Article
Hanford: B Reactor Panoramic Tour
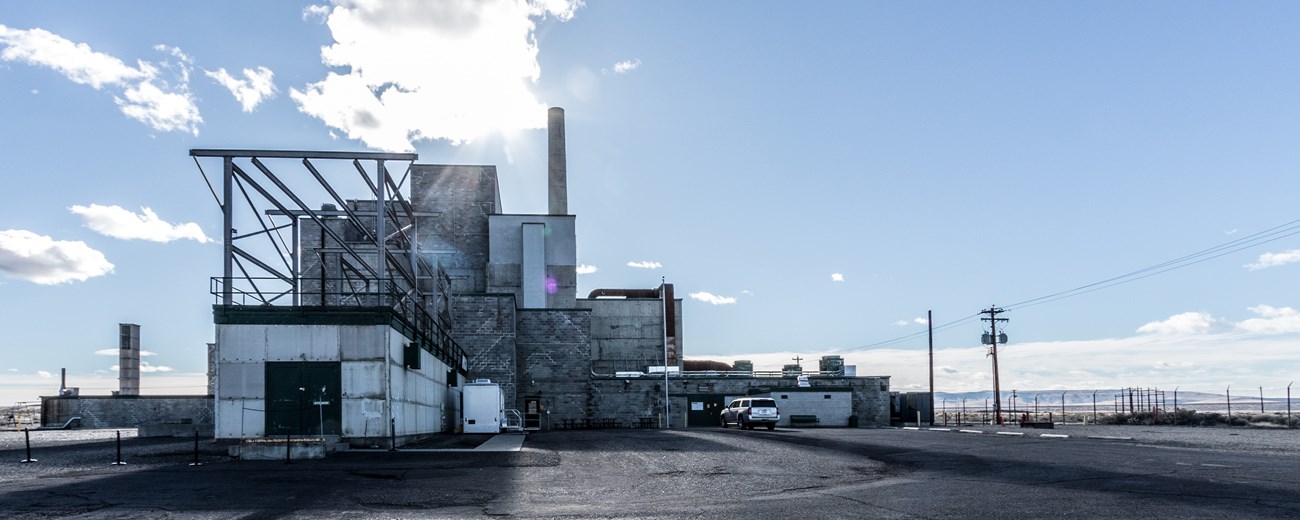
NPS/BURGHART
The Manhattan Project is one of the most transformative events in human history. It is a story of humans learning to control the power of the atom, which is akin to when humans learned to control fire. The Manhattan Project dawned the nuclear age, and the B Reactor played a key role in ushering in this new age.
The B Reactor on the Hanford Site in south-eastern Washington state is the first full-scale nuclear production reactor in the world. At the height of the Manhattan Project’s over 45,000 people from all walks of life and all 48 states worked at the Hanford Site. While many of the workers did not know their mission, their combined efforts proved that plutonium could be produced on an industrial scale. Plutonium, only discovered three years prior in 1940 by chemist Glenn Seaborg and colleagues, was a viable fuel for the Manhattan Project and America’s Cold War nuclear arsenal.
Under a contract with the federal government the DuPont Corporation began construction on the reactor in October 1943, achieving criticality on September 26, 1944. The B Reactor’s sole purpose during the Manhattan Project was to produce plutonium to fuel for the Gadget, the world’s first atomic test device, and Fat Man, the atomic bomb the US dropped on Nagasaki, Japan, on August 9, 1945. The B Reactor continued operation until it was shut down in 1968. It remained in “cold standby” until 1978 when it was permanently shut down.
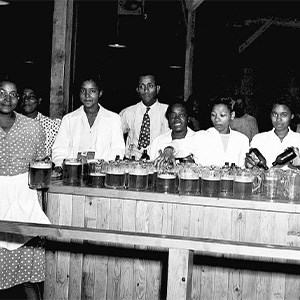
US DEPARTMENT OF ENERGY
Hanford Workers
Between the physicists of the Metallurgical Lab and the DuPont engineers and supervisors was a large workforce of skilled and unskilled workers. At Hanford, approximately 260,000 people were interviewed and around 120,000 were hired. Despite those massive numbers, the high point of the workforce was approximately 45,000 at any one time as there was a significant turnover in personnel, due both to the rough living conditions and the normal progression of crafts needed during construction.
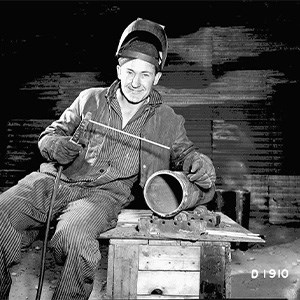
US DEPARTMENT OF ENERGY
At the Hanford construction camp, there were eight mess halls that served meals 24 hours a day. Meals cost workers 67 cents a day and were all-you-could-eat…and workers ate a lot. Each day 200 pounds (91 kg) of butter was used for sandwiches, 120 tons (181 mt) of potatoes were served, and 32,000 glasses of milk were drunk. Workers consumed 250,000 pounds (113,398 kg) of meat and drank 13 carloads of beer each week. A lot of calories were needed to power the Hanford workforce.
