Last updated: April 7, 2025
Article
Fiberglass Reinforced Plastic at the Fair
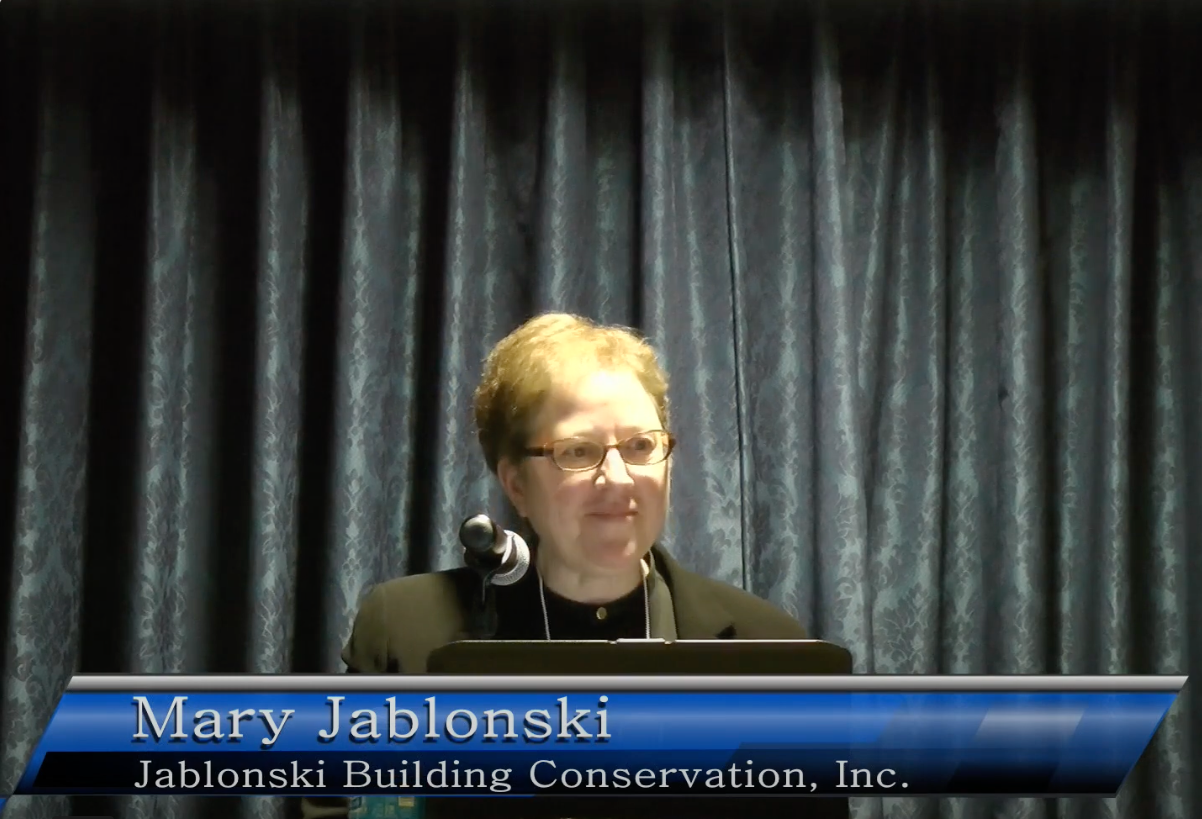
National Park Service
Plastics!
Mary Jablonski: So, take a front-row seat in a new era. It is an era in which man has created for his own better enjoyment of living, a whole new set of materials called “Plastics.” They behave as no materials have behaved before them ever behaved. So announced, the 1947, House Beautiful Special Edition on plastics.
The subtitle was “A Better Way to a More Carefree Life.” Many did heed the call to plastics and they are now used extensively. I defy any of you not to have been using plastics today. It’s impossible to get through a day without plastics. At the beginning, not everyone was quite so enamored with this material.
>While Richard Benjamin in The Graduate was able to reject the call, conservators do not have that choice. Plastics are completely pervasive throughout our entire environment. As we move through the 21st century, we are finding in a new era for conservation where we will be working with mid-century modern materials, particularly, plastics. Plastics is actually an umbrella term as there are many different types of plastics.
I’m going to use two case studies to illustrate this talk and to illustrate the difficulties of making decisions with this.
Fiberglass-Reinforced Plastics
The subset of plastics we are going to be looking at today is fiberglass reinforced plastics which come under the Thermosets. The two case studies are sort of quite different even though they are similar materials.
One is quite simple, one’s complex- one’s completed, obviously the simple one, and one’s still in study phase, but both of these studies were part of the 1964/65 World’s Fair in New York City. So we are continuing the theme. Let’s begin by taking a little bit of a look at what fiberglass reinforced plastics are.
Everybody has seen fiberglass reinforced plastics. Here’s two very common uses of them. While the development of FRP began in 1930s, it’s not really begun being used in manufacturing until the mid-20th century. Fiberglass was discovered by accident in 1932 when a jet of compressed air inadvertently hit a molten stream of glass. The resulting spray of fine glass was something that research has been working for years on.
