Last updated: June 12, 2024
Article
Conservation of a Vietnam-Era Aluminum Swift Boat
This is a transcript of a presentation at the Preserving U.S. Military Heritage: World War II to the Cold War, June 4-6, 2019, held in Fredericksburg, TX. Watch a non-audio described version of the presentation on YouTube.
Conservation of a Vietnam-Era Aluminum Swift Boat for The National Museum of the United States Navy
Presenter: Paul Mardikian
Abstract
This paper describes the challenge of conserving of a 50-foot long Alclad aluminum Patrol Craft Fast (PCF) for the National Museum of the United States Navy on static display at the Washington Navy Yard. The failed coating was removed using ultra high-pressure (UHP) water jetting to NACE WJ-2/SSPC-SP standards at pressures between 30,000 and 40,000 psi, a technique that it is non-abrasive to aluminum, non-toxic and environmentally safe. Following water jetting, corrosion mitigation of the hull and bilge examination, the Swift Boat received a new high-performance coating. This paper outlines the challenges, methodology and techniques employed to preserve the original fabric of this large historic vessel and plans to ensure its long-term stability.
Paul Mardikian: I'm really happy to speak on this project and I want to introduce my co-author Claudia Chemello, who's here. We've had a great opportunity to work with Search. We were hired by Search to conserve this large 50 foot long aluminum swift boat and what I want to say that I have spent 30 years of my life working on military heritage and mostly under water. It was interesting to work on this particular project because on most maritime projects or anything that floats, you have to make the difference between what is going to be preserved functioning in water and what is going to be taken away from the original context and placed in a different environment. And I'm trying to switch slides. It's happened now. Right?
Okay. All right. Oh yeah. Worked much better. The case of this particular boat, which we call PCF-1 because it was number one made between 1965 and 1972. Out of 183 that were made in total, this is PCF-1. So she's not the one right here. This is showing you one of those swift boats. The swift boat is the equivalent if you want in shorter terms of the shell boat for instance, of World War II. It's much smaller. It's made of aluminum, which is slightly different, extremely light, not really sea worthy. This is more for brown water. And what's interesting is that it's made of aluminum. The only thing that is not made of aluminum is the gun turret for good reasons.
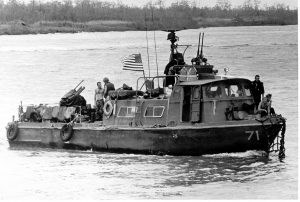
The boat is made of aluminum plates 5086 CC Alclad nomenclature for this particular alloy. And it is very important to talk about this alloy for the restoration project. And I will, I will tell you why. PCF-1 was moved from Coronado, California where it was used as a training boat during the Vietnam War. Never went to Vietnam. And it was de-accessioned in 1994 and put on the Anacostia River Walk outside the Washington Navy Yard as you can see right here. It was dedicated in '98. The boat looks in pretty good shape. However, you had a lot of numerous problems and our contract was to restore the exterior of the boat.
It's in itself a huge task, especially if you're working on a base that is very active and even though it's slightly outside the base, it is considered part of the base and you have people doing their jogging in the morning. It's a very lively place and so you have to take all of that into consideration when you’re trying to restore such a large artifact.
One of the things is that you had, I'm going back to the design, you had several types of swift boats. Mach I, Mach II, and Mach III. And just a way to remember what, how you differentiate a Mach I, which is this one in particular with Mach II and Mach III is that the viewing ports on II and III's are round and these are not. That's easy way to differentiate them. The coating, which we don't know if the coating that we had seen in 2014 was original or not. But what we could say that the coating was failing numerous areas and the epoxy was a blanching and failing in areas where the hull was really corroded, particularly near the bilge of the boat. You can see the clear separation between the layers. It was really very typical of that boat to see those localized failures all around.
What we decided to do was to find the best possible way to remove that paint. We didn't want to do any touch up. We thought that the best way to ensure the long term stability of the boat, even though it's not a floating boat anymore, we wanted to treat it as such and provide the best possible coating. But for that we had to remove the coating and removing the coating can seem like a straight forward task, but in fact it is not. And especially if you're working on aluminum, you'd have to take into consideration the material. And as you know, aluminum is very soft and the a 5086 alloy that I was referring to is called Alclad. Alclad is a an Alcoa nomenclature that means that you have a sandwich of hardened aluminum in the center of your sandwich and on the exterior here have almost pure aluminum and this pure aluminum is protecting the core of your boat and it's providing cathartic protection during corrosion.
You see where I'm going with that. The way to clean the hull is extremely important because if you start abrading this protective layer that had already suffered, it would have led to really a more endangered metal after cleaning than it was before.
I'm just showing you here the scaffolding, full scaffolding access to the crew and also giving the opportunity for people who do their jogging on the an Anacostia River Walk to go through. You see that little door over there to your right. For those who know the place, they will easily recognize. The way we enclose the area was also very important because we are really restrictions from the Navy to work on that boat and do our work. In the background you can see by the way, the John Berry that in 2016 was unfortunately taken to Philadelphia and scraped. It gives you an idea of how fragile this military heritage can be, especially if it's floating. Luckily, for PCF-1, it was placed on the pylons and it's on the ground. I'm repeating, but this is a very important difference when you're working on maritime heritage.