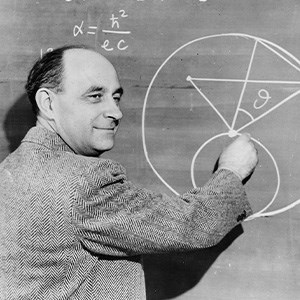
PHOTO COURTESY OF SMITHSONIAN INSTITUTION
The Reactor Pile
This is the front face of the B Reactor. Behind this enormous wall of metal pipes, tubes, and pigtails is the heart of the B Reactor, the nuclear pile. It was modeled after Enrico Fermi's CP-1 and later experimental piles. But the scale of the B Reactor dwarfed all aspects of its predecessors.
Enrico Fermi received the 1938 Nobel Prize in physics partly for his discovery of the effects of slow neutrons on the fission process. After receiving the Nobel Prize, Fermi and his family fled to New York to protect his Jewish wife from rising anti-Semitism in Italy. Fermi continued experimental work with slow neutrons and soon theorized that a self-sustaining chain reaction was possible.
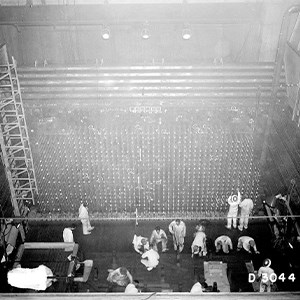
US DEPARTMENT OF ENERGY
Behind the visible front face are 75,000 graphite blocks precisely laid in place by bricklayers. The combined size of the 75,000 blocks are 36 feet wide (10.97 m), 36 feet tall (10.97 m), and 28 feet (8.53 m) front to rear. The graphite serves a valuable purpose in making the fission (splitting apart) happen. The graphite moderates (slows down or reduce the energy of) the fast (high energy) neutrons released by the fissioning of a uranium 235 nucleus. The slowed neutrons are then able to do two things: impact other U-235 atoms, causing another fission (a chain reaction), or be absorbed by the more plentiful U-238 atoms that might then undergo the transmutation process to plutonium 239.
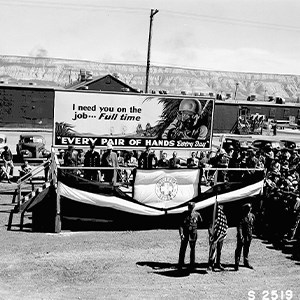
US DEPARTMENT OF ENERGY
The DuPont Company at Hanford
The federal government contracted the DuPont Company for engineering, construction, and administration of the plutonium production facilities at Hanford. The company provided design, project and construction management, and critical engineering leadership. DuPont’s Board of Directors were hesitant to take on the project because of the negative reputation they had received after WWI when they were accused of huge profits from munitions and branded “merchants of death.” The board was also concerned about the many unknown variables of the project and the scale of the commitment.
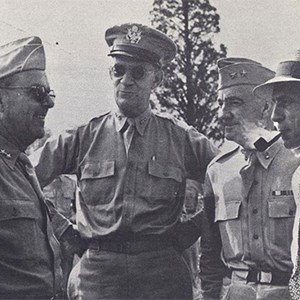
US DEPARTMENT OF ENERGY
DuPont requested a letter from President Roosevelt asking for clarification of DuPont's role in the project and refused any profits—agreeing to the contract only on the condition that DuPont would be reimbursed for expenses and receive one symbolic dollar as an award fee for completion of the project. In 1945, an article in a local newspaper stated DuPont received only 68 cents because an expense item of 32 cents was not allowed by an accountant. As a result, the Pasco Kiwanis Club collected one penny from each of their 32 members to make up the difference and sent it to DuPont along with a letter of appreciation for the work DuPont had done for the project.
