Last updated: April 7, 2025
Article
An Engineer’s Approach to Forecast the Long-Term Effects of Environmental Thermal Cycles on the Aluminum Works in the Artillery Sheds at the Chinati Foundation
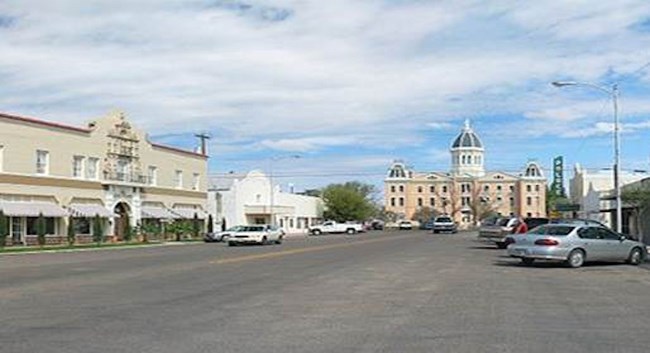
James C. Parker
James C. Parker: Exciting to be here. This will be a change of pace. I’m not going to be talking about the arch, so sorry about that. But I am going to be talking about a project I’m very excited about and very important to me, my firm, and many, many other people. I’m going to be talking about the conservation and preservation of the artillery sheds at Marfa, Texas. In many ways this is a building preservation project of two buildings previously owned by the U.S. Army and then adapted and altered by the artist Donald Judd. But in many more ways, it’s an art preservation project because where in these buildings the artist installation ends and the building starts is not easy to determine, and that was by design of the artists.
I’m going to be speaking about a proposed study in which we will be studying aluminum works of art inside the buildings, understanding the extreme temperature fluctuations that are currently undergoing, and trying to understand what it means for the long-term health of those works in hopes that the knowledge we gain from this study will inform the museum and the members of the project team on some … what appear to be fairly consequential decisions about the conservation.
You need some context, I think, for this project, and the context is southwest Texas. Marfa, Texas, in particular. And to get to Marfa, Texas, you have to drive, and you generally have to drive a long way. During that drive, you can’t help but notice the landscape, in part because the landscape is so beautiful, and part because there’s not a lot of other things along the way to Marfa, Texas. Marfa, Texas, is a small town, population of about 2,000. It was once just a stop on the railroad that replenished the steam locomotives with water, and it’s probably safe to say before Donald Judd and the Chinati Foundation put Marfa on the map, if anybody knew about Marfa, it was because Elizabeth Taylor, Rock Hudson, and James Dean made a movie there once back in the fifties.
But on the south edge of the town is the Chinati Foundation. The Chinati Foundation is a contemporary art museum based on the ideas of its founder and artist, Donald Judd. The mission of the Chinati Foundation is to preserve and present to the public large scale art exhibits from a select few artists. Originally, it was conceived to exhibit the art work of Donald Judd, John Chamberlain, and Dan Flavin. Today in the audience, a co-author of mine, is Patina Lagreavy, who is the director of conservation. It’s also, I think, important to note that recently the Chinati Foundation has recently been put on the world monument watch-list, and it’s very exciting for the institution.
The grounds of the museum occupy 340 acres, which was once the Fort D. A. Russell Military Base. The buildings that remain now that you can see on the right-hand side. Donald Judd started first making interventions and installations with the support of the Dia Art Foundation out of New York City. Here is a photo of the grounds with some of the outbuildings and barracks that still remain. The first installations done on the museum were Donald Judd’s fifteen works in concrete, which are large works all along the eastern perimeter of the property. They become now part of the landscape, if you will, for the Chinati Foundation’s property. You can see then, there on the right-hand side of this image, this aerial view. The U-shape buildings you see in that circular pattern are the remaining barracks, six of which house light installations by Dan Flavin. The two long, slender buildings with the silver roofs are the artillery sheds.
There are other artists’ exhibits, but it’s safe to say the two artillery sheds are the center of Chinati’s permanent installations. They’re two very large buildings. In them are 100 untitled works in aluminum by Donald Judd. Each building is about 350 feet long, one a little bit shorter than the other, and 75 feet wide. They were originally gun sheds, and used to store trucks or tractors that would pull cannons. Along each of the long sides of both buildings were roll-up garage doors, and the trucks would enter one side with the cannons in tow, be serviced and stored, and exit out of garage doors of similar size on the opposite side.