We decided to go with a technique that is essentially ultra-high water jetting. Meaning essentially using pressures that are in the range of 30,000 to 40,000 psi to remove the coating. To give you an idea, if you're using a gas powered pressure washer on your house, most of the time you, I mean the most, you could probably get 3000 psi. You're looking at pressures that are 20 to 25 more powerful for the removal of the coating. And this technique is very useful for the removal of surfaces such as aluminum and it has been shown in the past that this is one of the best technique to achieve that. You've got the gun right here that is used by the team and the nozzle is rotating at 3,000 rpms. That gives you an idea of the pressure and the way it works.
You can also see the anti-skid coating on top of the boat right there. You can look at it. This is the team working on the removal of the coating. Also, we had requirements from the Navy to collect all the effluence and make sure that none of the water would get in the river and it would be collected during all the work. The work took about two weeks from start to finish. Just to show you how quickly water jetting is compared to other techniques. If we had used blasting, like I said, would not have been a good idea in terms of preservation of that Alclad layer. But also we would have produced probably around five tons of dried materials, whatever it is, garnet or aluminum oxide, you name it. But solids that would have been used with all the consequences of damaging the boat.
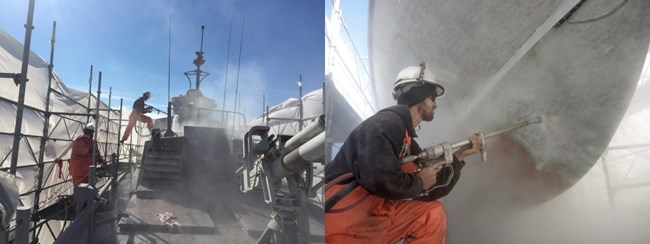
You can see the progress of the work and what's really interesting is that it's a sort of forensic study here of the hull and you are able to see the welding. You can see the way the hull was assembled. You can find markings and you can see the water jetting here, removing different layers of coating and leaving the metal behind. Here you've got examples of cleaned area showing you on the top the left for instance of weld that has corroded and you have those fighting marks that are original to the time the boat was made. On the top right you've got a plug that is clear and very visible. You see a little bit of the green left of the water jetting. The standard that we used, which is a [inaudible] standard, was calling for very clean surface, meaning not everything, every bit of paint could be removed but the water jetting standard that we used called for an extremely clean surface. The new coating would really adhere and would be long lasting.
Bottom last you have original corrosion and you can tell that because you still have paint over there. You see, so you can tell that this corrosion was preexisting. And on the right you have runoffs and you've got an area that was repaired and you see almost as if it had been repaired yesterday. The tool marks and you can really read this surface and learn a lot from it.
And other testimony to water jetting is that we were able to find the original Alclad metal and the stamp. That gives you an idea of the ability to clean the surface without damaging it. And by using the least abrasive technique, we were able to really achieve wonderful results but also get some unexpected drips. I mean not necessarily due to the water jetting, but just due to the fact that this boat had been placed outside for many years and corrosion in the bilge was quite extensive. And so it revealed all those holes in the hull, and of course it didn't take long for us to understand that it was related to the area of the bilge where dirt and water collects and create a corrosion line. This differential aeration between the water in the bilge and the area that is out of the water creates this sort of peaking corrosion that is quite typical.
Well, we spent a lot of time in the bilge trying to clean as much as possible, but once again our goal, or our contract, was not to do that. But we could not, not do it because we had to look and document and let the client know what was going on and we did our best to remove the water and be able to get rid of the oil as well and dispose of all those materials and treat them off site. We didn't do any welding. If the boat had been used to navigate, it could have been a totally different thing. But in that particular case, we decided not to do any welding to the hull and just patched those holes with an appropriate polyester material designed for aluminum and we moved on.
You can see the pilot house being cleaned during, after water jetting here. The cleanness of the surface is quite amazing and of course you have to be careful if your water jetting around rubber or other materials that could be damaged. You really have to have a good team of people, well aware of what your goals are because otherwise you could really create, like anything else, create damage to the surface of the softer materials. We decided to go with an industrial coating and typically several coats of primers of different colors so you can see what you're adding and you measure the dry film thickness of the film as you go until you meet the manufacturer's recommendation. And as you know, epoxy is not really resistant to UV's and so you have to top coat it with a polyurethane. This is what we usually do. Otherwise your coating would fade and start to choke and break down. Those things are quite important as well to keep in mind the system that you're using, the wet you apply, the relative humidity, the thickness of your coating, all these things are extremely important.
