derivatives and maleimide for the creation of new materials. Rsc Advances 2015, 5 (47), 37742-37754.
- Hinderliter, B. R.; Allahar, K. N.; Bierwagen, G. P.; Tallman, D. E.; Croll, S. G., Water sorption and diffusional properties of a cured epoxy resin measured using alternating ionic liquids/aqueous electrolytes in electrochemical impedance spectroscopy. Journal of Coatings Technology and Research 2008, 5 (4), 431-438.
- Bierwagen, G. P.; He, L.; Li, J.; Ellingson, L.; Tallman, D. E., Studies of a new accelerated evaluation method for coating corrosion resistance - thermal cycling testing. Progress in Organic Coatings 2000, 39 (1), 67-78