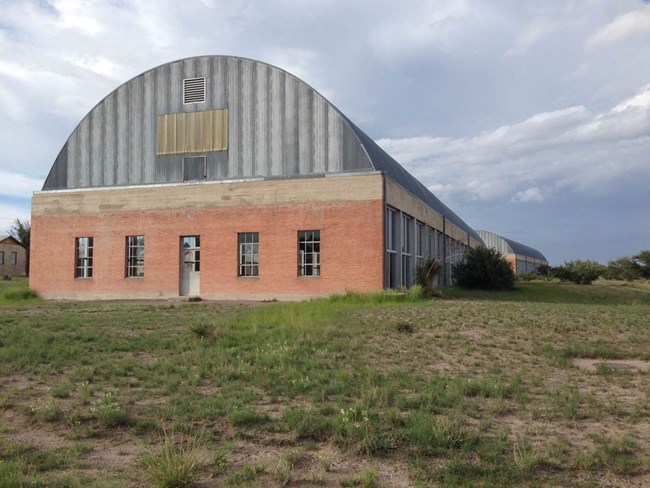
James C. Parker
To say these structures simply house the aluminum works really understates the importance of the structures to the installation and what Donald Judd thought of them. Matter of fact, the writings state that the size and scale of the buildings dictated the nature of the works that he decided to put in them, and such that the works in the buildings become part of one installation. And he modified the buildings for purpose. He removed all the garage doors, and installed windows of his own design of single-pane clear glass that flood the space with light, and that interacts with the milled aluminum works.
The precise fabrication of the aluminum works sits in contrast with the rough surfaces of the board-form concrete and brick walls and industrial floor slabs. Yet, the simplicity of both come together to make a unified whole. The light in Marfa changes throughout the day, and such the interaction of that light with the works changes. This is an image looking east at sunrise, and for me, I see warm, soft surfaces, despite intellectually knowing those are smooth, hard aluminum surfaces. And yet, at the same time of the day, I turn and face the other way. I now see blue, cool surfaces in the aluminum works, but I still see the warm glow of the sunrise in the reflected single-pane glass.
Not only are the pieces and the space that they’re in connected as one, both of them are connected with the landscape, and you kind of sense this when you’re in the buildings and you see the landscape all around you, as well as when you look into the buildings seeing the works. You never look through the buildings to the landscape beyond in the horizon in the distance.
From the archives, in the upper left-hand corner, you can see what the army called the gun shed. And the upper right-hand corner around 1980 you see the buildings as Donald Judd was starting to alter them, and you can see the garage doors in it still. The lower two pictures are the buildings with the garage doors removed and the project underway. As I mentioned, the windows were Donald Judd’s design, and they were fabricated and installed on site. Each window custom fit into the rough opening of the garage doors. I surmise this was so there wasn’t any excess trim. They tried to deal with a prefabricated window sized to fit multiple different garage door sizes.
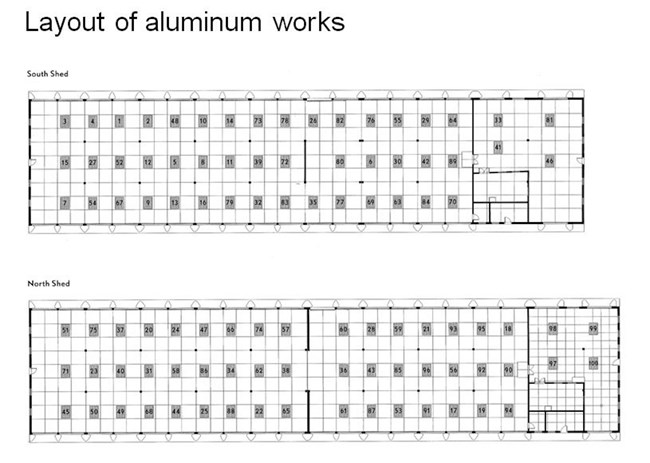
James C. Parker
There are 48 works in the south shed and 52 works in the north shed, each of them put in a particular place by the artist, and each location having a specific design by the artist. All 100 works have the same overall outer dimensions of 41 inches tall, 51 inches wide, and 72 inches long, but every work is of a unique design with different geometry within that volume. This is a fabrication drawing of one of the works. All of the works were fabricated by Lippincott Fabrication in Connecticut, shipped by them to the site and installed over a period from 1982 to 1986. All of the works are made of half-inch thick milled aluminum that is fastened together at the corners with stainless steel threaded fasteners that are counter-sunk. Everywhere an internal plane abuts the planes of plates around the perimeter, they are interconnected with friction-fit hidden blind dowels.