Corning and Fiberglas
In 1936, two glass companies, Corning Glass and Owens-Illinois figured out how to do a glass fiber mat and a glass cloth they named Fiberglas, with one “S.” They were looking for a resin to embed it in.
DuPont actually by 1936 had come up with this resin, but they had trouble with the cure times. The Germans on the other hand did find a solution. So at the very beginning at the Second World War, the British Intelligent Agents stole the secret from them and brought it to the US where they gave it to American manufacturers.
Fiberglass: Polyester Resin & Glass Cloth
Ray Greene was a boat builder in this country, and he used this polyester resin to reinforce glass cloths. He actually made a fiberglass reinforced plastic boat in 1942. So war users were quickly found this material. Of course after the war, you had to find some new industry here or new users. With the post-war construction boom, FRP industry immediately went to the construction industry.
Lightweight & Strong
It was very attractive because here is a material that’s light with high strength. An opportunity to show case this material came about with the 1964/65 World’s Fair, particularly as the manufacturers had the dominant role in this fair. There were basic requirements which you sort of heard a little bit about previously about building here.
One of them was, they had to be inexpensive. They had to be easy to erect and very easy to disassemble as Fair the ground, of course if you heard, had to go back to being a park.
New Work Waived Materials & Requirements
New York City waived its 20-year longevity building code for this fair. However, the strength and stress requirements remained in effect. What better opportunity to demonstrate the use of modern materials, such as plastics, fiberglass, stainless steel and tempered glass.
Owens-Corning Fiberglas estimated that a million pounds of glass fiber was used at the fair to build about two dozen fair pavilions as well as telephone booths, dinosaurs and roofs. I’m guessing the money that came from this was what went in to enable them to build that fiberglass tower that we heard about yesterday.
The designs used here were often mid-century modern. They could be kitsch, and of course there was a futuristic element in many of them. Mind you, all three sort of attributes were found. While corporate pavilions with distinctive designs dominated the literature of the Fair, we are going to examine three small-scale examples of fiberglass.
Bench Conservation
These remnants have acquired significance because they are part of the very few remaining relics of this Fair that remained in-situ. In 2014, New York City Parks contacted me as they were wondering whether Columbia University Historic Preservation Program Conservation Workshop would be willing to conserve the 1964/65 World’s Fair Bench.
What they wanted was, they wanted at least one bench to go to the Queens Museum, so this was to be the bench. How could one possibly turn down such an opportunity to work with such good plastics? Four students, Catherine Gardner, Corey Manchenton, Marina Wisniewski and Dona Yu took up the challenge to work on these benches.
The 1964/65 World’s Fair was spread over nearly square-mile of land. People’s feet got tired. They got weary, and benches were an obvious solution. By the way, this is an actual photograph from the fair.
Originally 3,500 Benches
As benches were an obvious answer, 3,500 fiberglass slat benches were installed at a cost of $ 352,000 or about $100 a bench. Inexpensive. Today, there are less than three dozen benches left. The eight-foot benches have a nice, sleek, minimalist design- very décor-looking in a way.
They were done by the architect Gilmore Clarke and his firm who were actually working for Robert Moses who was of course, as you heard, in charge of the Fair. The benches have three legs, eight slats- five slats for the seat, three slats for the back-rest. The fiberglass slats were molded using a pigmented resin and they also had aluminum legs.
Two separate companies manufactured these benches. Hampden Brass and Aluminum Company of Springfield, Massachusetts cast the aluminum legs and the Universal Molded Fiberglass Corporation of Bristol Virginia did the fiberglass slats.
The benches were supposed to be maintenance-free. They were supposed to be unpainted although the aluminum legs had to be lacquered. The Universal Molded Fiberglass Corporation is now part of what is called Strongwell Corporation.
