Last updated: April 7, 2025
Article
Podcast 042: John Asmus on Laser Cleaning "Have Laser Will Travel"
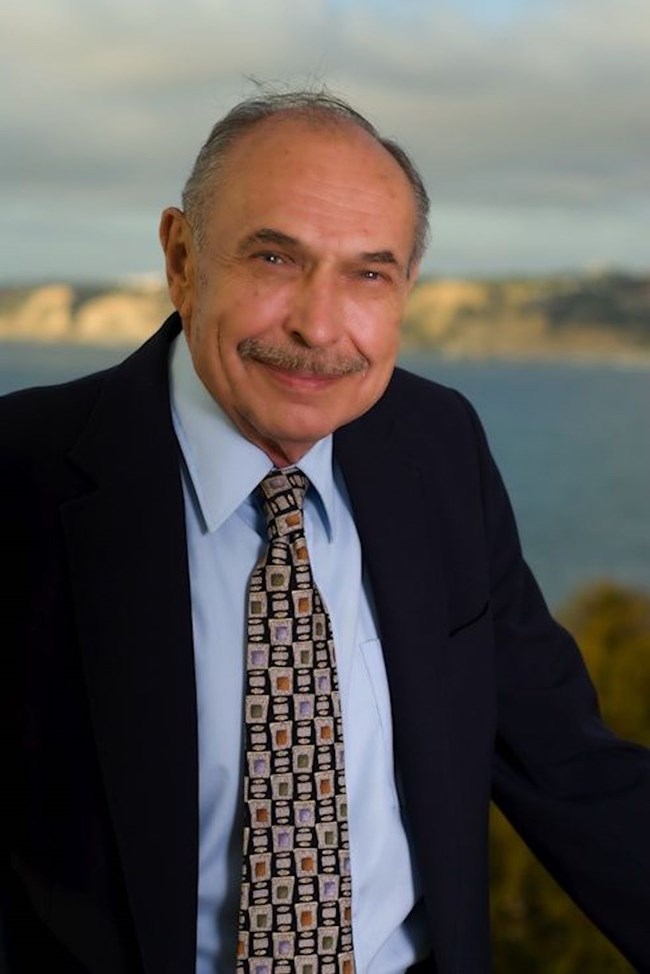
University of California, San Diego
Grandfather of Laser Cleaning
Jason Church: My name is Jason Church, Materials Conservator with the National Center for Preservation Technology and Training and today, I’m here talking with Dr. John Asmus. Dr. Asmus I was actually introduced to you at a LACONA Conference by Meg Abraham. She was explaining to me that you’re one of forerunners and she called you the father of laser cleaning. So what can you tell us about that?
John Asmus: Well for recent years, actually they’ve been calling me the grandfather. We tend to think of Costas Fotakis, the Director Forth and Crete as the father because around 1990, he developed a very active program in laser treatment of artworks and he got LACONA going.
John Asmus: I suppose the major thing I could say at that point was that most of the people who were doing treatment of artifacts with lasers at that time, thought that I had died twenty years earlier. In fact, it was Meg Abraham that said, “Why don’t you invite John to these things because he’s still around and he’s still active,” and so that’s how I got involved in the LACONA organization. I had long since moved into a number of different fields.
John Asmus: I did my first work on artistic materials using laser radiation in 1972 and it seems rather bizarre to me in retrospect, but several of us who were involved in the early projects in Venice and in Florence and so forth, as we usually do after performing some research, we wrote up manuscripts and we sent them off to the appropriate journal which in this case was Studies in Conservation.
John Asmus: The editor of Studies in Conservation refused to even review our manuscripts and it’s impressed in my memory the letter of rejection that we received for several papers and the most succinct line that I recall is that “cleaning with lasers is so hypothetical as to not be taken seriously.” So I thought if that’s the way the community is going to respond to this, we’ll move on to other fields. So we adapted our laser divestment techniques to taking the paint off airplanes and more recently the paint off stealth aircraft which is a tremendously challenging application because you’re essentially taking epoxy paints off of epoxy composite substructures, which is a major problem in selectivity, far more complex than most of the things we find in the arts.
