Last updated: June 12, 2024
Article
Conserving Salvaged Military Maritime Objects
This is a transcript of a presentation at the Preserving U.S. Military Heritage: World War II to the Cold War, June 4-6, 2019, held in Fredericksburg, TX. Watch a non-audio described version of the presentation on YouTube.
The MARAD Collection - Conserving Salvaged Military Objects
Presenter: Josephina Maldonado
Abstract
Conservation Solutions, a division of EverGreene Architectural Arts (EverGreene), has been leading a multi-year project for the assessment and treatments for a collection of over 1500 artifacts, for the Department of Transportation, Maritime Administration (MARAD). The collection is comprised of artifacts coming from predominantly Victory Ships, circa 1940s, which includes clocks, chronometers, barometers, nautical instruments, and hardware such as ship’s bells, steering wheels, and engine order telegraphs. As part of the mandate of the MARAD organization, the collection underwent conservation to clean, stabilize, and repair the collection for future display.Historic use and storage over time varied from artifacts’ conditions such that the procedures to treat the objects also varied based on the type of object. The collection is comprised various materials such as finished and unfinished brass, glass, aluminum, plastic, wood, and other materials. Conditions varied on the artifacts that included failing lead paint, serious metal corrosion, and objects coated with industrial grime. Before any treatments, a team of EverGreene conservators and technicians conducted tests and mock-ups of the different execution strategies throughout the duration of the project. Conservation treatments were divided into the following categories: dry cleaning, wet cleaning, corrosion reduction, lead paint abatement, repairs, and coating applications.
A continual delivery and pick-up schedule by object group was developed to meet project milestones within the allotted time frame. The artifacts were transported from the Naval warehouses at Cheatham Annex, in Williamsburg, VA to EverGreene’s studio in District Heights, Maryland. The Maritime Administration was consulted throughout the life of the project to ensure that all treatments were to the specification of the scope of work to ensure preservation of the collection.
This paper will explore the historical context of these objects to provide perspective for the object’s conditions. We will also review the extensive documentation, transportation plans, and treatment program carried out by EverGreene staff between 2016-2019.
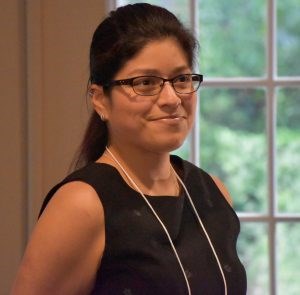
Presentation
Josephina Maldonado: So good morning everyone. My name is Josephina Maldonado. I am a senior conservation tech with Conservation Solutions, a division of Evergreen Architectural Arts. So I'll be referring to them as Evergreen from this point forward and I know I am between you and your lunch. So when I see the angry looks, I'm going to work through the presentation as quick as I can. So you'll notice the QR code on this slide. If you'd like to learn more about what services Evergreen provides or what projects Evergreen has worked on, this will take you directly, but if your phone is not capable of that, you can just go to www.Evergreen.com.
So in 2016 Evergreen was awarded a two-year contract with the Maritime Administration to clean, stabilize, and repair a collection of artifacts from historic merchant vessels. So in today's presentation I will discuss with you highlights from the project including the scope of work.
There are 1,574 artifacts. So as you can imagine, there were many challenges, logistical and coordination. We had issues with project managers, staff turnover, health and safety concerns, and at the very end of the presentation, I will go over the treatment of one of the most numerous artifact groups that we have. So as part of the Department of Transportation, the Maritime Administration's History Program is responsible for the historic preservation of a collection of historical value artifacts removed from merchant vessels. So the QR code on this slide will take you to a MARAD's historic program. In 2015 the collection was relocated to a secure storage facility at the Naval Weapons Station Yorktown/Cheatham Annex. Prior to that, the artifacts were in, I believe they were in, what does it say here, in shipping containers, excuse me, at Beaumont. And unfortunately 70% of the collection was downsized, so I can't speak on behalf of those items that we never saw, but of what remains, that's the collection that we got to work on with Evergreen.
An independent collection assessment in 2016 was conducted to determine overall baseline condition for the artifacts. So their ranking system ranged from excellent to very poor. At the Naval Weapons Station, the artifacts are stored in two areas within the warehouse. The first areas, excuse me, the first artifacts that we dealt with were from the areas that were not in a climate control setting. Later on, as the project continued we got to work on areas, excuse me, artifacts, which were in an area that did have climate control.