And here are the sheds initially after completion, and you’ll note they don’t have the large barrel arch roofs that they’re known for on them yet. Originally, this was not the thought, but Donald Judd, and I understand, became increasingly frustrated with leaks in the flat roofs. Ultimately decided it was futile to try to repair those flat roofs. That was erroneous, but I guess many feel fortunate that he felt that way because, ultimately, he was inspired by agricultural storage units he saw down the road in Valentine, Texas, and decided to install these barrel arches on both the roofs. And thus, we get the artillery sheds as we know them today, and they are iconic for the Chinati Foundation.
Ironically, it didn’t solve the water problem. The contractor’s decision on how to create a gutter was a complete failure, and Donald Judd was not happy with the results, but the barrel arches come down and are founded on the flat concrete roof right up against and adjacent to a short concrete parapet wall that goes all around the perimeter. So you can see in this image here, the concrete parapet wall and the barrel arch, and you can image that complicated geometry of volume that occupies between the steel arch and the concrete wall, as you have the undulating barrel arch. The contractor filled that complicated volume with sand, sprayed urethane foam on top of it, and covered it with a water-proof coating.
It was never water-tight. The sand became moist and started corroding the bases of the barrel arches. At some time in the past, somebody cut these cute little hatchways in each and every rib of the arch and removed the sand, which was very helpful. But any water that gets past that gutter coating is now pools between the angle that attaches the arches to the base of the concrete floor slab and the back of the parapet wall. This area here is unroofed, so that water gets directly into the space. It goes directly into the space and becomes a headache for Patina.
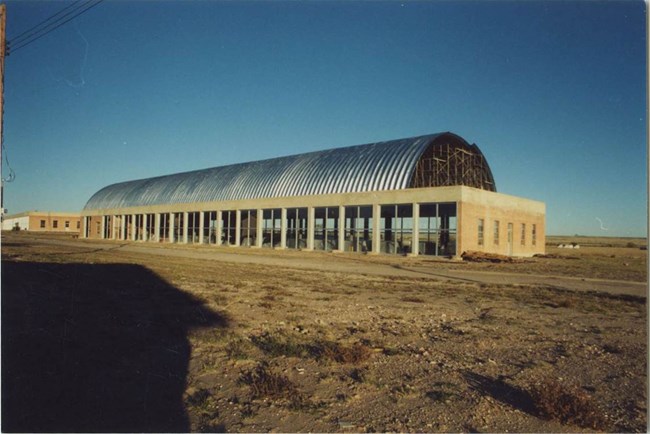
James C. Parker
Even if the gutters were completely water-tight, they were woefully undersized for the volume of water that can be in a downpour in Marfa, Texas, so the water goes over the edge and down the front of the storefront windows, which are now 30 years old. They never did have proper sill flashing underneath them with appropriate M-dams, and they never really had the type of perimeter joint that you would need for a long-term durable seal. Plus, the gaskets are now shot, so much water comes in through Judd’s windows as well. In addition, water that’s been splashing against the concrete curb on the outside has etched the glass and hazed it. And any water that hits the works themselves becomes a labor of love for Patina and her staff to figure out how to clean it.
We know now Judd didn’t like the gutter, and so we can unabashedly come up with an intervention to fix this. We can put an appropriate membrane throughout the attic space on insulation that slopes it. We can put the metal hut on a structural curve that will now form a gutter of reasonable geometry that we can reliable waterproof, as well as handle the volume of water. So this decision is fairly straight, very easy in contrast to the decision of what to do about the storefront windows, as those are the artist’s design. Do we replace them in kind? Do we refurbish them where they are? Or as much more difficult and consequential decision. In particular, when you consider the fact that it gets stifling hot in those spaces throughout the year.