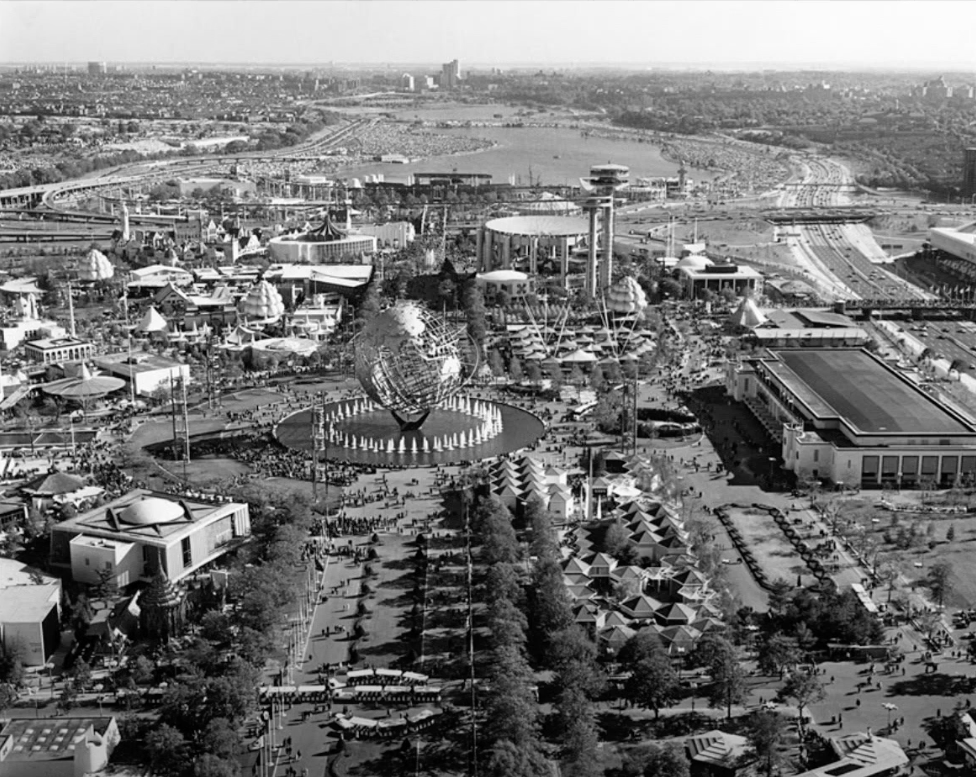
Gary Winogrand
Fiberglass: Corning Glass versus Owens-Illinois
In 1936, two glass companies, Corning Glass and Owens-Illinois figured out how to do a glass fiber mat and a glass cloth they named Fiberglas, with one “S.” They were looking for a resin to embed it in. DuPont actually by 1936 had come up with this resin, but they had trouble with the cure times. The Germans on the other hand did find a solution.
So at the very beginning at the Second World War, the British Intelligent Agents stole the secret from them and brought it to the US where they gave it to American manufacturers. Ray Greene was a boat builder in this country, and he used this polyester resin to reinforce glass cloths.
He actually made a fiberglass reinforced plastic boat in 1942. So war users were quickly found this material. Of course after the war, you had to find some new industry here or new users. With the post-war construction boom, FRP industry immediately went to the construction industry.
It was very attractive because here is a material that’s light with high strength. An opportunity to show case this material came about with the 1964/65 World’s Fair, particularly as the manufacturers had the dominant role in this fair.
There were basic requirements which you sort of heard a little bit about previously about building here. One of them was, they had to be inexpensive. They had to be easy to erect and very easy to disassemble as Fair the ground, of course if you heard, had to go back to being a park. New York City waived its 20-year longevity building code for this fair.
However, the strength and stress requirements remained in effect. What better opportunity to demonstrate the use of modern materials, such as plastics, fiberglass, stainless steel and tempered glass.
Owens-Corning Fiberglas estimated that a million pounds of glass fiber was used at the fair to build about two dozen fair pavilions as well as telephone booths, dinosaurs and roofs. I’m guessing the money that came from this was what went in to enable them to build that fiberglass tower that we heard about yesterday.
The designs used here were often mid-century modern. They could be kitsch, and of course there was a futuristic element in many of them. Mind you, all three sort of attributes were found. While corporate pavilions with distinctive designs dominated the literature of the Fair, we are going to examine three small-scale examples of fiberglass.
These remnants have acquired significance because they are part of the very few remaining relics of this Fair that remained in-situ. In 2014, New York City Parks contacted me as they were wondering whether Columbia University Historic Preservation Program Conservation Workshop would be willing to conserve the 1964/65 World’s Fair Bench. What they wanted was, they wanted at least one bench to go to the Queens Museum, so this was to be the bench.
How could one possibly turn down such an opportunity to work with such good plastics? Four students, Catherine Gardner, Corey Manchenton, Marina Wisniewski and Dona Yu took up the challenge to work on these benches. The 1964/65 World’s Fair was spread over nearly square-mile of land. People’s feet got tired. They got weary, and benches were an obvious solution. By the way, this is an actual photograph from the fair.
As benches were an obvious answer, 3,500 fiberglass slat benches were installed at a cost of $ 352,000 or about $100 a bench. Inexpensive. Today, there are less than three dozen benches left. The eight-foot benches have a nice, sleek, minimalist design- very décor-looking in a way.
They were done by the architect Gilmore Clarke and his firm who were actually working for Robert Moses who was of course, as you heard, in charge of the Fair. The benches have three legs, eight slats- five slats for the seat, three slats for the back-rest.
The fiberglass slats were molded using a pigmented resin and they also had aluminum legs. Two separate companies manufactured these benches. Hampden Brass and Aluminum Company of Springfield, Massachusetts cast the aluminum legs and the Universal Molded Fiberglass Corporation of Bristol Virginia did the fiberglass slats. The benches were supposed to be maintenance-free. They were supposed to be unpainted although the aluminum legs had to be lacquered. The Universal Molded Fiberglass Corporation is now part of what is called Strongwell Corporation.

Gilmore Clarke
Strongwell Corporation
If you look on their website, you’ll find that they’ve been working with plastics since the mid-1940s. What’s interesting is they were using a fabrication process since somewhere around the mid-1950s called the Continuous Automatic Process, which today they call pultrusion which allowed them to create these slats.