Well you have a view of the team working on the application of the paint. We couldn't spray because the Navy didn't want us to spray. And that's understandable because you know, airborne particles, people would breathe those things. And you could have your car nearby coated with a beautiful haze gray and they didn't like that. Of course everything was applied using other means and rolls, and rolling and brushing. You have a view of the hull right here with you know, of course number one because we have this. This is what it is and really proud of having number one there.
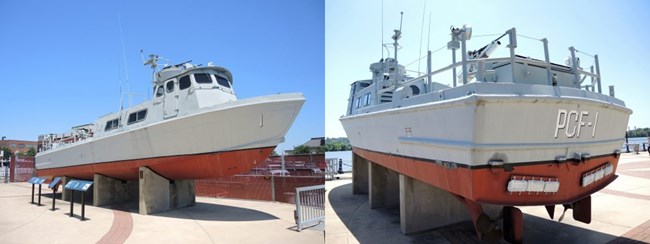
The colors are the colors that the Navy requested and these are the original colors of the swift boat. We have details here of the hull after painting. You've got the anti-skid coating that was real applied to the deck. There was also a gun that was made of rubber and the poor gun had totally [inaudible] and the museum decided to replace the fake gun with a more rigid version. Let's put it that way. And they did. And it looked great. Another view of the boat after all of the deck with the anti-skid. I don't know if many people are going to go on that boat, but the Navy wanted to have something that could be as close as possible from the original. A side view of the swift boat after conservation PCF-1 which is a vinyl. This is not paint that's a vinyl and that's what they wanted. So we applied that at the end of the painting. That's one nice view of a swift boat in Vietnam.
The boat was all mounted on pylons and we were about to glue polyethylene sheets of all under the boat, and there was a slope that was made in such a way that we would be able to collect the water jetting, from the water jetting essentially as it when there was someone dedicated for shop vacuuming the water and transferring that water into a holding tanks. That's how it went. There is no magical way to do it. It's got to be done as it goes.
Questions
Claudia Chemello: Just on that point, the water in the holding tank was emptied I think twice; 4,000 gallons.
Paul Mardikian: Yeah. About eight tons of water were generated during the process.
Claudia Chemello: And the water was tested. I mean it was tested. The paint was tested for lead first. That was the first concern. And then.
Paul Mardikian: Oil.
Claudia Chemello: All the things like that. But the Navy, we had to write a proper safety plan before we got the job. And in one of the things was having the water tested for other things. I just thought it was taken off site, tested and got the results and that was cleared,
Paul Mardikian: But we could not dispose of the water on the base even if the water was crystal clear. It had to be taken out and disposed of and we would have to give a certificate to ensure that had been done and then dumped in the sewer.
Speaker 1: I used to live blocks from there. I used to walk up and down that walkway all the time. I know the project. Did you use a primer at all?
Paul M: Yes.
Speaker 1: Could you go back over the paint system a little bit?
Paul Mardikian: Yeah. The paint system, again, the primer is an epoxy primer. It's a Sherwin Williams product. All the details are in the paper, and I can give you those things if you want to. The only thing that was not Sherwin Williams was the anti-skid material, which is a different brand. But essentially you go with two coats of epoxy and then a top coat of polyurethane. And so if you're interested in knowing a little more about what we do, I'm putting a little barcode that you can photograph and you will go directly to our Instagram account and find our projects. But essentially the name Terra Mare Conservation has a signification. Terra means Earth and Mare means the sea in Latin as you figured out and the reason why we call our company that way is because it's extremely important for us. We worked extensively, I worked a lot under water and [inaudible] worked a lot on terrestrial sites.
For us having a way to bring together those two fields was really important. And this project is a good illustration of this type of approach. And I also want to thank the team from the Navy Yard and NHSC and a team of the museum because they've been really helpful. Those projects are extremely difficult to put together because of the size of the object that you're conserving, and I want to say also that the long term preservation plan doesn't stop here. Doing what we did was a critical phase to put the boat back on track, so to speak. But there's a need for long term maintenance, making sure that a number of critical issues, particularly water getting into the hull because otherwise it might pose problems. Thank you very much.
Speaker Bio
Paul Mardikian is co-founder and senior conservator of Terra Mare Conservation, LLC, a firm specializing in the conservation of cultural heritage, particularly military heritage. Paul has an undergraduate and graduate degree in art history and archaeology from the School of the Louvre and a graduate degree in conservation from the Sorbonne University, Paris. After graduation, he completed post-graduate studies and research in maritime heritage preservation and conservation for Parks Canada and for the Western Australian Maritime Museum where he was an honorary research fellow. Since 1988 he has led conservation efforts for numerous conservation projects including the RMS Titanic (1912), CSS Alabama (1864), H.L Hunley(1863) and Apollo F1 engine recovery and conservation project. Paul has over 30 years of international experience in cultural heritage preservation, and extensive experience with complex conservation programs requiring a multidisciplinary approach and international collaboration. He is a fellow of the American Institute for Conservation of Historic and Artistic Works.
Read other articles from this symposium, Preserving U.S. Military Heritage World War II to the Cold War, or learn more about the National Center for Preservation Technology and Training.