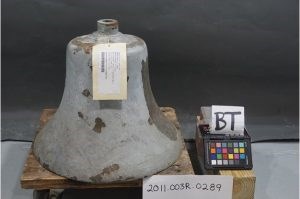
I'm going to move to the next. So as you can see on this slide here, we do list some of the materials that we had to deal with. At no point did we have one object group that just only had one type of material. So as we were doing treatments, we did have to consider all the varying materials as we were trying to decide the, not just the conservation treatment, but also recommendations for storage later on once we returned the artifacts. In this image here you can see the interior of the warehouse. This warehouse also holds, excuse me, what is it, housing for parts of the MARAD's ready reserve warships. So in this area, as you can see the heavier artifacts, which in this image, you see ships bells and what looks like a very tiny cannon on the top. That's a Lyle gun. Those were all on the metal racks and everything else in behind is what you see from the ready reserve ships.
This image here is what I call the artifact room. This was the room that was designed to hold these artifacts in climate controlled and security controlled areas. In the other warehouse area, anyone could enter. Anyone who's a staff member, but at this point only the MARAD staff could enter. So as you can see here, we have wooden crates and wooden bins. Most of these were built by MARAD. They had contractors build these items. So these were the artifacts that we had to transport as they were. Towards the very back and also off to the sides, I'm afraid you can't see very well, were tri-wall boxes, which held life ring buoys, ship's wheels at times ones that they use to guide the ships. But otherwise, in the wooden bins, we have builders plates and in the crates, which are designed for the tall artifacts such as binnacles, gyroscopes, engine order telegraphs.
The condition assessment in 2016 did a baseline, as I mentioned, for the entire artifact groups. However, when Evergreen was starting to do their assessment, we had to indicate some of the specific items that were not addressed in the assessment. So on the first image that you see here, we have the lifting and the flaking off of the painted layer. So the team had to use a proper adhesive to consolidate the painted layer. And this next image here, you see the removal of stickers, tapes and labels. We did have to use mechanical, dry and also wet-based methods to remove all of these, but to preserve the painted layer. In this image here, you're seeing the removal of ink-based markings. A lot of it, this was not on wood, but a lot of the times we saw the ink on the painted surfaces. We saw the ink on the bare metal. So we did have to use, if possible, dry methods, mechanical methods, but mostly solvents to remove the ink.
This is a fire ax, so you can see the corrosion on the fire ax. And in one instance, there were only two of these, the corrosion was so severe that it was actually falling off of the wooden handle. So when we returned it to the client, we did have to put it in special housing to keep them together, but otherwise to mitigate this corrosion we did have to use tannic converters. For the copper corrosion, as you can see here, I'm sorry the image is a bit blurry, we did have to use mechanical methods and also wet methods to remove it.
The life ring buoys were the only object group that had mold. And to mitigate the mold we did have to use dry methods and also wet methods. Now this picture shows lubricants, excessive lubricants that we're covering most of the artifacts, some of the other artifacts had these same lubricants in their interiors. So we did have to oftentimes open up the artifacts, and I'm referring to binnacles, I'm referring to the gyroscopes, the engine order telegraphs. When possible, we did open them up and tried to clean out the excessive lubricant, but oftentimes not just excessive, just the removal of it because the lubricant is a fire hazard if left in their storage collection.
We used a proper conservation adhesive to repair glass. And not just glass, but there are also plastic almost glass-like elements that were broken faces that we did have to repair as well. And in some of the artifacts, the nautical instruments that came in wooden cases, we did have to repair the cases themselves. Oftentimes as is in this image, they were disjointed, but we also had some where the baseboards were completely detached and other detached areas as well. And these ships bells were the only object group in which the client did ask us to remove unassociated parts. So in this picture here you see our technician using a portable band saw to remove excess metal from the headstock of a ship's belt.
So in this image here we see binnacles, which have fallen over in a moving truck. Now I'm happy to say this was not me. This did not happen under my watch. Otherwise I would be ashamed to show you this photo. However, this is an indicator of problems that occurred during the project. This is the most dramatic photo. So luckily we don't have any that are just as bad. But in treating 1500 artifacts in two years, we had a lot of logistical and coordination concerns, packing and shipping, and probably the most important, which is the tracking and inventory system.