Essentially what they were doing was they were creating fiberglass ladder rail which is the same thing basically as these slats. I cannot emphasize how important the documentation phase was to this project. The students found and combed the archives locating original specifications, reports of testing and a fair number of period reports of these actual benches. Here’s one from the Japanese Times.
Also as part of the documentation, the piece of fiberglass was sent to the Metropolitan Museum of Art just to confirm exactly what the metrics was, which of course it was a polyester resin. The students also took a look at the paint layers and they basically found that the first paint layer, at least the first finish coat on it, was a light yellow-green. The most significant archive for the Fair is in the New York City Public Library archives.
There are blueprints there. Just because it’s easier to read, I put up actually the patent. What was even more interesting was there were testing reports for these benches. They were thoroughly tested before they were ever put out in the park. Testing found that if you tighten the bolts, you would actually crack the slats. However, if you tighten the bolts so that it was short of refusal, it was very easy to remove the bolts.
They actually had a major concern about vandals, so essentially what they did to solve this problem was they put washers underneath the head of the bolt underneath the slat and they glued them. There had to have been a form of epoxy. They glued the bolts into the aluminum legs. When the Fair was finished, the grounds and the benches were actually handed over to New York City Department of Parks and Recreation as we already heard.
There was actually a fair amount of documentation for how the benches were to be prepared for this handover. A contractor was actually hired to paint the benches that were originally meant to be unpainted, and a big note was made that the slats were not to be removed.
Anyway, they were painted with a marine grade paint, and needless to say, those benches have been painted many times since. By 2013 there was really a great concern amongst several people in parks that these benches were going to be lost forever.
So the fiberglass slats actually, in the benches, if you go to the park you’ll find that many of them replaced with wood. I’m going to verify here. I actually sat on both types of benches. Those fiberglass slat benches are so much comfortable than a wood slat bench. Anyway, the Park’s department wanted this bench, at least one of them, left as relatively intact.
So we very carefully selected actually a bench. We went through the park finding a bench with intact slats and one with none of the slats appeared to have been replaced. There may be close to three dozen benches left. Most of them are not intact and what you’ll see is what you see on the screen here, that essentially when these slats are broken, they just cut them off, at least at the breakers at the ends. While we were there, we actually saw a slat being broken as they were setting up for the US Open.
When you replace the slats, one of the things that happens is that the opening where the bolt goes in on the slats widens so you can see they have to use a washer. So it’s fairly easy to tell which ones have been replaced. The other problem was we could see white there the mat actually was not very well embedded in the resin.
So in the fall of 2014, an intact bench with its original fiberglass slats and aluminum legs was delivered to the Conservation Laboratory at Columbia. After the very thorough documentation, the students undertook a conditions’ assessment, and the bench that came to Columbia did not look very impressive.
The slats were heavily painted with up to ten layers of paint and the paint was peeling badly. Also the aluminum had paint drips everywhere as you can see in this image. We’ll be focusing here on the FRP instead of the aluminum although the aluminum was actually quite interesting for treating.