This is results of an energy model that takes one year’s worth of data. You can see the white light lines is the air temperature throughout a year, starting in January and ending in December. Of course, it’s the hottest in the summer. But that jagged nature of that line is telling us that there’s 10 to 20 degrees temperature change each and every day that the aluminum works need to go through. In addition, the two red lines are our model’s predictions of the temperature of the aluminum. The lighter line at the top is the temperature of the aluminum on the sunny side, and the darker red line is the temperature of the aluminum on the interior side. You can see on the sunny side it also goes through daily cycles, and it’s considerably hotter than the air during the winter months. And maybe most importantly it shows that there is a temperature gradient across the work in the winter months between the window side and the interior side.
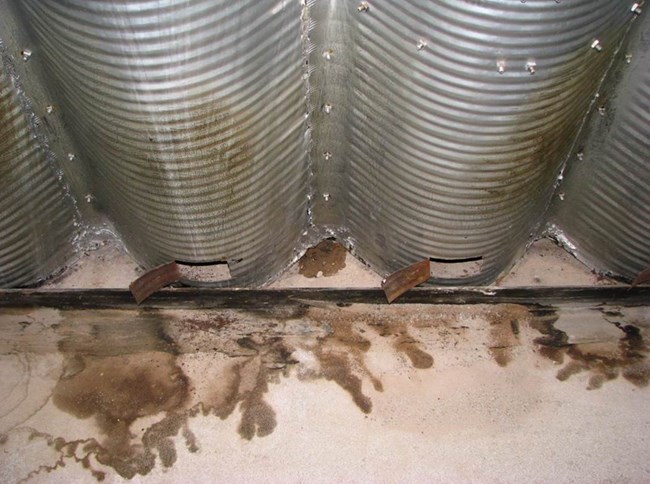
James C. Parker
Undoubtedly, after 30 years of this type of annual exposure, the condition of the works have changed. Exactly how much it’s changed is a current study that Patina and her staff are undergoing, but there’s certain observations that it’s very plausible are the results of this thermal cycling. One of the observations are gaps that are forming between the interior plates and the exterior perimeter plates that you can see here. Some cases it’s as thin as sliding a piece of paper between it. In other cases, it’s as much as an eighth of an inch, and you can start to see the hidden pin dowel that’s between the gaps. Knowledgeable people know that Donald Judd would not have accepted such a gap, so it’s surmise that they weren’t there upon installation.
Additionally, the fasteners at the corners- the thread fasteners at the corners have become loose. They need to be re-torqued, and some of them or a few of them are now such that they are not able to be torqued to their specifications. And they move. Some of the works move more than others. This is a plan view showing of Work #28. It has moved over time. Each one’s going to move differently because they’re all of different geometry. In a way, these aluminum structures are going to respond and behave, and the thermal cycles is going to be a function of that geometry.
So we looked at modeled possible interventions. The upper left-hand graph is the one I described earlier, and then across the top is if we keep single-pane glass. The middle shows that air exchanges can make a slight difference in the overall air temperature, but does not change the daily fluctuations, and it does not have a large impact on the temperatures of the aluminum. If we add HVAC to our model, of course we can tell the model never let the air be hotter than 75 and never less than 65. So the air temperature is controlled, except we still have cycles during the spring and fall, and we still have temperature gradients in cycles in the aluminum.
If we look across the graphs on the bottom, we’re seeing the results of if the single-pane glass is replaced with IGUs and low E. You can see if that’s all that we do, we do make a modest difference in the temperature and the fluctuation, but we make a dramatic change in the temperatures in the aluminum. The aluminum now is not getting the solar gain that it would ordinarily get, so they’re not little heaters in the space. And now the temperatures in the aluminum are essentially averages of the temperature of the air. Air exchanges, as you can see, help, and of course both IGU low E glass and HVAC, you can start to approach conditions that might be more common for the storage of art. However, those of you in this room probably know better than I the consequences of changing single-pane glass to IGUs, and the architectural ramifications. And I think that’s only more acute if you think of this not in terms of architectural ramifications, but in changing an artist’s intention.