So when I took over, there were a lot of moving parts. As the lead technician... I started about nine to 12 months after the project had started. And within that time there was a turnover in project managers. And unfortunately the handoff of the project was basically non-existent. So with regards to project materials, the project manager who I started with, I saw they had a binder. But when I had to take over, we couldn't find that binder. We don't know where all that information went to. If they just took it home with them to their new job or they burned it, threw it away for all we knew.
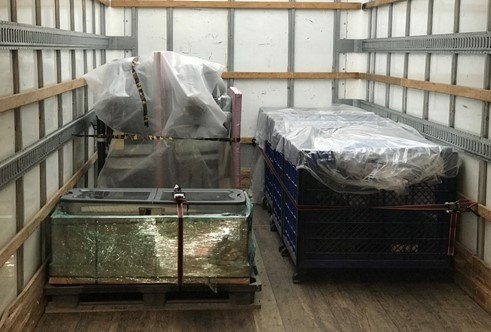
The tracking system. When I started, the owners of the company asked me how many artifacts have been treated? I had to thumb through a separate binder to manually count how many items had been treated and even then a lot of the paperwork was hard to read. There was no electronic system. So Evergreen does keep a cloud based storage system and you would think, "Oh well maybe since we can't find any paper-based evidence, we can go online and try to see what's up there." We couldn't find anything that was of any value. So apparently the project managers were just maybe setting up their own system, and then the next person that came in wanted to set up their own system. But at the end we couldn't find any of that information.
And in the meantime, who was communicating with the client? While all these changes were happening, did anyone contact the client? Did the project managers themselves say, "Hey, I will no longer be with this project. So for any more information, please contact so-and-so." And I will tell you right now that didn't happen. And when I took over again, I was the lead technician, so our project manager was based in Canada. So at no point did I ever meet this poor female. We had to communicate with pictures and cell phones and emails as I'm trying to relay, "Hey this is the corrosion that we see, but it's unusual. How would you handle it?" And then they would just email right back. So at the end, I would say it took us about a month before we could have a baseline of where things were and what to be done so that we can continue forward.
So as the lead technician, I had to be sure that all of the staff were filling out daily treatment reports. Now, these reports were still written by hand, but then they would feed into an excel spreadsheet, which I'll refer to later on. Since I was the one who was assigning the tasks, I was also the one responsible for training the staff. Now the senior conservators developed the protocols, but I had to write out the protocols, so in the event that if I was to leave, someone else could continue onward and they wouldn't have to start from scratch again. But being as that since I was training the staff, I was also the one that had to ensure that there was a uniform consistency in the treatment that was done. And I had to decide when an artifact treatment was complete or if like, "Hey, come back, let's look at this area or let me contact the senior conservator, we have an issue here that needs to be addressed.
I was also in contact with the client to establish a pickup and delivery schedule. At no point were we ever going to have 1500 artifacts in our studio. We just didn't have the space. And although some of the items were small, a lot of them were really big. You can see the bell at the very bottom right corner of this image. So usually three or four of those bells would fit on a pallet, and we could only fit two pallets on a rack, and we had about 64 bells. So that right there, using moving trucks would have required us to at least have three moving trucks. So we were not going to have a convoy going up and down the highway between our office and studio in Maryland down to Virginia to go pick them up and to return them.
So it did require a lot of planning ahead, "Hey, we'll take this number from this number, from this specific object group, then we'll take this number from this other type of object group." And I forgot to mention that we had at the end 26 object groups. I won't list all 26 of them, but when I say object groups, I mean the name of the artifacts. So if I say we had ships bells, there were 64 of those. If I say we had name boards, we had about 32 of those. Later on when those booklets, those post scripts, I believe that were, there will be a table listing out all of the exact numbers of the different object groups.
And now we're moving to documentation. So our studio did not have a dedicated photo studio. At one point, depending on the different projects that we were working on, we had to Mcgyver a photo studio using tarps, using clamps, using black plastic just to try to get professional-looking photos that we would have to submit to the client, both before treatment photos and after treatment photos. Of course we did take some during treatment photos, but those were mostly for our own documentation purposes and to explain treatment procedures to the client.
And at the very bottom we see the reporting. So I had to submit weekly reports to the company managers, which then fed into the monthly reports that I would submit to the client. And in those monthly reports to the clients, I had to indicate what was the work completed, the previous work that had been completed, the projected work for the following month, lists of issues and constraints and any modifications to our delivering pickup system. Now the 2016 condition assessment survey indicated that there was lead-based paint system and asbestos in the collection. So to test for lead paint, we used the commercially available 3M lead check swabs. That's the image you see right there.