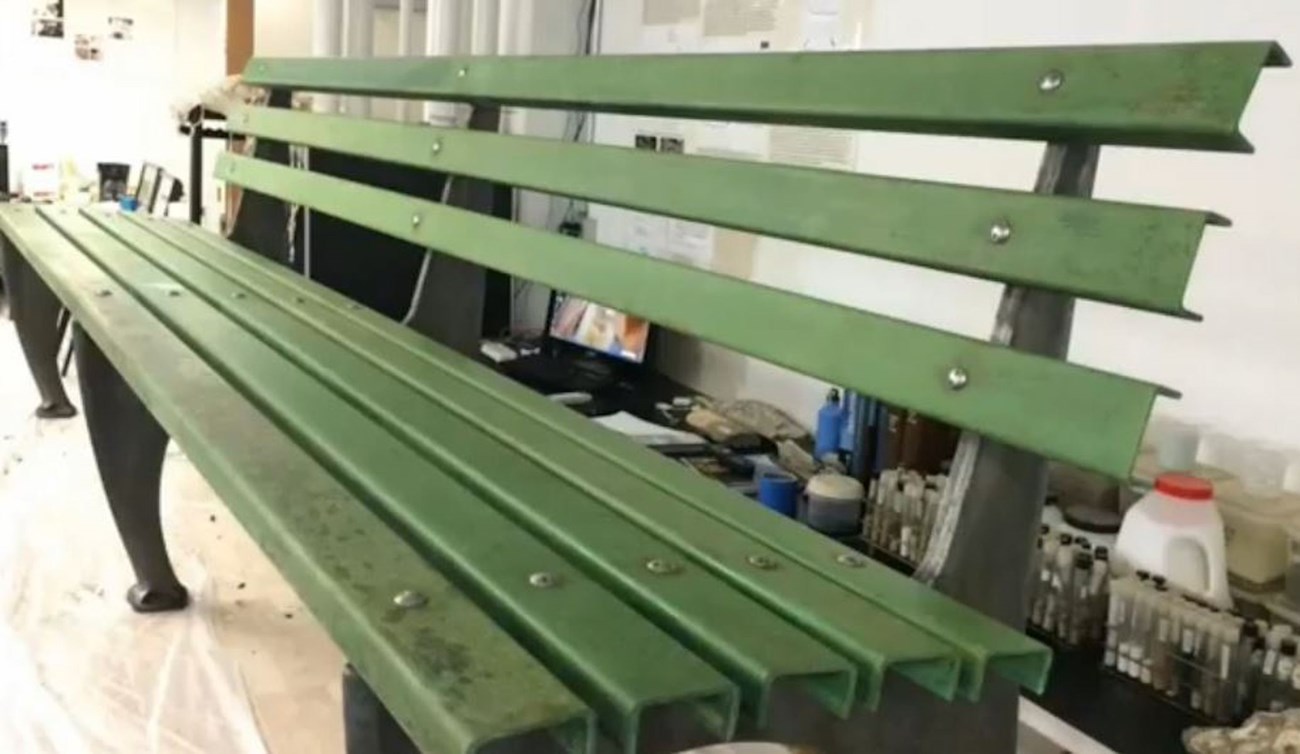
Gary Winogrand
Benches
This left with an easy maintenance for the museum on this that you basically had to use a damp rag or used a PH-neutral detergent, but you did have to continue to wax the legs on a regular basis. Repairing gel coats is not particularly easy, and is particularly bad if you don’t know the resin matrix. Because the students had already done this, they knew basically that there had to be a polyester resin. If you are fixing this kind of benches, it’s not very difficult. You just have to know how to treat it.
Essentially, scratches just get sanded out, but in this case, of course since somebody removed the gel coat, you would still put a gel coat back that was polyester resin. For gouges and deep scratches, you put a sympathetic filler in and then the gel coat over it. What is problematic about repairing these benches is how close the slats are to each other.
In addition to this, I said the students figured these benches had to be repainted, so in these repairs, you could do these repairs without having to match the color of the original benches.
Of course a marine grade primer and paint would have to be used. They did recommend matching the original color. Actually, to go back, one other thing they did recommend that if these benches had already lost their slats, rather than using wood slats, they should use fiberglass slat again, and they should and they should make up extra slats for the maintenance of these so that if the slats got broken, the park’s department could then just interchange new slats, and that if you had a bench with all new slats, this meant you wouldn’t have to paint it every five years, probably longer there in the parks, and therefore it will be a much more easier maintenance.
I’m going to go quickly into some other structures that we are looking at because fiberglass structures at the fair most, they were much more complicated than the bench, particularly the pavilions. And all that remained of the fiberglass pavilions at the fair are too small and celery structures.
As with all good projects, there was a team, and this was headed by Silman with Ed Meade at the head. Emmy Wang and Sylvester Black were assisting there and Jablonski Building Conservation with my colleague Brandy Hayes and myself was also part of the team. The three fiberglass pavilions were built at the Marina of the Fair which is right next to the water. They were part of an experimental application in the use of these materials.
Two other pavilions actually had similar products. One was the Seven-Up pavilion, which is a two-storey central structure here and 18 canopy modules. The other one was the West Virginia State Pavilion which actually had two FRP domes. The Marina pavilions were designed by the architectural from Peter Schladermundt, Associates and the engineering firm [stroborongoved 00:20:11]. The FRP panels were fabricated by Ray Greene … Remember that 1942-boat, his company.
Originally, we had known that most of the pavilions at the fair, the fiberglass had been fabricated by Owens-Corning. We found later a little booklet here. You will see one of those little pavilions showing up on their booklets so we know they had to have supplied the FRP. The marine pavilions were built with 12 FRP, prefabricated sandwich panels. They had joints at the four axis of symmetry, and the panels were connected with these little locks called Roto-lock connectors.
One of the things that made these pavilions was, you see this infill panel here, there were actually infilled with glass and aluminum and mullions which enclosed and supported the structures and then they were anchored right here in the corners down with steel into the foundations.
As with the benches, these pavilions were not originally painted. They had a colored, in this case, white gel coat. At the end of the fair, the structures were auctioned off. One private buyer bought one of these pavilions, disassembled it and moved it to the Adirondacks where it’s actually still in use.