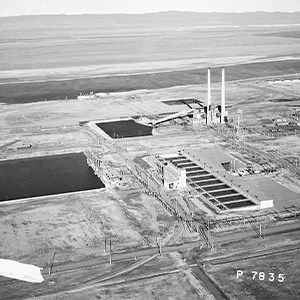
US DEPARTMENT OF ENERGY
Millions of Gallons of River Water
If you have ever stood near a thundering waterfall, you know it is hard to have a conversation with anyone nearby. The deafening sound of rushing water filled the reactor and most acutely in the valve pit. This is where the water for cooling the reactor entered the building. Initial water flow was approximately 27,000 gallons (100,000 l) per minute of water pumped from the Columbia River. When the reactor power level was increased to 2,000 megawatts in the 1950s, the water flow increased to approximately 70,000 gallons (264,978 l) per minute. This is a comparable water supply for a city with a population of 60,000 people.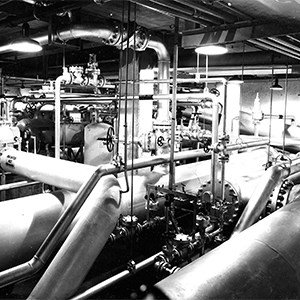
US DEPARTMENT OF ENERGY
Large diameter pipes delivered the much-needed cooling water to the valve pit. From there the water was divided into two sets of pipes that ran under the floor of the front face room. One set of pipes fed the right side of the reactor and the other fed the left side. If the flow of water to the reactor was ever interrupted, the reactor could overheat and melt down or irreparably damage the reactor core. DuPont understood this danger and developed backup systems to prevent such a disaster.
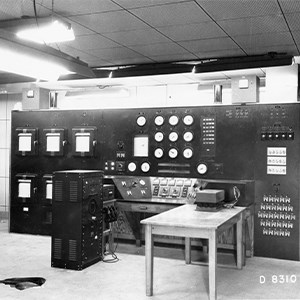
US DEPARTMENT OF ENERGY
5,000 Instruments
Operators in the control room had a big responsibility to keep the reactor operating safely. They had more than 5,000 instruments to monitor. Some instruments displayed their readings, others recorded them, sounded an alarm, or controlled the reactor. Just about all of them were in the control room. It was here that personnel controlled the power level of the pile and monitored the reactivity of the pile, the temperature of the graphite and shields, the temperature, pressure, and flow rate of the cooling water, and much more. A minimum crew of three people would be stationed in this room 24 hours a day, 7 days a week.
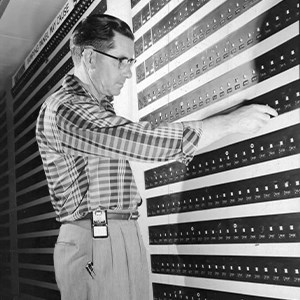
US DEPARTMENT OF ENERGY
A wall of 2,004 Panellit gauges, named after the company that manufactured them, measured water flow through each of the 2,004 process tubes in the reactor. Workers recorded the pressure from each of the Panellit gauges.
In an eight-hour shift, the crew would read one-third of the gauges and enter the data on paper. A sensing line ran from the inlet end of each process tube, just downstream of the orifice that controlled the flow of water, to the Panellit pressure gauges and switches in the control room. Two magnets on the dial were positioned for high and low trips. During initial use, small variations in pressure caused several accidental scrams, a fast shutdown of the pile, most often because the gauges were not properly dampened.
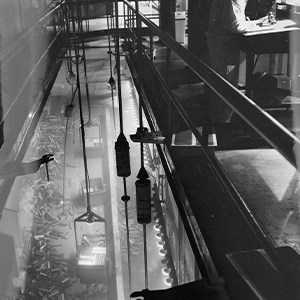
US DEPARTMENT OF ENERGY
Discharge and Cooling
Fuel spent a varying amount of time in the reactor, depending on where it was located within the core. Fuel in the center of the reactor received the greatest amount of neutron radiation and it might spend as little as four to six weeks, while fuel around the outer edges might spend six to nine months.
Every four to six weeks of operation, workers would shut down the reactor and go through a charge-discharge process replacing 10-20 percent of the fuel in the reactor. Fresh fuel would be pushed into the front of the reactor, which would cause the now highly radioactive discharged fuel to come out the rear of the reactor. The fuel would fall into the fuel storage basin, a 20-foot (6.10 m) deep water-filled pool. The water protected the workers from the dangerous levels of radiation given off by the irradiated fuel.
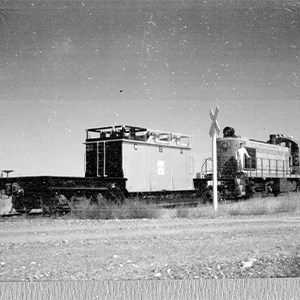
US DEPARTMENT OF ENERGY
Workers leaned over railings above the basin and used long tongs to place fuel into baskets. Once the baskets were loaded, they would be moved via the monorail system to the storage area of the basin where the irradiated fuel would be held for approximately 90 days to thermally and radiologically cool off. Thermocouples at the inlet and outlet of the storage basin measured water temperature, which was used as an indicator of radiation levels.
Once sufficiently cooled, the fuel was moved to the transfer area. There, a large overhead crane transferred the fuel baskets into water filled casks. These casks were then put into lead lined tanks on a flatbed rail car. Once loaded, the fuel was transported by rail to the T Plant to chemically separate the plutonium from the uranium and other radioactive byproducts produced during irradiation.
Last updated: February 8, 2024