As you can see, it's red, so if there's red there's lead, that's their logo. We tested the first sets of object groups that we brought to the studio, any that had paint on the surface, and by the end of the project we just had to assume that all of the artifacts had some amount of lead paint because it they were always red, the swabs are always red. Now, as you can see in this other image here, the lubricants, again, I'd mentioned that those are potential fire hazards if left in collections and not dealt with the in a safe and efficient manner. You can see in that image that there are just chunks of that lubricant that was covering that ship's wheel. And in this image here we're seeing our technician fully covered, not just for the lead paint ‘cause she's working on a builder's plate, but more for the asbestos.
So our staff at all times had to use gloves. They had to use proper respirators, safety glasses because we didn't know what we were going to find. But also with the concern of as best as we wanted to be sure that we weren't going to put our staff in danger. However, by the end of the project we weren't able to confirm if there was asbestos. But possibly the most important thing was when we would return the artifacts back to the client, there was going to be the concern of later on in the future who was going to be handling those artifacts. So one of the other scopes of the project was to make sure that any health hazards would be mitigated under our watch.
So the packing and shipping. In this image here you can see that we had to rent standard moving trucks to transport the artifacts. Overall, we made about nine trips in both the delivery and the pickup. From the lessons learned slide where you saw the binnacles all tousled and turned, it was obvious that not everyone knew how to properly secure artifacts for transport. Now I came from the Air and Space as a contractor in their offsite storage, so I had some knowledge, but really as the lead technician, I did have to sometimes wrangle the senior conservators and say, "We need a proper training. We need to teach staff how to use a pallet jack, how to use a forklift and who's authorized to use the forklift, how to use ratchet straps. If we're going to secure items, how do we properly secure them inside a moving truck." Now, Evergreen purchased bulk containers which were on wheels and were stackable. So that's the one you see at this bottom image here.
In addition to polyethylene, polystyrene foams to move mostly the smaller nautical instruments, what we would do is individually wrap each of these small artifacts in polyethylene foam and then they would be again encased in bubble wrap placed inside plastic containers and as you can see here, then the plastic containers would be placed inside these larger crates. In addition to polyethylene, we use polystyrene foams to act as barriers, and those are the pink foam that you see in between the barrier. You can get those at Home Depot. But to prevent vibrations during transport and to also prevent any crushing of the objects as we're trying to squeeze them and pack them tight, you didn't want to start crushing things. So we also had to use a, what's it called, a polyurethane foam. It's usually a gun foam to put your guns on display. So those were mostly for shock absorption. But at the end on the picture you see on the right side to the top, those items would be covered. We covered them with plastic in the event that the moving truck had leaks when it was raining or during the time of winter, if there was snow.
You can see the on the top left picture, the gal is using wooden blocks to secure the bottoms of these binnacles onto pallets. So these were artifacts that were not already on crates. I don't believe these were the same ones that were tousled in the moving truck that we saw in the previous picture. But when we received individual items, we did our best to return them in a much better condition than how we received them. And we had to use, as you can see, ratchet straps and the foam to be sure that the ratchet straps wouldn't cause any surface damaged.
So with the complexity of this project in the top bubble, we had to create an excel spreadsheet that had all the information that you can read on there. So the client information that they provided to us, the name of the object, the object number, materials made, their condition assessment rating. And then we had to include our own data points for our own records such as dates of pickup, inventory, photography, when were they delivered? The project manager created the spreadsheet and it was maintained by the technicians. And all of the information from the daily report forms were uploaded into this excel spreadsheet. Now any of the technicians were allowed to do so, but eventually when you have about 20 people working on it, it was best to just keep it to one person and that was me, so I had to manually input everyone's sloppy handwriting into the excel spreadsheet.
Then on the bubble that you see on the bottom on the same spreadsheet but on a different tab, those are the numbers that counted. Those are the numbers that the company managers wanted to see and also the numbers that the client wanted to see. What percentage of the artifact group was complete? What percentage out of the whole project was complete? How many did you pick up? How many were delivered?
So following each of the pickups from the annex, we had to conduct a secondary inventory. Now in the first line you see under the visual studio inventory artifact within or not within the scope of work. So on the picture to the bottom right, you see a bin holding builder's plates. Now when we picked up these builder plates, they were not so nicely as the way you see them here. These were all individually wrapped as Christmas presents when we returned them. But when we picked them up, they were all crammed with cardboard and thin, flattened foam, just bulging. And I don't think anyone at MARAD really went through each and every individual plate.