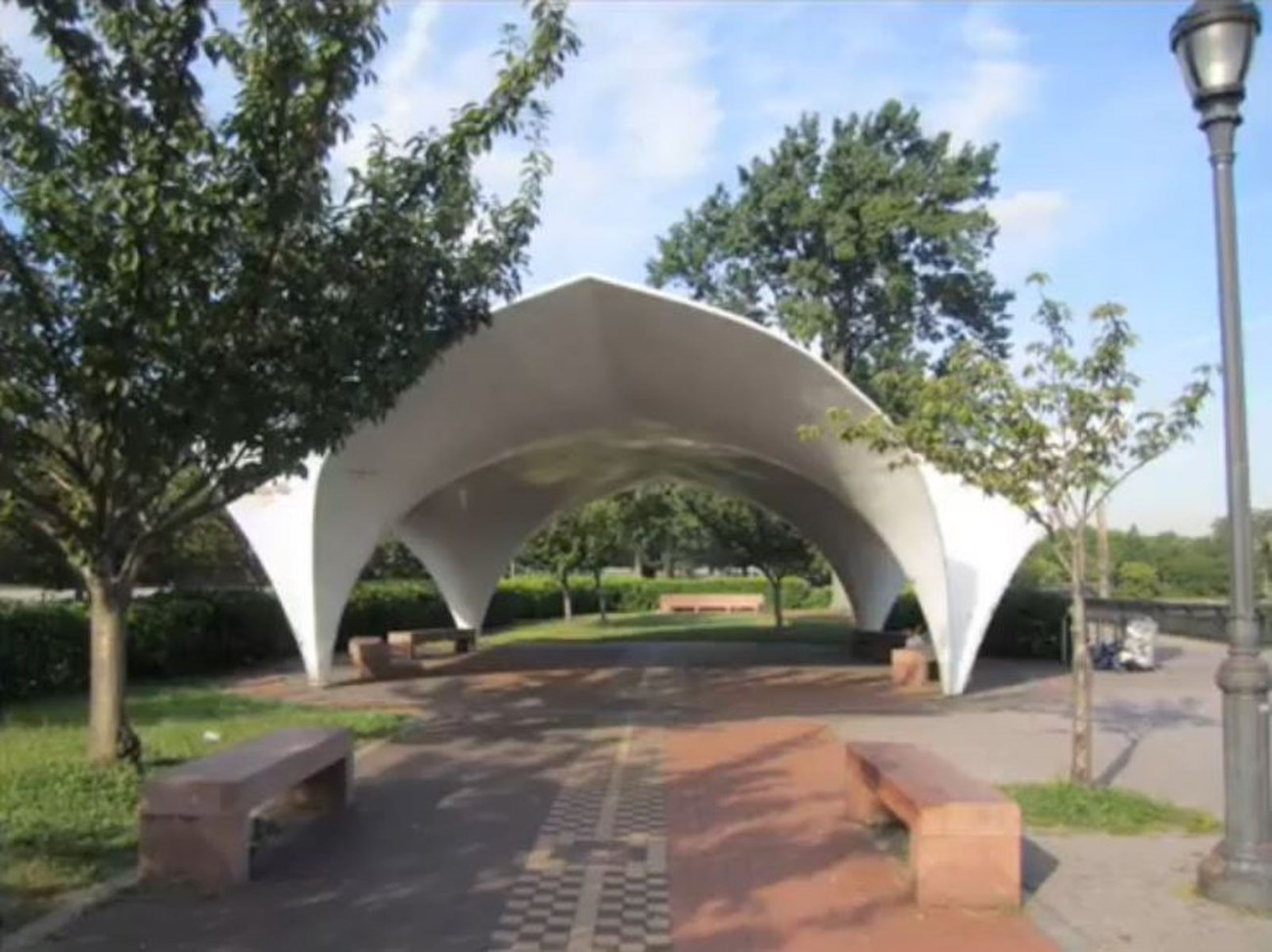
Gary Winogrand
World Fair Pavilion
A contractor purchased the two other pavilions, but what he did was he stripped out the glass and aluminum enclosures and took those. He didn’t think the FRP shells had any use. Just to take a quick look at what the construction is here. This is a sort of a not-to-scale sandwich construction intersection. You can see there is a top skin and there is a bottom skin, and in the layers of these pavilions, there is actually polyurethane film.
The blocks actually, it’s a one eighth inch skin and the film is two inches thick by four inches wide and they are preformed blocks. The interesting thing is in the other two pavilions they actually use honeycomb paper instead of polyurethane foam. Another interesting point was they used shear ties because nobody quite knew how this stuff works, so to tie these two skins together, they had the shear ties that you see here.
To hold these different panels together, we had this Roto-lock that was used on all of these FRP pavilions. They were on intervals of 12 inches on center for vertical joints and eight inches on center for horizontals.
The thing about it is that the center disk here was a nice copper alloy, and the rest of this lock was a ferrous metal.
Time, poor repairs and lack of understanding of how to maintain FRP structures and of construction has taken a significant toll actually on these pavilions. The actual material issues with the FRP are very similar to those found on the fiberglass benches. They are compounded by major structural issues.
Silman Associates undertook the structural analysis. If I make a mistake here, I take full responsibility for it as I’m interpreting this. The FRP deteriorates from movement and thermal stresses. One of the things is, in sandwich construction, what can happen is you can get air in the middle between these skins, and when you do, it heats up, you can expand and contract and it causes rippling of the skins.
So after the two-year mark at the Fair, when they started to disassemble these pavilions, they actually did an analysis on all three types of pavilions, the Seven-Up, the West Virginia State, and these three. What they found was the Seven-Up and the West Virginia pavilions actually were actually severely deteriorated.
What happened is the paper honeycombed center actually had actually caused delamination of the skins from the core. However, the marine pavilions were just fine.