Galileo's office & Cremona Cathedral
John Asmus: So we had been moving in those directions and then there were a couple of true believers in the viability of laser treatment of artworks. One of these was an art conservator for many years. He was chief conservator of sculpture in Venice and then he moved onto private practice in Padua and his name is John Carlo Calconyo and oh, every year or two, I’d get a call from John Carlo saying, “I’ve run into this terrible problem where we can’t get adequate divestment of something or another.” So I’d pack up one of the lasers from our laboratory and we’d go and work on Galileo’s office, the Cremona Cathedral, and other places and gradually the word spread.
John Asmus: I think after about twenty years, quite a number of art conservators and scientists who were interested in applying lasers to the arts, came to be familiar with this, and I think that culminated then around 1990 when Costas organized the first International Conference On Lasers In Art, which was subsequently renamed LACONA 1. It took place in Crete and it’s been going on from there. For a number of years, people referred to Costas as the father of laser art conservation. Somebody had pointed out that I had done it twenty years earlier and so they christened me the grandfather of lasers in art conservation.
First Object Cleaned by Laser
Jason Church: Now what was the first thing that you ever cleaned with a laser and when was it?
John Asmus: Well, there’s a curious anecdote that has to do with all of this. We were in Venice making holograms thinking that when Venice was gone, at least we’d have these very high resolution three dimensional images of the Venice that used to be. And we were making holograms of some important sculptural pieces in Venice and one of these works, which was the polychrome wood carving of Saint John the Baptist by Donatello, we found that where the people in the gallery placed it when the Sirocco winds came up, rain started coming through the windows and rainwater was splashing on this priceless polychrome wood carving.
Giulia Musumeci, UNESCO and the Venice Imperil Fund
John Asmus: So we called the conservator, what should we do? She came in and she covered the wood carving with plastic and then she said, “I really respect what you’re doing about saving the images of artworks, but why don’t you help me save the artworks themselves, the statues, the marble statues that were deteriorating.
John Asmus: Her name was Giulia Musumeci and she was employed by UNESCO and the Venice Imperil Fund, and she was trying to do what she could to save these marble statues of Venice. She pointed out to us that cleaning the statues was a major technological challenge. So she asked us if we would try our holographic laser on removing the crust from stone and everyone was amazed at how beautifully this worked. We had reinvented the laser eraser. The encrustation, the sulfates in Venice is black and it absorbs laser light and if you do it with short pulses you can cause the black encrustation to sublime and if that happens very rapidly there’s little if any heat that’s transferred to the stone itself. It worked perfectly.
John Asmus: So Giulia Musumeci located her mentor, Kenneth Heppell of the Victoria & Albert Museum, who was Sir Ashley Clark’s point man for saving Venice and it’s artworks. Ken Hepple was told about these initial results and he came over and we spent a day shooting different pieces of dirty stone that he had in his pocket. One pulse here, two pulses there, white stone, Portland limestone, istrian stone and so forth and at the end of the day he said, “This is the most spectacular advance in stone cleaning that I’ve seen in my lifetime.” We said “that’s great,” and we went back home to America and then we started receiving airmail packages and this is the answer to your question Jason.
John Asmus: He would send us airmail monument stones from abandoned cemeteries in London. So we spent the first year back from Venice cleaning limestone, oolite, and other things from abandoned cemeteries in London and then airmailing them back to Ken Heppell. Then he started sending us pieces of cathedrals and I suppose the direct answer to your question Jason, is that he then began sending us some elements from the sculptural decorations on Wells Cathedral. These elements were all of oolite which is a very poorly consolidated limestone and it presents some unique problems in trying to clean it without damaging it. So we cleaned several elements from Wells Cathedral.