So we often found plates that were not in the scope of work. We found an object number, and it was not in the scope of work. We found plates that did not have any identifying tags. So we did have to contact the client and ask, how do you want us to deal with this? Do you want us to still treat it since it's outside the scope of work? And oftentimes she said, "Yes, please do so." We also had to confirm, as I mentioned, the object numbers, and we had to see if there are any discrepancies. There were some artifacts that had duplicate object numbers. Many of these builder plates had the exact same information. And later on I'll describe what was some of the information on the plates, but they were identical. So I had to send photos to the client saying, "Hey, these two are basically identical according to your records, but we have two copies of them. How would you like us to handle that?"
And the reason I also want to show you these two pictures as you can see the little fluorescent yellow tag underneath the bell with stickers. So that was our visual inventory. So at one point, one of the company owners came to the studio and said, "Well, how do I know these are treated?" And I said, "Because I know," and that's not the answer you tell them. So what we did have to do was not invent, but we had to establish the system so that if anyone came to the studio, they could tell you. So for instance, that bell, the blue indicating it had before treatment picture, the white that it was in the scope of work, the green that the treatment was complete and the pink indicating it was now getting its final photography.
So now we're going to continue with the treatments. So the builder plates, the builder plates were about 61% of the collection, and there were two types, the plastic and the metal plates. Now when I say plastic, according to the clients' records, they were Bakelite, but Evergreen at no point was able to confirm if indeed they were Bakelite or not. There were approximately 430 plastic plates. They were varying sizes, and they were made of plastic mold and the exterior surface let me show you this picture, were mostly black. They had engraved text which had been painted white. Most of the plates were flat and rectangular. Almost all of them had four mounting holes at the corners. There were a select few that still had metal screws in the mounting holes. Some of the plates were damaged by missing corners. Some of them had stains from the metal screws that were still attached on the side. So they did have some staining. Some of the plastic coating on the plates was in such poor condition that they were cracking, delaminating and lifting. We probably had about two in which that black surface was completely gone. All we had was just the paper substrate left.
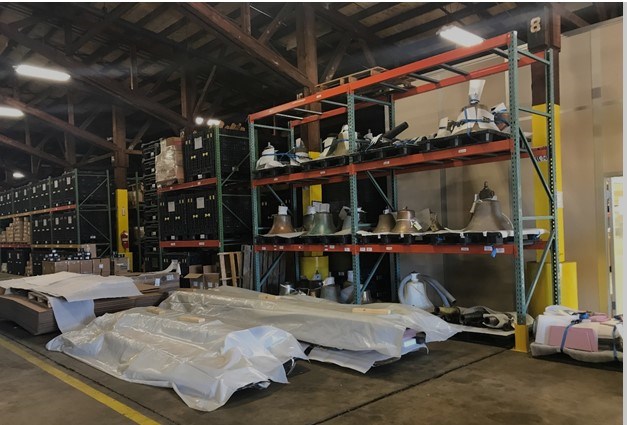
Okay. So the first step in the treatment, I'll go, I'm sorry, I'll go back to the next picture, was removing the labels. And as I mentioned before, we tried to use a mechanical means, but oftentimes we had to resort to wet methods to remove the labels, and we did keep the labels. We placed them into plastic bags and we handed them all back to the client at the end. So we did not throw away anything. We didn't discard anything, not because the client asked us to, but because we didn't want to keep that information. That doesn't do us any good. Some of the labels pertained to older inventory systems that MARAD had or possibly from other organizations that had these artifacts before.
So Orvis paste versus industrial cleaner. Now this plate is looking pretty well. So Orvis, if you're not familiar, is a mild detergent. You can use it to wash farm animals in fact. So it's gentle enough to remove the dirt and for the most part it suited us for our needs. However, as I mentioned, we had plates that had thick layers of paint or they had accretions that were not painted and we weren't able to identify what some of those accretions were. We used Super Clean Industrial Degreaser. Again, you can find that at Home Depot, and our senior conservator opted to use that particular product because as he came up to us one day as we were using the Orvis and he was like, "You know, you're just cleaning the paint layer. You're not actually removing the paint."