If you think about the HVAC equipment, even if it can be hidden up into the attic, the addition of vents throughout the ceiling space would have, definitely, impact on the quality and simplicity of the space. And you can’t tell from this photo, but when you’re experiencing this installation, it’s very quiet and very silent, and there’s concerns about that being marred by the hum of mechanical equipment. So we have to ask, clearly the aluminum works are in conditions well outside norms for storing art, but these are consequential decisions. And is it really necessary? May we better understand the behavior of aluminum in this space. So, being an engineer, I like to look at a graph, and Patina and I used this graph when we spoke with the original fabricator, Alfred Lippincott, who visited Marfa recently.
I can surmise that it’s very likely after 30 years, these works in aluminum have kind of self-acclimated. These opening of gaps and loosening of fasteners are relieving internal strain of the work that goes through the thermal fluctuations, and perhaps, maybe optimistically, that the rate of change is plateauing over time. So perhaps things don’t get much worse if we don’t take these drastic intervention measures. But we don’t know, and this is the subject of the study that we have embarked on. We started by getting a year’s worth of data, where we put data loggers on three of the aluminum works, and we’re getting temperature from multiple locations within each work, and we’re getting temperature within the space and exterior temperatures as well.
Well, we found after a year that it’s actually a little more acute than our preliminary model showed us. We have a maximum aluminum temperatures of over 130 degrees. We get maximum daily change of the aluminum temperatures of above 40 degrees. We’re seeing maximum differential across a work of as much as 20 degrees and peak air temperatures of 111 degrees. And you can see the blue line at the top, you can see how it peaks with morning sun, and the lighter colored line at the bottom that peaks in the afternoon from the western sun.
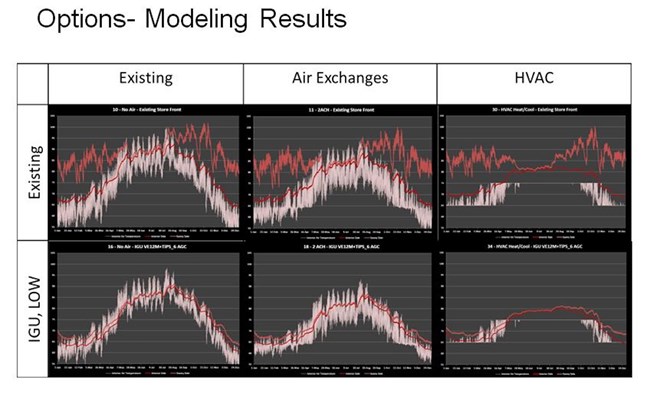
James C. Parker
So we can use this data to calibrate and validate our models. There’s another very important piece of information we need to make the models work, and that’s the emissivity of the aluminum, which is very sensitive to its surface conditions. Unfortunately, you can’t get this non-destructively, so we’re going to have to take small samples and emulate as closely as possible the actual surface conditions of the work so that we can model it appropriately. Essentially, the emissivity is a measure of how much of the solar radiation that hits the surface is absorbed and emitted versus reflected.
But with the data logging and better surface properties, we can do computer modeling, which will be done in two parts. One part will be a whole-building energy model. It will deal with energy plus. And another part will be a finite element model that we build initially of the three works and eventually, perhaps, more as needed. The energy plus model will take care of the outside temperatures, account for solar radiation, re-radiation of the interiors, ultimately giving us temperature of the materials and inside air as a function of time. And ABAQUS finite element model will do heat transfer analysis and structural stress. So essentially, we’ll be taking the energy plus model, it’ll be input into the finite element model, and out of the finite element model, we’ll get aluminum stresses, screw and fast pin forces, and movement.
A little pilot study here that we did for a hypothetical box where we did sequentially heating each of the four sides. The motion that you saw there is exaggerated, but we see in even one cycle we start to get the work to walk even a bit more than 2 millimeters. So we get this data, and the next step is to do the assessment. We’ll be doing the assessment by looking at the stresses and comparing them to material elastic limits. We’ll look at fastener deformations, both analytically and through mechanical testing. And most importantly, we’ll have to look at the fatigue fragility to see when and if we have a risk of cracking.