What’s happened since they’ve moved the structural support of the infill panels of the glass and aluminum out, the wind loads, as you start heavy storms and heavy winds, have actually caused these pavilions to move extensively and you get the kind of cracking that you see here.
The other point of this cracking here is you can see where the Fair is middle of the corrosion staining coming pout of the joint. The other thing you get, you get snow loads which have been significant, I think. We already heard from Nancy about problems with foundation here. So there are sort of settlements in here which has also caused some cracking. This is not the only problem. We have impact damage.
The most severe damage was caused when a car hit one column leg. You can see the crack at that joint is quite large. There is also the problem that people have been climbing up the pavilions, skate-boarding on top of the pavilions, riding the bikes up the legs, kicking soccer balls on the interior.
Here is a case where somebody probably was on the skate board and fell. You can where the elbows come down. They were quite lucky they didn’t fall down. To top this off, because don’t understand about how to treat FRP, here is a contractor that came in to paint it, and what he did was he took the gel coat off.
They sanded it completely down. You could see white is completely lost where the brown is. I’m sure the gel coat had its problems with cracks. It was discolored, but I think they just didn’t understand what the purpose of that was. We’ve also got the fact that we’ve also got the fact that we have embedded steel in these legs.
What happens is when these joints open and they crack due to thermal movement or wind movement, we get water infiltration which leads to corrosion of the steel, which leads to widening of the crack joints, and on and on and on. You could see that there is significant paint loss at the top of the pavilions, and because it sits on the gel coat, this matters. This is what is protecting the fiber mat.
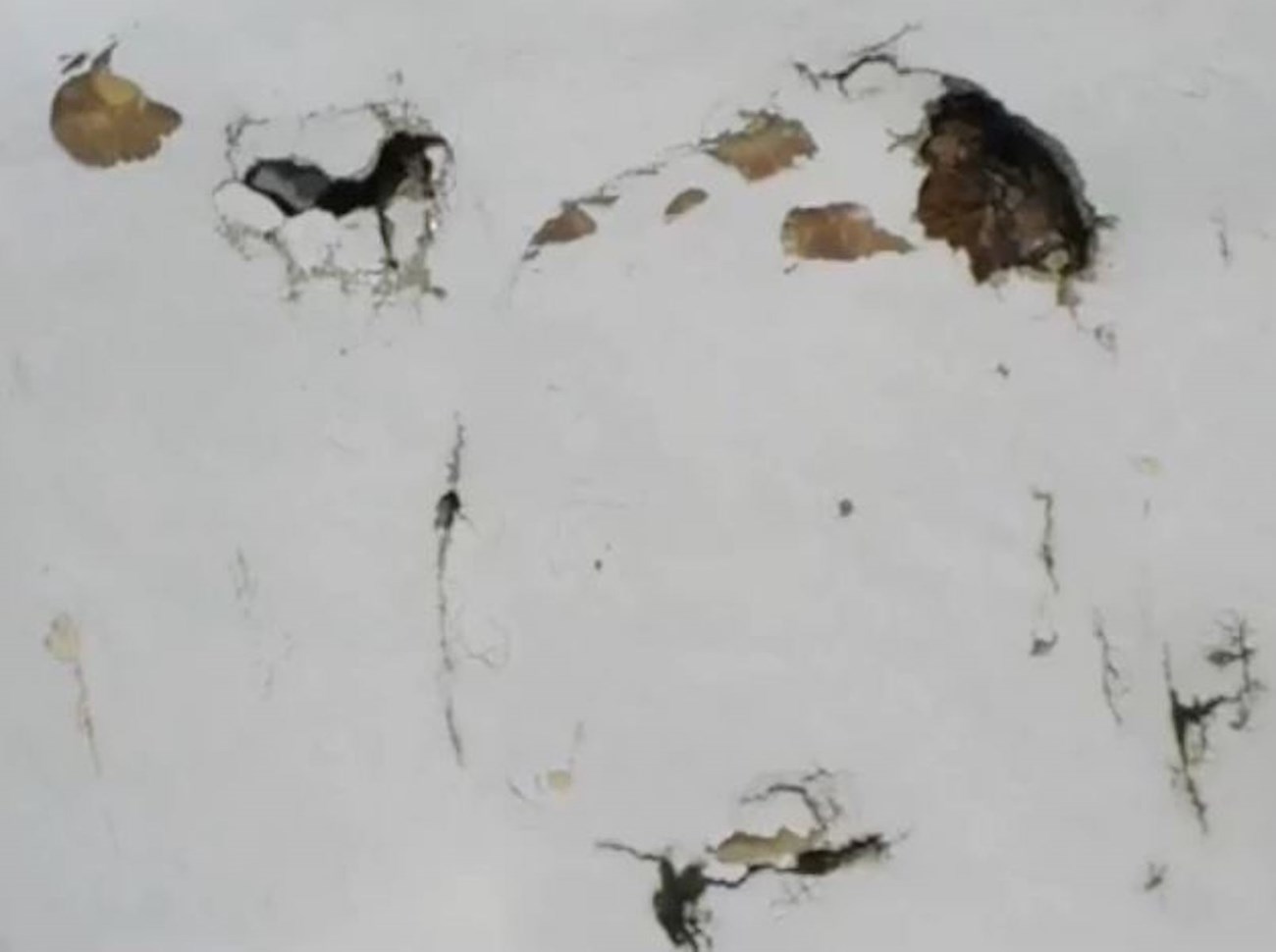
Gary Winogrand
Impact Damage
What’s interesting is the fiberglass bloom on this pavilion is not actually particularly bad. I think it’s because what they did is they embedded the mat into a resin quite thoroughly. We also have bio-degradation of this thing.