"Well that's correct. How would you like us to proceed?" We had to go back and talk to the client, make a change order, and he thought, "You know, these were used in industrial purposes. We should use a degreaser." Now I was horrified because I had never heard of using a degreaser in a conservation lab. That just sounded wrong to me, but it suited our purposes and the Orvis method took about four hours to treat each plate. With the industrial degreaser, we were able to cut that down to 15 minutes per plate. So we were to crank through them. And as a matter of fact, in one month we were able to complete all of the builder plates.
So in this image here we're talking about the delamination of that black top layer that I was referring to. So these were not subject to any type of wet cleaning method. These only had the dry cleaning method, and when I say dry cleaning, we used a vacuum. Sometimes we use the hairdryer, especially for when the delamination was already, or the top layer was already lifting, we could blow out the dust. And here are happy technician is power washing our plates. So once we applied either to the Orvis or the degreaser, we had to rinse them down.
So now the metal builder plates. Very similar to the plastic ones except there were 579 of them, and they were not all rectangular. As you can see, some of them were diamond shaped. Most of the plates were bronze and brass, but others were made of steel, aluminum and lead and the sizes vary from small, when I say small, maybe about 8-1/2 by 11 to large, which is 22 by 28 inches, so it took two people just to lift them and carry them. They also had mounting holes. The lettering was either raised or engraved and some of the letters when they were engraved were filled with enamel paint.
More than half of the metal builder plates had no surface coatings, and so the ones that did often had thick layers of paint on both sides. There were a variety of conditions including heavy tarnishing, moderate and heavy corrosion, and in fact some of the corrosion was the cause for the lifting and the flaking of the paint. I am almost done, I promise.
In addition, there was a yellow surface coating, possibly a varnish, and there were a few plates that had spray painted identification information on the reverse sides because a lot of these plates had the very same data such as Built by the Gulf Shipbuilding Core, Mobile, Alabama, 1943. We must have had at least 15 plates that look just like that.
The first step in the treatment was to assess if the plates were stable or had flaking paint. If the builder plates had no paint, then they were ready to continue with the next process, which is a wet cleaning. Evergreen had attempted to do some of this paint stripping in-house. I'm sorry. Here we go. So this is a plate that had no paint on them, but as you can see, it was mounted on wood. So it was, it had gentle Orvis, and we just had to ensure that the wood was in good condition. The wood mounting was not part of the scope of work, so we did not, if there was any damage to it, we did not assess that.
Now, one of the things I also forgot to mention was that at one point the client wanted to ensure that you could read what the plates said. So it wasn't enough that we were just trying to remove the paint, but we wanted to be sure that you could actually read what the text said. So if you guys can actually read that, you're pretty good.
So we did testing to use the paint strippers, however, there were approximately 174 metal builder plates in which the paint was thickly encrusted. Excuse me. At no point were we going to be able to handle that. So we did have to subcontract that out to get them chemically paint stripped. And in that case of the 174, 78 of the plates came back such that the surface of the metal was aesthetically unpleasant. And when I say unpleasant, they looked like they had the measles. They're just blotches of pinks and yellows on the brass plates. And we're like, "Well, I don't think the client wants them like that." So this technician that you see here in this image, he's applying a patina. So there were about 78 builders plates, which required a patina to again make them look pleasing.
And then the final was the lacquer coating. So we did spray, we sprayed these versus applying them with a brush or anything of that sort. And as you can see here, we have some... maybe some of you all think that's a health and safety concern. If you can't identify the health and safety concerns, I won't point them out to you. But we did our best. You see our technicians have respirators, they have gloves. We have exhausts on the side. We have fans. So we did try to mitigate the best we could with the ability that we could in our studio. So for many of the plates, on the top one, you can see that before, we were able to get into a beautiful after.
So I'd like to thank all of the hardworking technicians. There are about 20 of them, four senior conservators, three project managers, three assistant conservators, and one former vice president of field operations. Thank you all for your attention.
Speaker Bio
Josephina Maldonado is a Conservation Technician with EverGreene Architectural Arts and key team member in the Maryland office. She holds a BS in Chemistry from the University of Texas, as well as a BFA from New Mexico State University. Prior to joining EverGreene, Josefina brings experience from working at the National Air and Space Museum. For this project, she was the Senior Conservation Technician who oversaw the daily operations of this multi-year project; managing the staff, object handling and transportation, client relations, and overseeing conservation treatments carried out by the staff.
Read other articles from this symposium, Preserving U.S. Military Heritage World War II to the Cold War, or learn more about the National Center for Preservation Technology and Training.