In conclusion, one: go to Marfa. You will not regret it. It’s a wonderful experience. It’s fair to say that it’s changed me in some ways. Two: become a member of the Chinati Foundation. You’ll be supporting good people doing good work. Clearly these works are in an environment that are well outside the norms of what art would ordinarily be stored in, but the intervention to make a change from that has such consequence that a study to clearly understand the response of the aluminum to these temperature swings would be helpful, not only to the museum, but to the project team that have to ultimately make these difficult decisions. Thank you.
Abstract
Two single-story concrete and brick buildings constructed at Fort D. A. Russell in Marfa, Texas in 1938 are now known as the Artillery Sheds and house internationally important works of art by the renowned minimalist artist Donald Judd (1928 –1994). In 1979 Judd purchased the then-derelict structures. Judd planned significant architectural modifications to the buildings and the 100 mill aluminum works of art they contain together as one vision. Judd’s installation of 73 story-high glass and aluminum windows, of his design, create nearly fully transparent facades. The transparency, in turn, creates an important contextual relationship between the works of art and the landscape, and admits enormous amounts of natural light, the nature of which changes continuously from sun up to sun down. The Judd-designed glass windows and the subsequent addition of aluminum barrel arches on the once-flat roofs, known in the vernacular as the huts, have made the Artillery Sheds iconic of Judd’s works in Marfa.
The Sheds and their works of art are now cared for and opened to the public by the Chinati Foundation. The buildings remain preserved as Judd created them: building elements and materials bare and exposed; interior environment unconditioned and unlit by artificial light; and experience in the space acoustically unaltered by building mechanical and electrical systems. However, the single pane, clear glass of the windows allow for tremendous solar radiation into the space. The aluminum works comprised of rectangular aluminum plates creating box-like sculptures become great sources of heat within the space when they are being struck by sunlight. The surface temperatures of the aluminum in the direct light are much higher than other parts of the given work creating thermal gradients that migrate throughout the day and stress the aluminum. The diurnal and annual temperature fluctuations of the space are well outside ranges commonly sought for the preservation of art. Paradoxically, common strategies to affect the indoor climate, for example sun screens, window shades, coated glass and HVAC systems, all alter the architecture and arguably change the observer’s intrinsic experience with the installation.
Thirty years after installation, the mill aluminum works are undoubtedly changed from their original condition though certainly not detrimentally to the experience of current visitors. Their current condition relative to their original condition is part of an on-going archival study. Some of the works’ locations have shifted over time. Observers have heard pinging sounds emitting from the works as the works heat and cool during the day. There are slight gaps between plates in some of the works, and certain threaded fasteners have needed to be re-torqued; the gaps and loosening of fasteners are plausibly the result of, or at least exacerbated by, the unconditioned environment and resulting thermal cycles on the aluminum works. The extent to which this is the case is unknown. Furthermore, if the gaps and loose fasteners are the result of thermal cycles, it is unknown if the conditions have reached a state of equilibrium, or are degrading at an increasing or decreasing rate. Engineering analysis of the aluminum works can help answer these questions.
This paper presents an engineering approach to determine the effects of the diurnal and annual temperature fluctuations on the mill aluminum works to forecast the probable long-term effects of
continued exposure. The approach includes scientific gathering of material properties, advanced computer modeling for dynamic thermal stress analysis, mechanical testing of replica parts and data logging to validate computer modeling. Knowledge gained from the engineering study could prove helpful in making decisions concerning preservation and conservancy of the Artillery Sheds.
Speaker Biography
James C. Parker is a Senior Principal at Simpson Gumpertz & Heger (SGH).
James received his B.S. in Civil Engineering from the University of Cincinnati and his M. Eng in Structural Engineering from Cornell University. He has 29 years of experience in the structural design of new building projects and in the design of modifications for alterations and repairs to existing facilities. At SGH, James has engineered structures for new and historic buildings and has worked with modern and archaic materials alike. Recently, James has been actively working on the preservation of works by modern artists.
This presentation is part of the Mid-Century Modern Structures: Materials and Preservation Symposium, April 14-16, 2015, St. Louis, Missouri. Visit the National Center for Preservation Technology and Training to learn more about topics in preservation technology.