Sarcophagus of Erard de la Mark
John Asmus: Then we were invited to the Royal Institute of Artistic Patrimony in Brussels. Rene Schnaers had heard about our work in Venice and he had us clean a sarcophagus that housed the remains of Erard de la Mark. This sarcophagus had been damaged during the French revolution. It hadn’t been properly cared for after that and so there was a great deal of external deterioration of that sarcophagus and I suppose strictly speaking, that sarcophagus, which I think was brought into Brussels from Liege, was the first major artifact that we used the laser on. From there, a month or so later, we went to Munich with our laser and Dr. Vokernaugle brought out a number of iron sculptures that had supposedly been the first major iron statues or sculptures created in northern Europe and we took what amounted to rust and corrosion off those iron sculptures. So I suppose those were the second things we had used lasers on that was actually useful and accomplished some conservation.
John Asmus: The first major project where lasers played a big role in major conservation efforts was in the city of Cremona, which of course is famous for stratovarian, guinarian , all the stringed instrument makers. In Cremona we did major parts of the facade of the Cremona Cathedral including marble reliefs of the four prophets at the front door, Isaiah and the others, and that was in 1989 and 1990. At that point we were cleaning many square meters of marble surfaces of intricate detail and that’s about the time that Costas Fotakis picked up this technology and really went with it.
Jason Church: Now what kind of laser were you using?
John Asmus: Well when we started our work, you didn’t have very much choice. In 1970, 1971 and 1972, there were really two major laser types that produced high powers in short pulses and these were neodymium glass lasers and ruby lasers. So the only way you could make pulse holography in 1970, 1971, 1972 was with a ruby laser because it’s wavelength matched the spectra responses spectroscopic photographic plates, the one used in holography.
Ruby Lasers to Neodymium YAG
John Asmus: So we started out with a ruby laser and it was more suitable than neodymium glass lasers because glass has a poor thermal conductivity and you can’t really have a very high average power because you have to wait for the glass to cool down between pulses. So in the early seventies, there was really no choice other than ruby.
John Asmus: Now Neodymium YAG had been invented and had been turned into lasers but in the early seventies, neodymium glass rods were very problematical in trying to grow them to large sizes. Just about the time we were doing our work in Venice, the Lynton Corporation succeeded in making larger high quality Neodymium YAG rods. So those became available in 1973, 1974 and so I think by 1975, everyone was switching to Neodymium YAG because it existed.
John Asmus: So I believe after about 1975, we and then all of our successors in this field, pretty much universally went to Neodymium YAG. Of course, in subsequent decades there have been a number of other lasers that have been developed that give you options for other wavelengths and of course the harmonic crystals for turning YAG infrared wavelengths into green and near ultraviolet have become available. So the stable of available lasers has broadened considerably.
Excimer Laser with Krypton Flouride and Xenon Flouride
John Asmus: At one time a very interesting laser type that emerged was the excimer laser using krypton fluoride and xenon fluoride. There was a period where we did quite a bit of laboratory investigation of using those types of lasers on artworks and it looked very promising, I suppose around 1980. But those lasers, those excimer lasers used gases and they’re complex and present reliability problems, at least then and about that time, picosecond and femtosecond lasers from a number of the solid state posts became available and I think those extremely short pulse lasers, picosecond and femtosecond have been so successful on some of the very fragile materials.
Dye Lasers
John Asmus: But I am not aware of anybody who’s proceeded with the excimer lasers to see what they can do. So I think between the standard Q-switched neodymium YAG lasers and the harmonic generation from those and a few of the offshoots is pretty much the range of lasers that you find using. Dye lasers hypothetically offer some possibilities because they’re so widely tunable but the dye lasers haven’t been that successful commercially at least to this point so I haven’t seen much activity with dye lasers.
Jason Church: Sounds fascinating. I’ll look forward to it. Thank you for talking to us today Dr. Asmus. We hope to talk to you more in the future. Of course, you’ve given a great keynote here at the 2012 3D Digital Documentation Summit. We look forward to hearing more from you in the future.
John Asmus: Well thanks, Jason and it’s been fun. I’ve met a whole new cast of characters associated with allied fields so I’ve made many friends, and I think maybe I’ve helped a little bit in exposing them to some of the experiences I’ve had over the last sixty years of this phase of my career.
Read other Preservation Technology Podcast articles or learn more about the National Center for Preservation Technology and Training.