One of the worst of it is where water gets trapped in the panels and in the foam and it offers excellent breeding ground for things like the moss that you see here. If it was a matter of solely repairing the FRP, there would be a number of options here and most of the repairs would be relatively simple. With the exception of how to deal with the film in the few areas where we actually have these open joints which expose the foam, but unfortunately it’s the structural issues, I think, that are going to be one of the factors that defines how these are treated.
The removal of that window system has caused a major problem. The leg where the car hit is actually quite unstable, but in the end it’s probably going to be the deterioration of the Roto-lock that’s going to be defining most of all how these are repaired.
If these are the locks that are holding these panels together, because they’ve completely deteriorated on the fairest portion of this that essentially they are going to have to …
One of the things is that although these four pavilions have been mistreated and not particularly well taken care of, you can see what happens when something is.
This is the Adirondack Pavilion here. These things can be repaired, but I just want to point out that these had to have been inspiration here there was a magazine article about 12 addition FRP houses that were built by a company in Connecticut. Three of them are in Southbury, Tolland and Bristol.
Have not been able to locate them, but somewhere out there, there have to be at least one surviving house that we can all go and take a look at. Finally, plastics and fiberglass are everywhere, so are inappropriate repairs. Let’s not lose an important component of a mid-century modern material.
Abstract
The 1964 World’s Fair presented itself as “A Millennium of Progress” and viewed part of its mission as creating a venue for companies and businesses to unveil their products of the future. The makers of fiberglass reinforced plastic (FRP) made sure they were at the forefront of this Fair.
For the fair designers and fiberglass industry, fiberglass reinforce plastic was the perfect material for its temporary construction. It is a strong lightweight material that is relatively cheap and readily molded into complex shapes. At least one million pounds of the FRP was used to make pavilions, a Ferris wheel, life sized dinosaurs and benches. Two small pavilions and approximately 2 dozen benches remain at the Fair site.
A product developed during the war, FRP was used in many exhibitions after the war to show the merits of using plastics in building construction.
In the late 1940s, FRP sheets began to be used in the construction industry as wall panels or roofing panels due to the panels’ ability to be colored and transmit light. By the 1950s FRP was being used as cladding for buildings with steel or concrete frames, roofing trim, plastic forms for concrete, and gutters and flashing. Benches at the World’s Fair used FRP slats.
Another construction technique first used in the 1940s was fiberglass sandwich construction that began use as covers for radar equipment. For this sandwich, FRP skins were laminated over a core material, typically honeycomb paper or urethane foam. Several pavilions were made using this technique at the 1964 World’s Fair. Although three survived, only two remain at their original location.
At the time of the 1964 World’s Fair, FRP was innovative but viewed as ephemeral. Little thought was given to how to maintain or even preserve any of the FRP structures or infrastructure. This created a problem when the benches and pavilions were handed over to the New York City Department of Parks. Weather, inappropriate maintenance, and impact damage have taken their toll on the FRP.
The few remaining elements require significant conservation. Schematic preservation strategies have been developed by the engineering firm, Silman Associates and architectural conservation firm, Jablonski Building Conservation for one of the FRP sandwich shell pavilions.
Students in the Fall 2014 Conservation Workshop at Columbia University’s Historic Preservation Program conserved one of the FRP benches and devised repair strategies for the maintenance of the remaining 1964 World’s Fair Benches. None of the solutions for either project were perfect. This presentation will discuss issues with conserving FRP and the hard choices that need to be made.
Speaker Biography
Mary Jablonski runs one of the country’s best known architectural conservation firms, Jablonski Building Conservation. Mary has worked as an architectural conservator in the New York area for over 20 years, and has taught short courses nationwide through her affiliation with APT, the Campbell Center for Historic Preservation and NYU.
She began teaching in the Historic Preservation program in 2002 and has taught both the Conservation Workshop and American Finishes classes.
Jablonski received her Masters of Science in Historic Preservation from Columbia University in 1990; held a Kresge Fellowship for study at ICCROM, Rome Italy; and has degrees in Modern English Social History, from the University of Sussex, Brighton, UK; and History from the University of Massachusetts, Amherst.
This presentation is part of the Mid-Century Modern Structures: Materials and Preservation Symposium, April 14-16, 2015, St. Louis, Missouri. Visit the National Center for Preservation Technology and Training to learn more about topics in preservation technology.